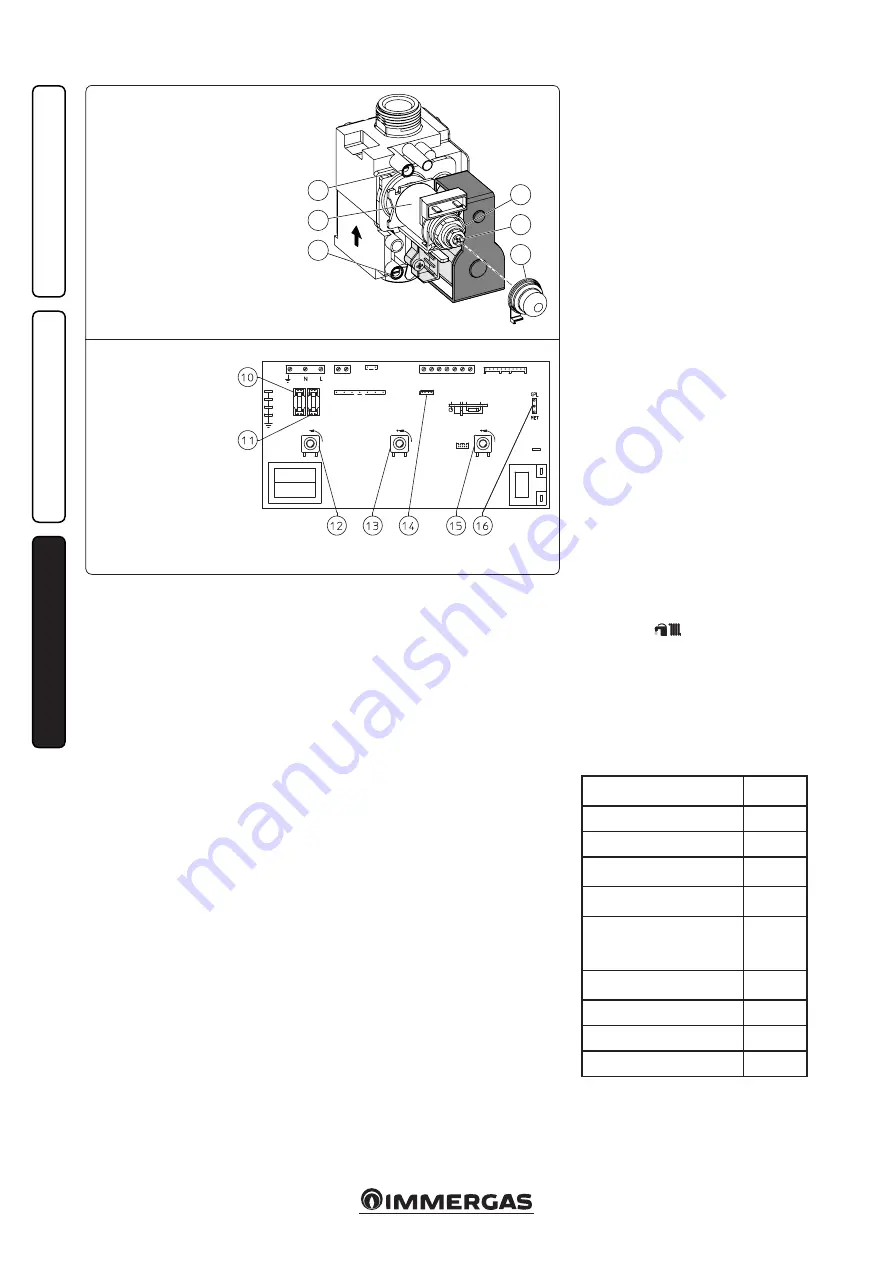
20
3-3
3-4
4
3
2
1
5
6
INS
TALL
AT
O
R
US
ER
MAINTEN
AN
CE
3.4 CONVERTING THE BOILER TO
OTHER TYPES OF GAS.
If the boiler has to be converted to a different gas
type to that specified on the data-plate, request
the relative conversion kit for quick and easy
conversion.
Boiler conversion must be carried out by a
qualified technician (e.g. Immergas Technical
Assistance Service).
To convert to another type of gas the following
operations are required:
- remove the voltage from the appliance;
- replace the main burner injectors, making sure
to insert the special seal rings supplied in the kit,
between the gas manifold and the injectors;
- move jumper 16 (Fig. 3-4) into the correct
position for the type of gas in use (Methane or
L.P.G.);
- to access adjustments on the circuit board the
cover must be removed from the dashboard by
loosening the rear screw fasteners;
- apply voltage to the appliance;
- adjust the boiler maximum heat power;
- adjust the boiler minimum heat power;
- adjust (eventually) the heating power;
- seal the gas flow rate devices (if adjusted);
- after completing conversion, apply the sticker,
present in the conversion kit, near the data-plate.
Using an indelible marker pen, cancel the data
relative to the old type of gas.
These adjustments must be made with reference
to the type of gas used, following that given in the
table (Para. 3.16).
3.5 CHECKS FOLLOWING CONVERSION
TO ANOTHER TYPE OF GAS.
After making sure that conversion was carried out
with a nozzle of suitable diameter for the type of
gas used and the settings are made at the correct
pressure, check that:
- there is no flame return in the combustion
chamber;
- the burner flame is not too high or low and that
it is stable (does not detach from burner);
- the pressure testers used for calibration are
perfectly closed and there are no leaks from the
gas circuit.
N.B.:
All boiler adjustment operations must
be carried out by a qualified technician (e.g.
Immergas Assistance Service). Burner adjustment
must be carried out using a differential “U” or
digital type pressure gauge, connected to the
pressure point located above the sealed chamber
(part. 2 Fig. 1-30) and the gas valve pressure outlet
(part. 4 Fig. 3-3), keeping to the pressure value
given in the tables (Para. 3.16) according to the
type of gas for which the boiler is prepared.
3.6 POSSIBLE ADJUSTMENTS OF THE
GAS VALVE.
• Adjustment of boiler nominal heat output (Fig.
3-3).
- Turn the domestic hot water selector knob (10
Fig. 2-1) to the maximum functioning position;
- open the domestic hot water cock in order to
prevent modulation intervention;
- adjust the boiler nominal power on the brass nut
(3), keeping to the maximum pressure values
stated in the tables (Para. 3.16) depending on
the type of gas;
- by turning in a clockwise direction the heating
potential increases and in an anti-clockwise
direction it decreases.
• Adjust the boiler minimum thermal input (Fig.
3-3).
N.B.:
only proceed after having calibrated the
nominal pressure.
Adjustment of the minimum thermal input is
obtained by operating on the cross plastic screws
(2) on the gas valve maintaining the brass nut
blocked (3);
- disconnect the power supply t the modulating
reel (just disconnect a faston); By turning the
screw in a clockwise direction, the pressure
increases, in an anti-clockwise direction it
decreases. On completion of calibration, re-apply
the power supply tot he modulating reel. The
pressure to which the boiler minimum power
must be adjusted, must not be lower than that
stated in the tables (Para. 3.16) depending on the
type of gas.
N.B.:
to adjust the gas valve, remove the plastic
cap (6); after adjusting, refit the cap and screw.
3.7 PROGRAMMING THE CIRCUIT
BOARD.
The Zeus kW boiler is prepared for possible
programming of several operation parameters.
By modifying these parameters as described
below, the boiler can be adapted according to
specific needs.
To access the programming phase, proceed as
follows: position the main selector switch on
Reset for a period of time between 15 and 20
seconds (after about 10 sec. LEDs 2 and 3 will
start to flash at the same time. Wait for this to
end and re-position the main selector switch on
domestic water and heating). At his point, re-
position the main selector switch on domestic
water-heating (
).
When the programming phase has been activated,
enter the first level where it is possible to choose
the parameter to be set.
The latter is indicated by the fast flashing of one
of the LEDs between 1 and 8 (Fig. 2-1).
Selection is made by turning the domestic hot
water temperature selector switch (10). For
association of the LED to the parameter, see the
following table:
List of parameters
Flashing
LED (fast)
Minimum heating power
LED 1
Maximum heating power
LED 2
Heating switch-on timer
LED 3
Heating power output ramp
LED 4
Heating switch-on delay on request
from Environmental Thermostat,
Digital Remote Control or Remote
Friend Control
V2
LED 5
Domestic water thermostat/Boiler
hysteresis
LED 6
Circulating pump functioning
LED 7
Functioning gas
LED 8
Boiler mode
LEDs1 and 8
Once the parameter to be modified has been
selected, confirm by turning the main selector
switch to Reset momentarily until the LED relative
to the parameter switches-off, then release.
SIT 845 gas valve
Key:
1 - Coil
2 - Minimum power adjustment screws
3 - Maximum power adjustment nut
4 - Gas valve outlet pressure point
5 - Gas valve inlet pressure point
6 - Protection hood
Zeus 24-28 kW circuit board
10 - Line fuse 3.15AF
11 - Neutral fuse 3.15AF
12 - Main selector switch
13 - Domestic water temperature trimmer
14 - RS232 computer interface
15 - Heating temperature trimmer
16 - METHANE L.P.G. gas type selector
Summary of Contents for ZEUS 24 Superior
Page 1: ...ZEUS 24 28 kW IE Instruction booklet and warning 1 038761ENG...
Page 26: ......
Page 27: ......