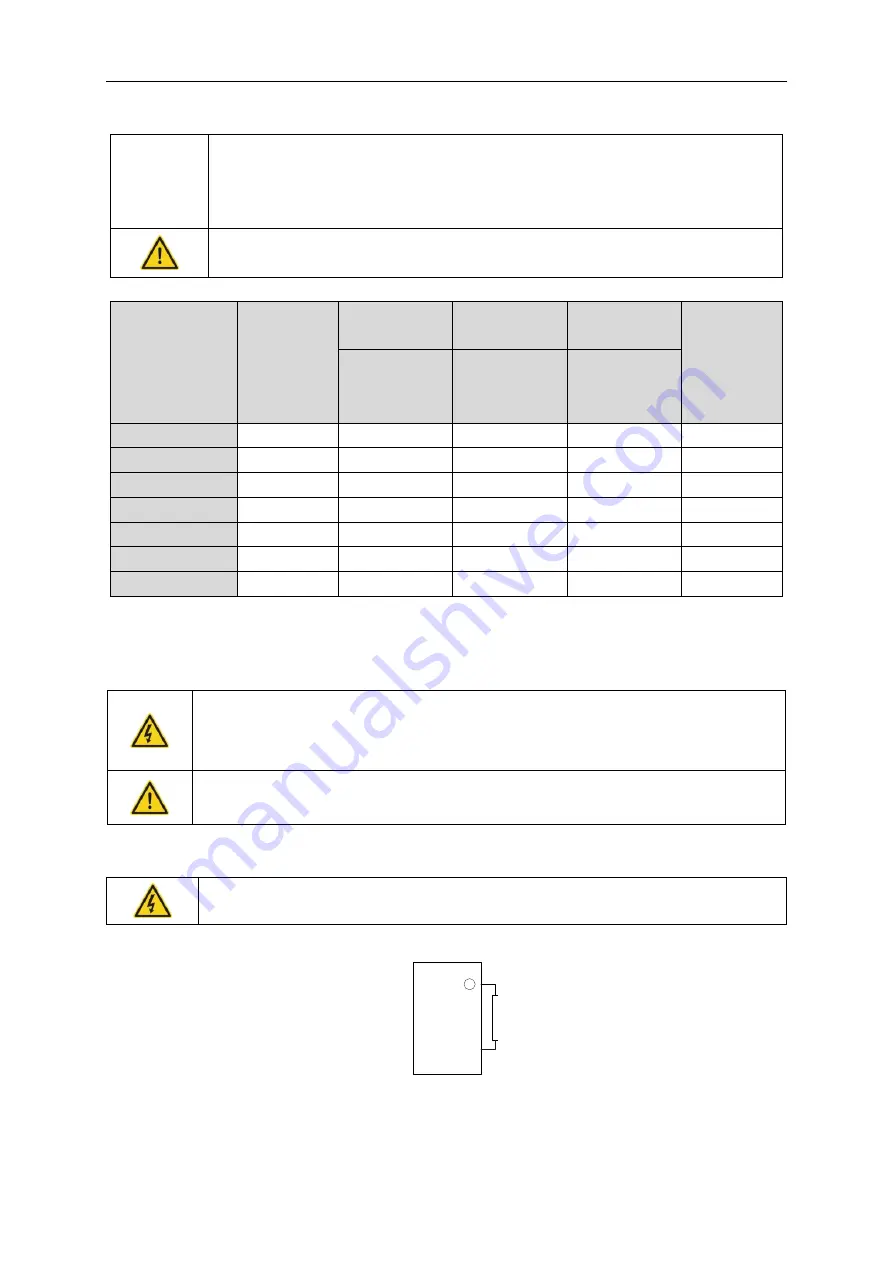
iDrive2 inverters Appendix C Peripherial options and parts
91
connecting them with the inverter.
Do not connect the braking resistor with other terminals except for PB and (-). Damage to
the inverter or braking circuit or fire may occur.
Connect the braking device with the inverter according to the diagram. Incorrect wiring may
cause damage to the inverter or other devices.
Model
Braking
resistor at
100% of the
braking
torque(
Ω
)
Dissipation
power (kW)
Dissipation
power (kW)
Dissipation
power (kW)
Min braking
resistor (
Ω
)
10% braking
50% braking
80% braking
XKL-040-21
361
0.06
0.30
0.48
42
XKL-075-21
192
0.11
0.56
0.90
42
XKL-150-21
96
0.23
1.1
1.8
30
XKL-220-21
65
0.33
1.7
2.6
21
XKL-075-43
653
0.11
0.6
0.9
100
XKL-150-43
326
0.23
1.1
1.8
100
XKL-220-43
222
0.33
1.7
2.6
54
Note:
Select a resistor with wattage and resistance rating as specified in the table above.
The braking resistor may increase the braking torque of the inverter. Above table is measured at 100% braking
torque, 10%, 50% and 80% braking usage rate, the user can select braking level according to duty cycle.
Do not use brake resistor with a resistance below the minimum value specified for the particular
drive. The drive and the internal chopper are not able to handle the overcurrent caused by the
low resistance.
Increase the power of the braking resistor properly in accordance of the duty cycle (the duty
cycle is more than 10%).
C.7.2 Connection of external brake resistor
Install all resistors in a place where they have air clearance.
The materials near the brake resistor must be non-flammable. The surface temperature of the
resistor can be extremely high, ensure sufficient ventilation for heat dissipation.
Only external braking resistor is needed in IMO XKL.
+
PB
E
xte
rn
al
re
sis
to
r