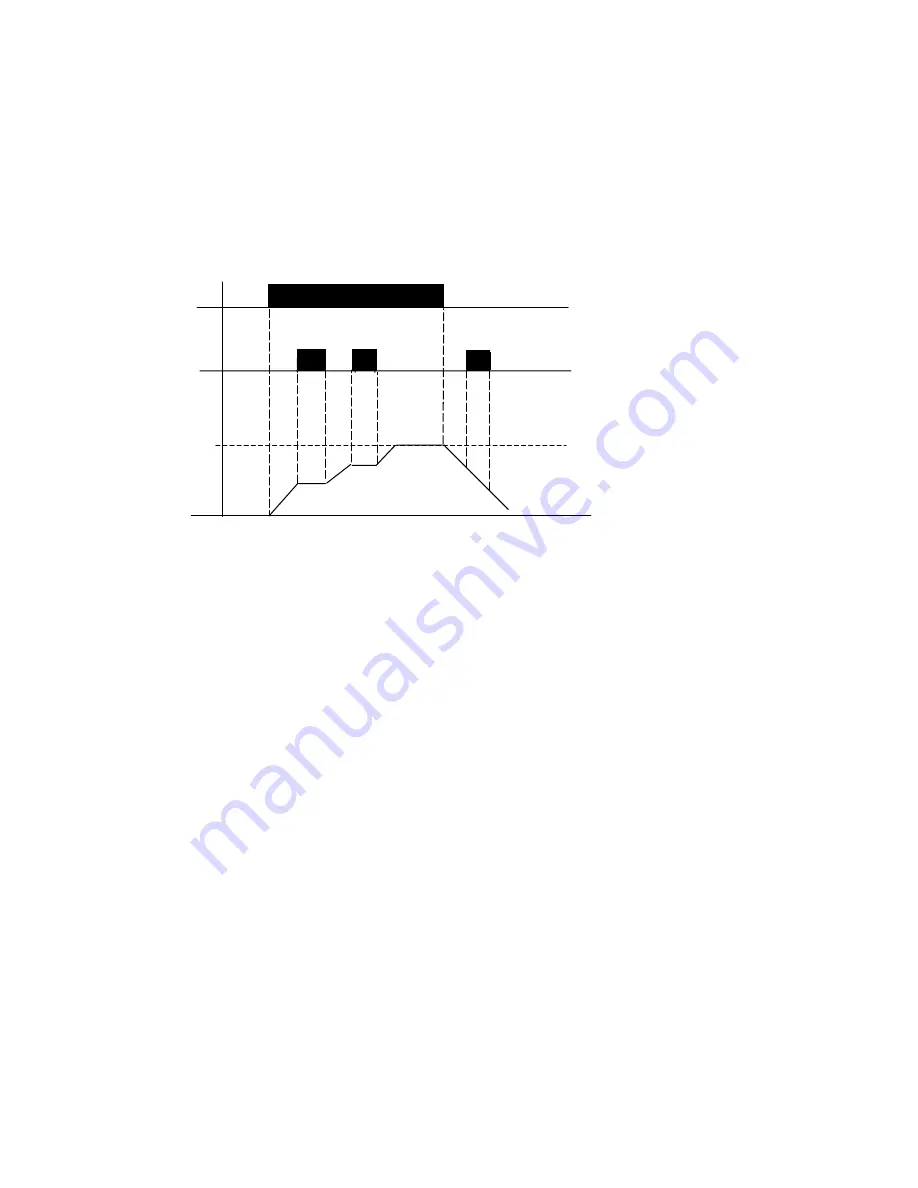
Chapter 4 Software index
4-19
b35 ~ b38 (or b41) = 013: Communication Mode Select.
Terminal OFF
: In communication mode, the
iDrive
is controlled by master (PC or PLC) run and
frequency signals and also allowed to modify parameters. The Keypad and TM2 run/frequency
signal is not available at this time. The Keypad is only available for displaying voltage / current /
frequency and parameters can be read but not modified.
Emergency stop is operational.
Terminal ON
: PC/PLC can read and modify parameters. Note that ALL operating controls are from
keypad. (Not effected by setting of A00 & A01).
b35 ~ b38 (or b41) = 014: Acceleration/deceleration disable.
When external control terminal ON, the
iDrive
will stop accelerating/ decelerating until the signal is
released. The motion is as follows:
b35 ~ b38 (or b41) = 015 Master/Auxiliary speed switch
1) A01 = 001: When one of the parameters b35 ~ b38 (or b41) is set to 015, and terminal is
OFF, the frequency is set by the VR on the Keypad (Master speed).
When multi-function input terminal is ON, the frequency is set by the analog signal on TM2
(Auxiliary speed AIN).
2.) A01 = 002: When one of the parameters b35 ~ b38 (or b41) is set to 015, and terminal is
OFF, the frequency is set by the analog signal on TM2, (Master Auxiliary speed AIN).
When terminal is ON, the frequency is set by the VR on the Keypad (Auxiliary speed).
b35 ~ b38 (or b41)
= 016 (PID function disable)
When input terminal is ON, PID functions set by b67 are disabled.
When input terminal is OFF, PID functions are enabled.
b41
= 017 Analog frequency signal input (Terminal AIN)
Frequency reference is set by 0-10Vdc or 4-20mA on terminal AIN, set by b61 and SW2.
b41
= 018 PID Feedback signal input (Terminal AIN)
PID feedback can be connected to AIN terminal 0-10Vdc/0~20mA or 2~10V/4-20mA as
set by b61 and SW2.
b35 ~ b38 = 019 DC Brake signal
When DC injection is selected (b17~b19) and TM2 DC Brake signal is OFF brake time
is set by value of b17; When TM2 DC Brake signal is ON, DC brake signal is held ON
until either the RUN signal is removed or the DC brake signal is removed (OFF).
Run signal
Acceleration
/deceleration
prohibit
Output
frequency
Note:
Acceleration/deceleration prohibit is
unavailable when Run signal is OFF.
ON
ON
ON
ON