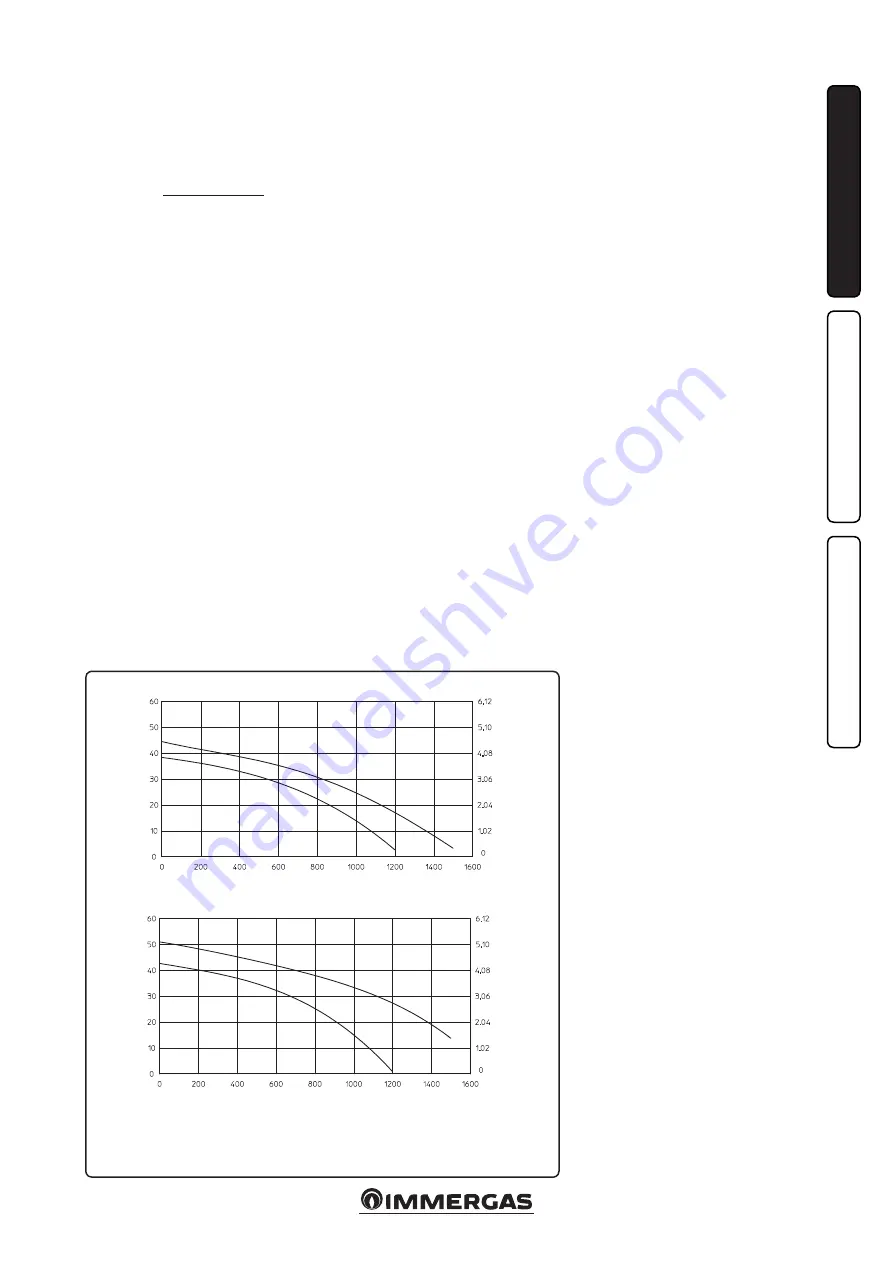
13
A
B
A
B
1-29
INS
TALL
AT
O
R
US
ER
MAINTEN
AN
CE
1.11 SYSTEM FILLING.
Once the boiler is connected, proceed with system
filling via the filling valve (Fig. 2-2).
Filling is performed at low speed to ensure release
of air bubbles in the water via the boiler and heating
system vents.
The boiler has a built-in automatic venting valve
on the circulator.
Check if the cap is loose.
Open the
radiator air vent valves.
Close vent valves only when water is delivered.
Close the filling valve when the boiler pressure gauge
indicates approx. 1.2 bar.
N.B.
: During these operations, turn on the
circulating pump at intervals by means of the
main selector switch on the control pane.
Vent the
circulation pump by loosening the front cap and
keeping the motor running.
Re-tighten the cap afterwards.
1.12 GAS SYSTEM START-UP.
To start up the system proceed as follows:
- open windows and doors;
- avoid presence of sparks or naked flames;
- bleed all air from pipelines;
- check that the internal system is properly sealed
according to specifications.
1.13 BOILER START-UP (LIGHTING).
For issue of the Declaration of Conformity provided
for by Italian Law, the following must be performed
for boiler start-up:
- check that the internal system is properly sealed
according to specifications;
- ensure that the type of gas used corresponds to
boiler settings;
- switch on the boiler and ensure correct ignition;
- make sure that the gas flow rate and relevant
pressure values comply withthose given in the
manual (Para. 3.16);
- ensure that the safety device is engaged in the event
of gas supply failureand check activation time;
- check activation of the main circuit-breaker
selector upstream from theboiler and on the unit;
- check that the concentric intake/exhaust terminal
(if fitted) is not blocked.
The boiler must not be started up in the event of
failure to comply with any of the above.
N.B.:
The boiler preliminary check must be carried
out by a qualified technician. The boiler warranty is
valid as of the date of testing. The test certificate and
warranty is issued to the user.
1.14 DOMESTIC HOT WATER BOILER
DEVICE.
The Zeus kW boiler is the accumulation type with
a capacity of 45 litres. It contains a large coiled
stainless steel heat exchanger pipe, which allows to
notably reduce hot water production times. These
boilers built with stainless steel casing and bottoms,
guarantee long duration. The assembly concepts and
welding (T.I.G.) are implemented to the minimum
detail to ensure maximum reliability.
The lower inspection flange ensures practical control
of the boiler and the coiled heat exchanger and easy
internal cleaning. The domestic water attachments
are found on the flange cover (cold inlet and hot
outlet) and also the magnesium anode holder cap,
including the latter, supplied as standard for internal
protection of the boiler from possible corrosion.
N.B.:
every year a skilled technician (e.g. Immergas
Authorised After-sales Service), must check the
efficiency of the boiler’s Magnesium Anode. The
boiler is prepared for introduction of the domestic
water re-circulation connection.
1.15 CIRCULATION PUMP.
Zeus kW Range boilers are supplied with a built-in
circulation pump with 3-position electric speed
control. The boiler does not operate correctly with
the circulation pump on first speed. To ensure op-
timal boiler operation, in the case of new systems
(single pipe and module) it is recommended to
use the circulation pump at maximum speed. The
circulation pump is already fitted with a capacitor.
Pump release.
If, after a prolonged period of inac-
tivity, the circulation pump is blocked, unscrew the
front cap and turn the motor shaft using a screwdri-
ver. Take great care during this operation to avoid
damage to the motor.
1.16 KITS AVAILABLE ON REQUEST.
• Kit of system shutoff valves (on request). The
boiler is designed for installation of system shutoff
valves to be placed on delivery and return pipes
of the connection assembly. This kit is particularly
useful for maintenance as it allows the boiler to be
drained separately without having to empty the
entire system.
• System zone Kit (on request). If the heating system
is to be divided into several zones (max. three), in
order to interlock them with separate adjustments
and to keep water flow rate high for each zone,
Immergas supplies zone system kits by request.
• Polyphosphate batching kit (on request). The
polyphosphate dispenser Reduces the formation
of lime-scale and preserves the original heat
exchange and domestic hot production water
conditions. The boiler is prepared for application
of the polyphosphate dispenser kit.
The above kits are supplied complete with instruc-
tions for assembly and use.
A = Total head available to the plant on the third speed (screws tightened by 1.5 revs with
respect to the completely loose adjustment screws)
B = Total head available to the plant on the second speed (screws tightened by 1.5 revs
with respect to the completely loose adjustment screws).
Total head available to the plant.
To
ta
l h
ea
d (m H
2
O)
Capacity (l/h)
To
ta
l h
ea
d (kP
a)
Zeus 24 kW
Zeus 28 kW
To
ta
l h
ea
d (m H
2
O)
Capacity (l/h)
To
ta
l h
ea
d (kP
a)
Summary of Contents for ZEUS 24 Superior
Page 1: ...ZEUS 24 28 kW IE Instruction booklet and warning 1 038761ENG...
Page 26: ......
Page 27: ......