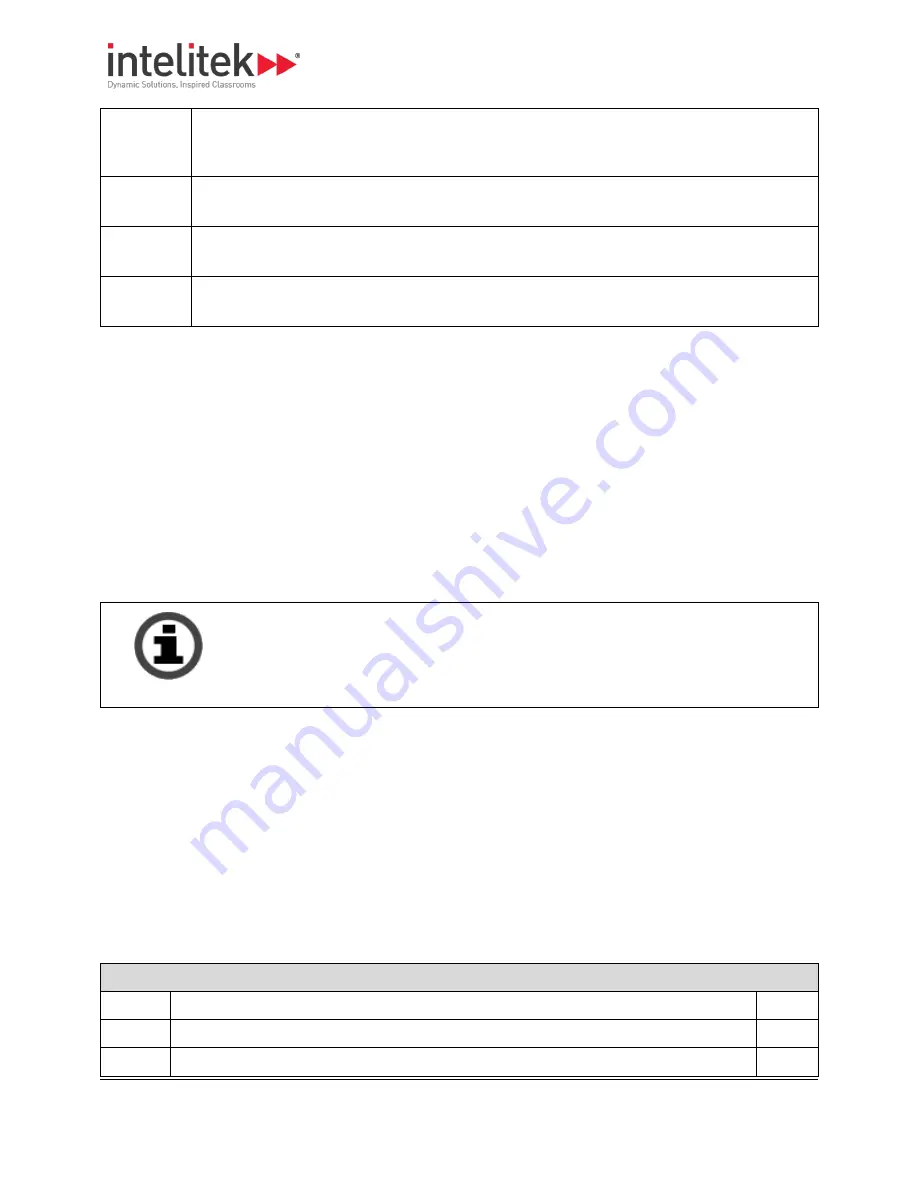
11 An Introduction to CNC Milling
11.5 Tool Types
163
material.
Lubrication
type
Some lubricants can allow for higher feed rates and deeper depths of cut than others.
Cutting
tool type
Some cutting tools are capable of making deeper cuts and maintaining faster feed rates
than others.
Machine
capabilities
Excessive depth of cut and high feed rates place greater strain on the spindle than
allowable.
11.4.
SELECTING LUBRICANTS AND COOLANTS
Lubricants remove heat from the tool and workpiece and are often used when high production rates are
required or when cutting very hard materials, such as stainless steel. A mixture of one part soluble oil to
six parts water may be used on steel to assist in producing a smoother finish and to reduce tool chatter.
Aluminum and aluminum alloys may require the use of paraffin, oil or kerosene to prevent chips from
welding to the tool’s cutting edge. Brass and cast iron are always machined dry.
When lubrication is necessary, small amounts of water-soluble cutting fluids are recommended for use
on the ProMill milling center. Lubricants should be wiped from the machine after use, as some
petroleum-based fluids may damage the electrical wiring insulation and other components.
Short runs of parts on Delrin or aluminium, such as would be performed in a school or college
laboratory, do not require the use of coolant.
Take Note
The ProMill 8000 milling center is designed for flood cooling. A cooling accessory is available.
Contact your dealer or Intelitek.
11.5.
TOOL TYPES
Cutting tools are usually made from hardened steel and are ground to various shapes. The clearances
ground behind cutting edges are adjusted for the type of material the tool will cut and the direction the
tool will be fed along the workpiece. Tools are often ground to shape by the operator to suit a particular
cutting requirement.
Insufficient clearance behind the cutting edge will cause the tool to rub against the workpiece. Excessive
clearance will produce a ridged or wavy finish due to the small length of tool edge in contact with the
workpiece. Standard tool types are: milling tools, side tools, parting tools and boring tools. Carbide
tooling has become popular in recent years. Carbide is more brittle than steel, but has a longer tool life.
The following common tool types are described in the sections that follow:
Section Contents: Tool Types
Section
Name
Page