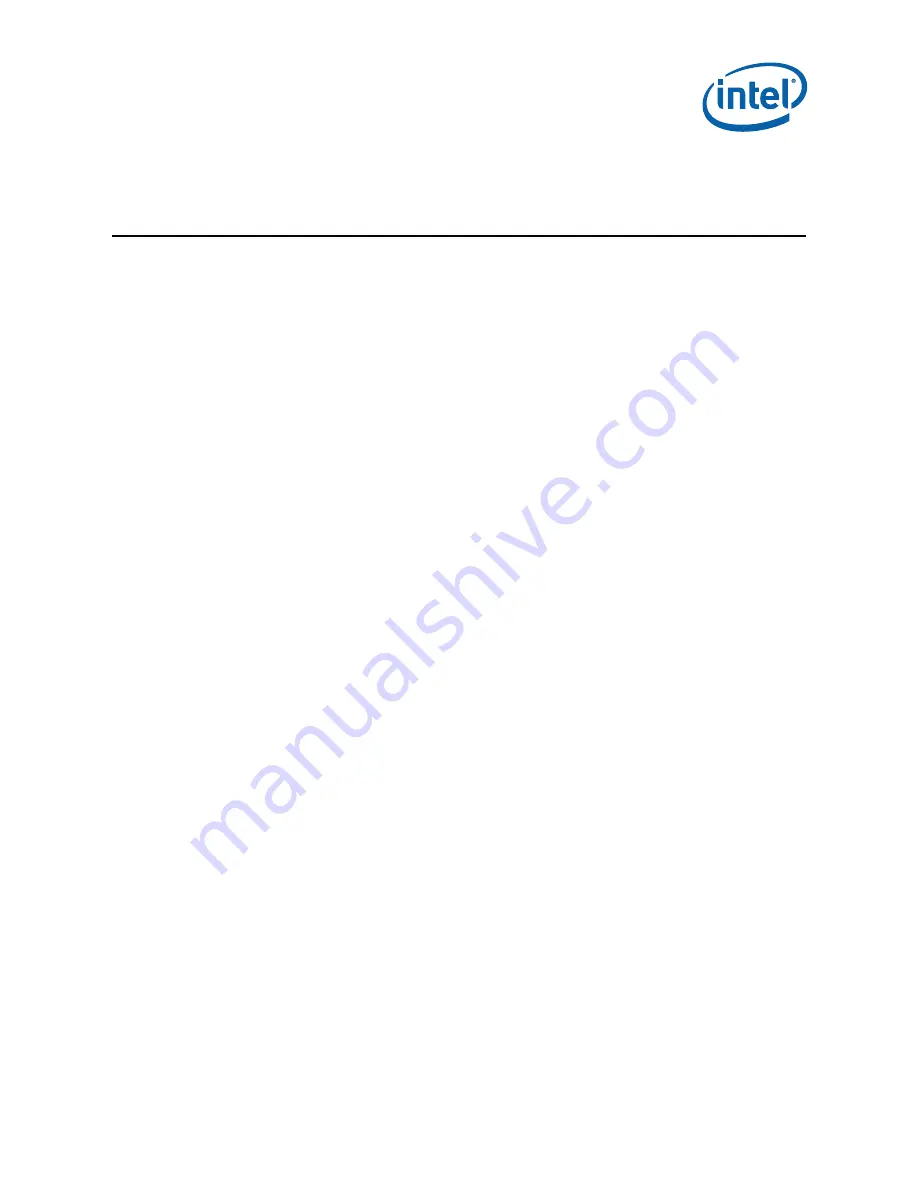
Reference Thermal Solution
Thermal and Mechanical Design Guidelines
21
4
Reference Thermal Solution
The design strategy for the reference component thermal solution for the Intel
®
G35
Express Chipset in ATX platforms reuses the ramp retainer, extrusion design and
anchors from the Intel
®
945G Express Chipset thermal solution. The thermal interface
material and a wire preload clip are being redesigned to meet the Intel G35 Express
Chipset thermal requirements.
The Balanced Technology Extended (BTX) reference design for the Intel G35 Express
Chipset includes a new extrusion, clip with higher preload and a new thermal interface
material. A slightly larger motherboard keep out zone than used by the Intel 945G
Express Chipset thermal solution has been defined, see Figure 13.
This chapter provides detailed information on operating environment assumptions,
heatsink manufacturing, and mechanical reliability requirements for the GMCH.
4.1
Operating Environment
The operating environment of the GMCH will differ depending on system configuration
and motherboard layout. This section defines operating environment boundary
conditions that are typical for ATX and Balanced Technology Extended (BTX) form
factors. The system designer should perform analysis on platform operating
environment to assess impact to thermal solution selection.
4.1.1
ATX Form Factor Operating Environment
In ATX platforms, an airflow speed of 0.76 m/s [150 lfm] is assumed be present
25 mm [1 in] in front of the heatsink air inlet side of the attached reference thermal
solution. The local ambient air temperature, T
A
, at the GMCH heatsink in an ATX
platform is assumed to be 47
°
C. The system integrator should note that board layout
may be such that there will not be 25 mm [1in] between the processor heatsink and
the GMCH. The potential for increased airflow speeds may be realized by ensuring that
airflow from the processor heatsink fan exhausts in the direction of the GMCH
heatsink. This can be achieved by using a heatsink providing omni directional airflow,
such as a radial fin or “X” pattern heatsink. Such heatsink can deliver airflow to both
the GMCH and other areas like the voltage regulator, as shown in Figure 7. In
addition, GMCH board placement should ensure that the GMCH heatsink is within the
air exhaust area of the processor heatsink.
Note that heatsink orientation alone does not ensure that 0.76 m/s [150 lfm]
airflow speed will be achieved.
The system integrator should use analytical or
experimental means to determine whether a system design provides adequate airflow
speed for a particular GMCH heatsink.
The thermal designer must carefully select the location to measure airflow to get a
representative sampling. ATX platforms need to be designed for the worst-case
thermal environment, typically assumed to be 35
°
C ambient temperature external to
the system.
Summary of Contents for 82G35
Page 6: ...6 Thermal and Mechanical Design Guidelines...
Page 10: ...Introduction 10 Thermal and Mechanical Design Guidelines...
Page 16: ...Product Specifications 16 Thermal and Mechanical Design Guidelines...
Page 20: ...Thermal Metrology 20 Thermal and Mechanical Design Guidelines...
Page 30: ...Mechanical Drawings 30 Thermal and Mechanical Design Guidelines Figure 11 GMCH Package Drawing...