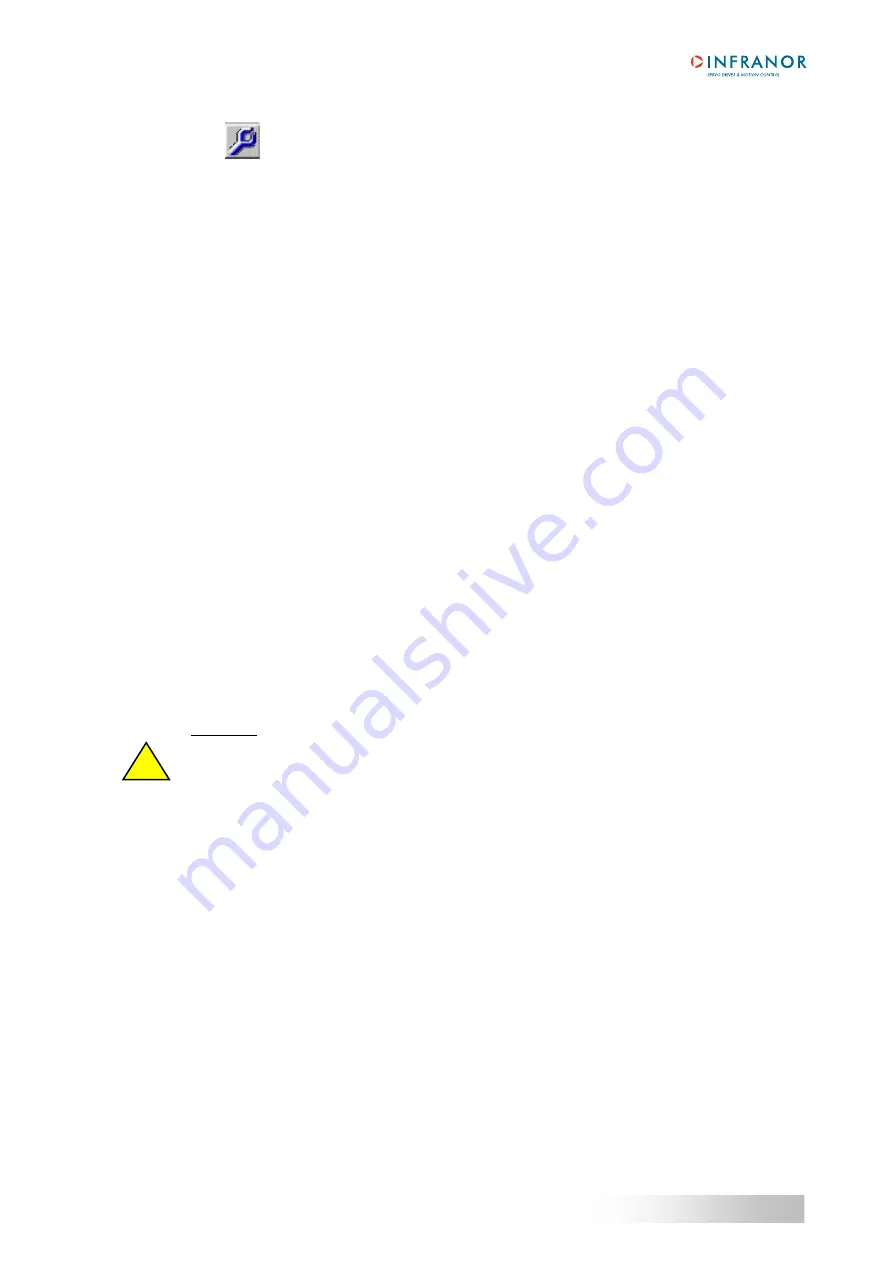
26
SMT-BD1/m
Chapter 6 – Commissioning
4.1 - PARAMETER SETTING OF MOTOR AND DRIVE
(shortcut button
)
The parameter setting software tool allows a quick commissioning thanks to the WIZARD function.
Clicking on the shortcut button will open a new window with several notebook tabs:
Servo motor
,
current limit
,
speed limit
,
encoder output
,
servo loop
.
A
Wizard
function is available at the bottom of the screen for helping the user to the easy and accurate
adjustment of the motor/drive system. The Wizard successively leads through the notebook tabs mentioned
above.
For a best use of the software tool, it is advisable to refer to the VISUAL DRIVE SETUP Manual.
If the user does not want to use the Wizard help, he will have to follow the instructions below:
Select the motor in the
Motor list
.
Check that the "
Current limitation
" parameters are complying with the motor and drive specifications.
It is advisable to use the I
2
t "fusing" mode for the commissioning phases.
If the motor used in the application is not contained in the
Motor list
, proceed like follows:
- Adjust the "
Current limitation
" parameters according to the motor specifications.
- Uncouple the motor from its mechanical load and check that the motor shaft is free and that its rotation over
one revolution is not dangerous for the operator.
- Start
the
Autophasing
procedure.
Check that the "
Speed limitation
" parameters are complying with the motor specifications.
Select the
Encoder resolution
if the encoder emulation is used in the application. The encoder resolution window
also allows to parameter set:
-
the number of ZERO pulses per revolution (1 to 4)
-
the ZERO pulse origin within one revolution (0 to 32767)
-
the ZERO pulse width.
Couple the motor to its load and select the speed regulator (P, PI or PI
2
). In the case of a vertical load,
Start the
Auto-tuning
procedure and check that the axis rotation over one revolution is not dangerous for the
operator. In the case of a vertical load,
In case of loud noise in the motor at standstill or when running, check the transmission rigidity between motor and
load (backlashes in the gears and couplings). If necessary, renew the
Auto-tuning
procedure by selecting a
lower
bandwidth. If the problem remains, renew the
auto-tuning
procedure by activating the
anti-resonance
filter
.
Check that the motor is correctly running in both directions by activating the
logic inputs JOG+
and
JOG-
.
If
necessary, re-adjust the speed regulator parameters by means of the
Stability
button.
4.2 – MOTOR / DRIVE PARAMETER SETTING WITH A VERTICAL LOAD
Execute the
Auto-tuning
procedure with the motor
uncoupled from its mechanical load
in order to initialize the
speed loop gains.
Select the
Limiting
mode of the I
2
Then select the speed regulator type PI
or PI
2
.
Couple the motor to the load and move the axis by means of the digital speed input command until its stall
position where
one axis revolution is not dangerous for operator and machine
.
Then execute the
Auto-tuning
procedure with the motor
enabled at its stall position
(zero speed input
command).
!
WARNING
The auto-tuning procedure should be executed in control mode by the PC and at standstill.
It is the user's responsibility to take the appropriate measures for reducing the risk due to
uncontrolled motions of the axis during the auto-tuning procedure.