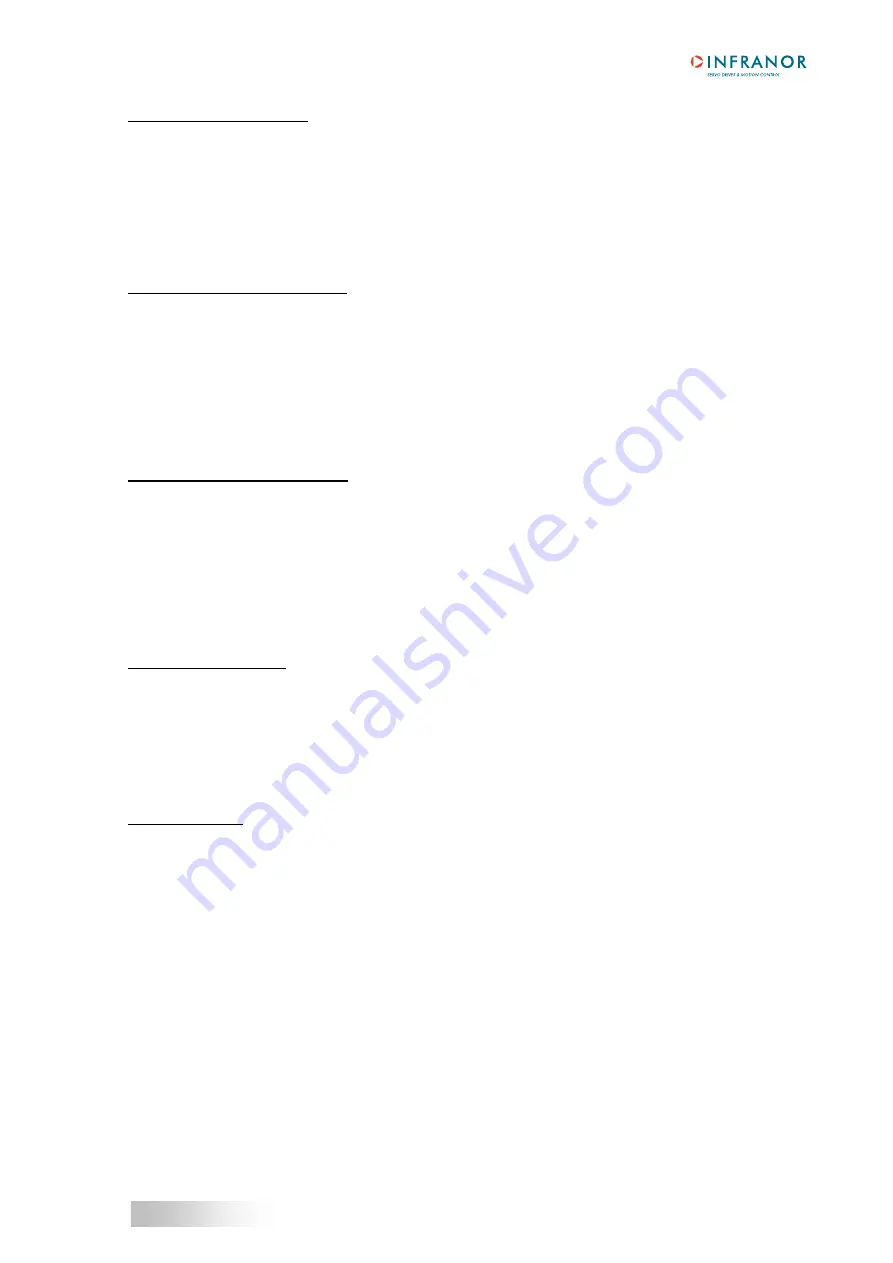
45
SMT-BD1/m
Appendix
Modify speed of a sequence
Instruction US
Parameters
1st parameter: sequence number.
2nd parameter: speed.
If there is no 2nd parameter, the drive will return the actual speed of the sequence (1st
parameter).
Conditions
This instruction can be sent only if no sequence is executed.
The sequence must exist.
The minimum speed is 20 rpm.
Unit
rpm
Modify acceleration of a sequence
Instruction UA
Parameters
1st parameter: sequence number.
2nd parameter: acceleration time.
If there is no 2nd parameter, the drive will return the actual acceleration time of the
sequence
(1st
parameter).
Conditions
This instruction can be sent only if no sequence is executed.
The sequence must exist.
Unit
Second
Range
16 s - 16000 s
Remark
See SMT-BD1/m manual for the "acceleration time" signification
Modify deceleration of a sequence
Instruction UD
Parameters
1st parameter: sequence number.
2nd parameter : deceleration time.
If there is no 2nd parameter, the drive will return the actual deceleration time of the
sequence
(1st
parameter).
Conditions
This instruction can be sent only if no sequence is executed.
The sequence must exist.
Unit
second
Range
16 s - 16000 s
RemarK
SMT-BD1/m manual for the "deceleration time" signification
Execution of a sequence
Instruction GO
Parameters
1st parameter : sequence number.
Conditions
This instruction can be sent only if no sequence is executed.
"Enable" and "Run" signals are activated.
"Wait" and "Stop" inputs are not activated.
The sequence must exist.
Remark
This instruction executes a sequence (with parameter as sequence number) regardless of the
logic
inputs
status.
Position feedback
Instruction PF
Parameters none
Conditions Read
only
Remark
This instruction reads the position of the motor.
Unit