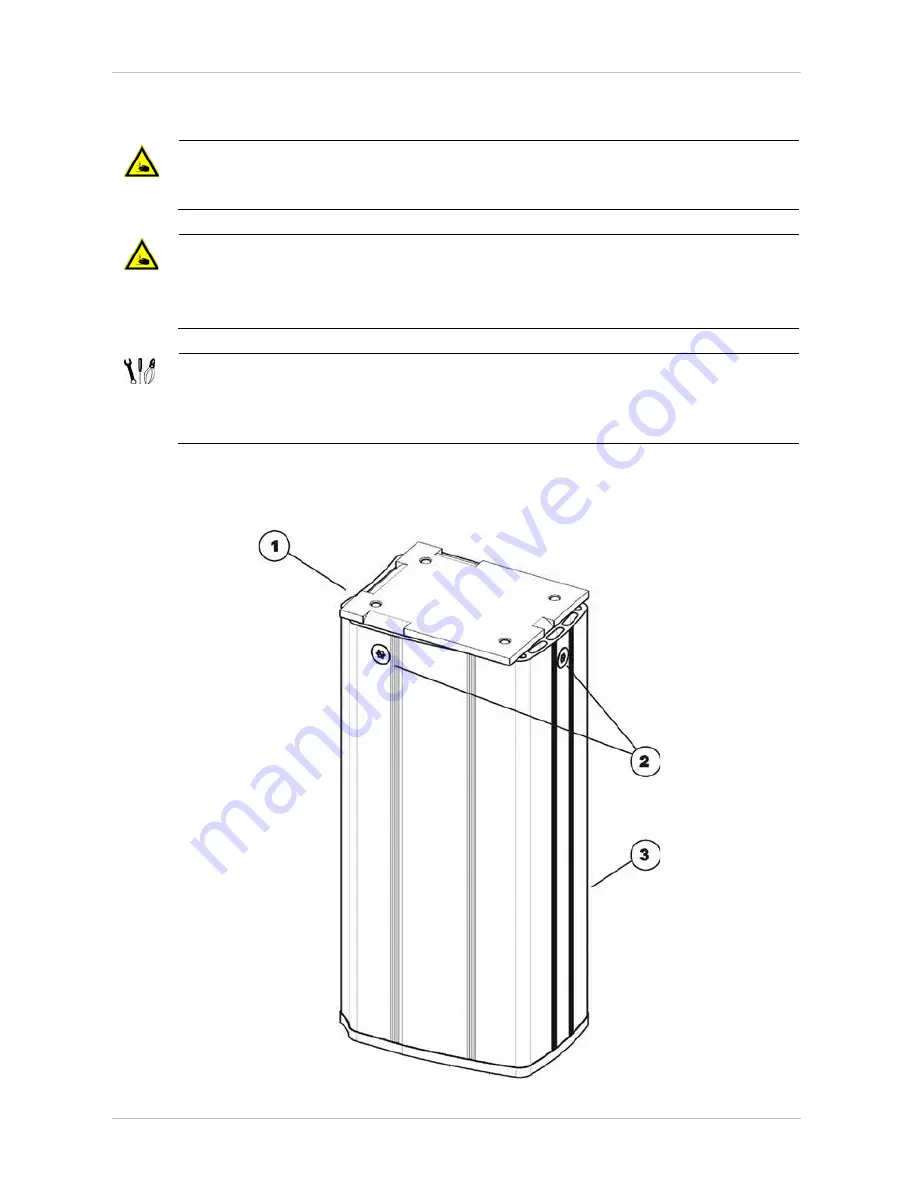
Invacare
®
- STORM
4
MAX
SERVICE MANUAL
119
10.1 Seat height adjustment
WARNING: Danger of crushing!
The seat is very heavy. Injury hazard to hands and feet!
•
You should seek help from a second person.
WARNING: Danger of crushing!
Injury hazard caused by uncontrolled movement of the mobility device!
•
Switch the power supply off (ON/OFF key).
•
Engage the drive.
Requirements:
•
4 mm Allen key
•
T40 torx wrench
•
Oblique pliers
•
Cable ties
Manual seat height adjustment
•
Remove the seat as described in chapter 8.14.1 or 8.14.5.