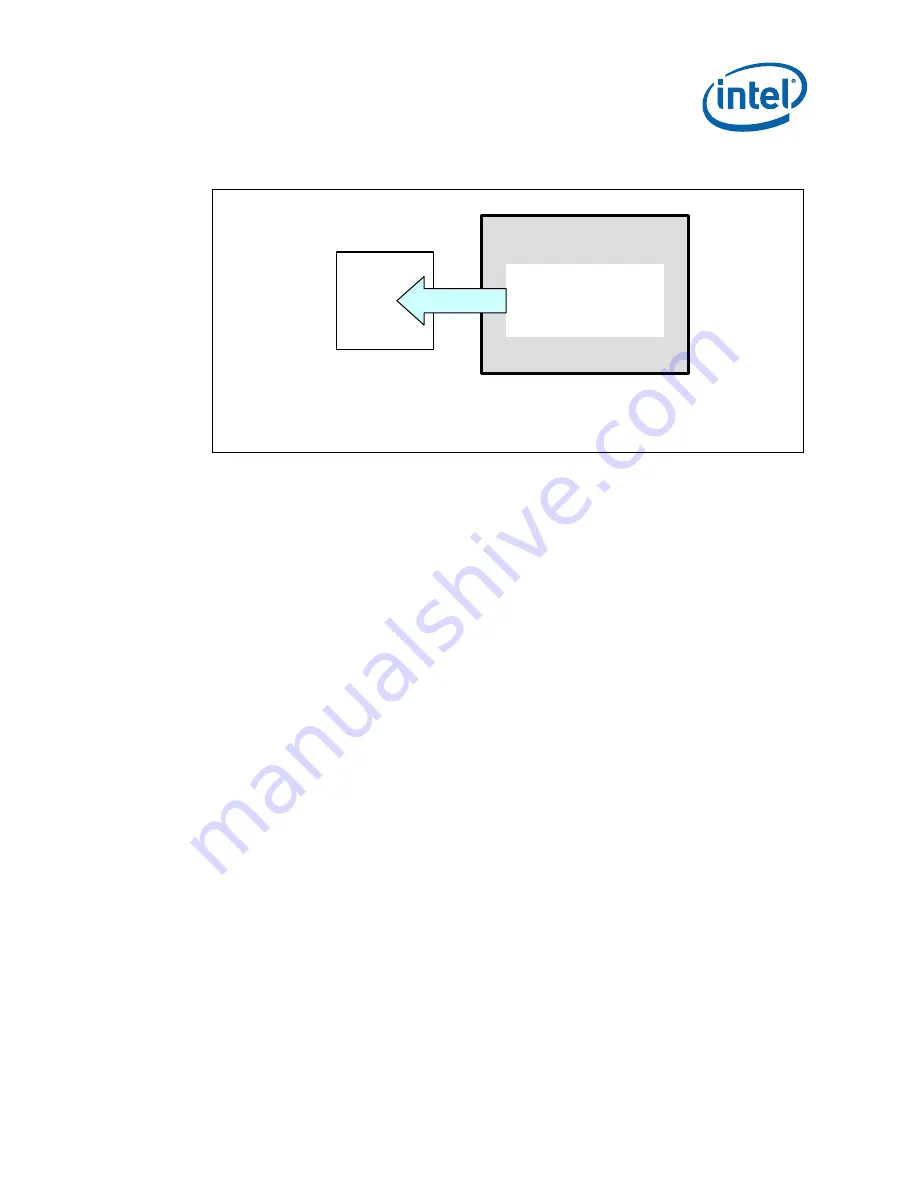
Reference Thermal Solution
Thermal and Mechanical Design Guidelines
23
Figure 8. Processor Heatsink Orientation to Provide Airflow to GMCH Heatsink on a
Balanced Technology Extended (BTX) Platform
BTX Thermal
Module Assembly
over processor
Airflow Direction
GMCH
Top View
4.2
Reference Design Mechanical Envelope
The motherboard component keep-out restrictions for the GMCH for an ATX platform
are included in Appendix B, Figure 12. The motherboard component keep-out
restrictions for the GMCH on a BTX platform are included in Appendix B, Figure 13.
4.3
Thermal Solution Assembly
The reference thermal solution for the GMCH for an ATX chassis is shown in Figure 9
and is an aluminum extruded heatsink that uses two ramp retainers, a wire preload
clip, and four motherboard anchors. Refer to
Appendix B for the mechanical drawings.
The heatsink is attached to the motherboard by assembling the anchors into the
board, placing the heatsink over the GMCH and anchors at each of the corners, and
securing the plastic ramp retainers through the anchor loops before snapping each
retainer into the fin gap. The wire preload clip should be left loose in the extrusion
during the wave solder process. The assembly is then sent through the wave process.
Post wave, the wire preload clip is assembled using the hooks on each of the ramp
retainers. The clip provides the mechanical preload to the package. The mechanical
preload is necessary to provide both sufficient pressure to minimize thermal contact
resistance and to improve solder ball joint reliability. The mechanical stiffness and
orientation of the extruded heatsink also provides protection to reduce solder ball joint
reliability. A thermal interface material (Honeywell* PCM45F) is pre-applied to the
heatsink bottom over an area which contacts the package die.
Note:
The ATX design is similar in appearance to the Intel
®
945G Express Chipset thermal
solution, but two critical items have been changed.
•
A higher performance TIM
•
A clip with a higher preload to meet the TIM preload requirements.
The combination of the two new items provides the performance increase to meet the
GMCH thermal requirements.
Summary of Contents for 82G35
Page 6: ...6 Thermal and Mechanical Design Guidelines...
Page 10: ...Introduction 10 Thermal and Mechanical Design Guidelines...
Page 16: ...Product Specifications 16 Thermal and Mechanical Design Guidelines...
Page 20: ...Thermal Metrology 20 Thermal and Mechanical Design Guidelines...
Page 30: ...Mechanical Drawings 30 Thermal and Mechanical Design Guidelines Figure 11 GMCH Package Drawing...