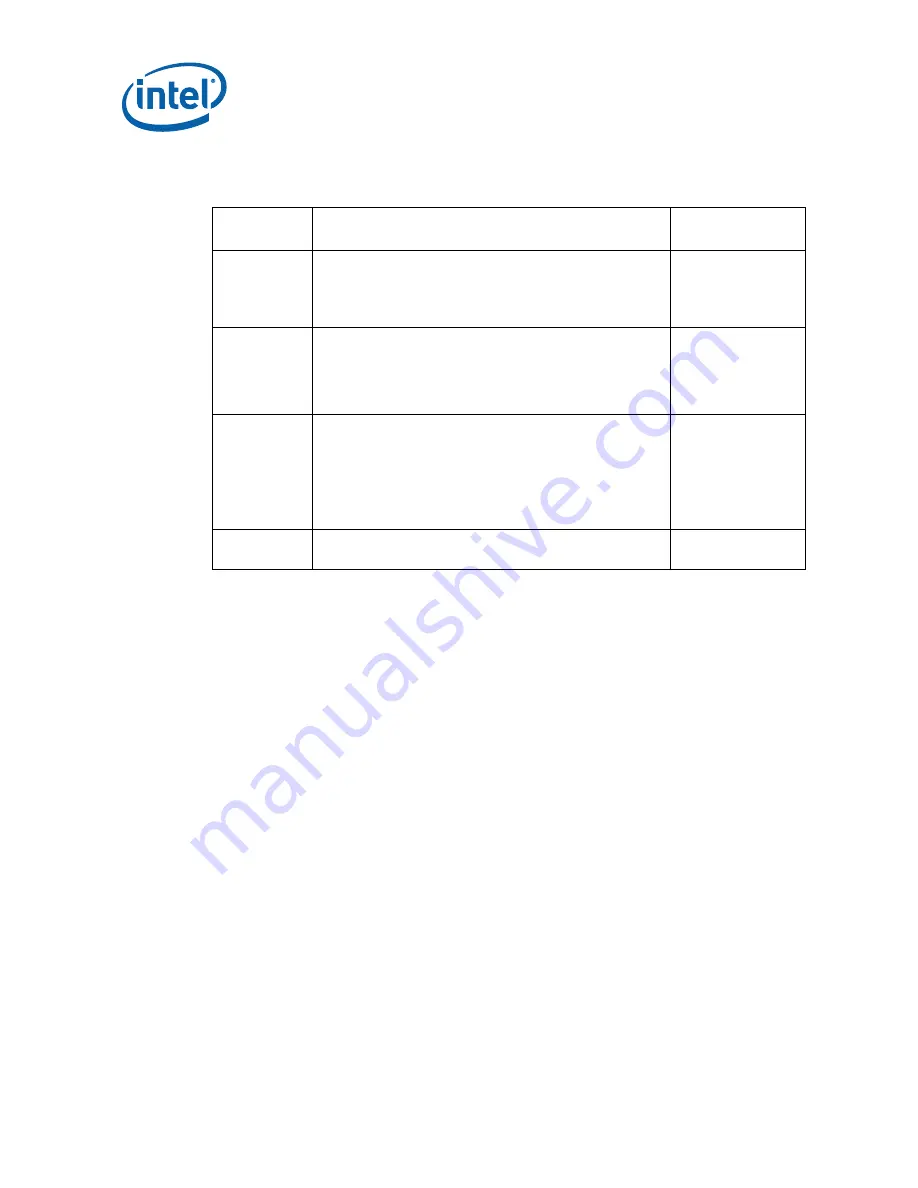
Reference Thermal Solution
26
Thermal and Mechanical Design Guidelines
Table 4. Balanced Technology Extended (BTX) Reference Thermal Solution
Environmental Reliability Requirements (System Level)
Test
1
Requirement Pass/Fail
Criteria
2
Mechanical
Shock
5
•
2 drops for + and - directions in each of 3
perpendicular axes (i.e., total 12 drops).
•
Profile: 25g, Trapezoidal waveform, 5.7 m/s
[225 in/sec] minimum velocity change.
Visual\Electrical
Check
Random
Vibration
5
•
Duration: 10 min/axis, 3 axes
•
Frequency Range: .001 g2/Hz @ 5Hz, ramping to
.01 g2/Hz @20 Hz, .01 g2/Hz @ 20 Hz to 500 Hz
•
Power Spectral Density (PSD) Profile: 2.20 g RMS
Visual/Electrical
Check
Power
Cycling
•
7500 cycles (on/off) of minimum temperature 27 °C /
maximum temperature 96 °C
•
1400 cycles (on/off) of minimum temperature 35 °C /
maximum temperature 96 °C
•
A 15 second dwell at high / low temperature for both
test cycles.
Thermal
Performance
Unbiased
Humidity
•
85 % relative humidity / 55
°
C, 576 hours
Visual Check
NOTES:
1.
The above tests should be performed on a sample size of at least 12 assemblies from 3
different lots of material.
2.
Additional Pass/Fail Criteria may be added at the discretion of the user.
3.
Mechanical Shock minimum velocity change is based on a system weight of 20 to 29 lbs.
4.
For the chassis level testing the system will include: 1 HD, 1 ODD, 1 PSU, 2 DIMMs and the
I/O shield.
5.
BTX reference solution testing for shock and vibration is to mount the sample board in a
BTX chassis in with a thermal module assembly (TMA) having a maximum mass of 900g.
§
Summary of Contents for 82G35
Page 6: ...6 Thermal and Mechanical Design Guidelines...
Page 10: ...Introduction 10 Thermal and Mechanical Design Guidelines...
Page 16: ...Product Specifications 16 Thermal and Mechanical Design Guidelines...
Page 20: ...Thermal Metrology 20 Thermal and Mechanical Design Guidelines...
Page 30: ...Mechanical Drawings 30 Thermal and Mechanical Design Guidelines Figure 11 GMCH Package Drawing...