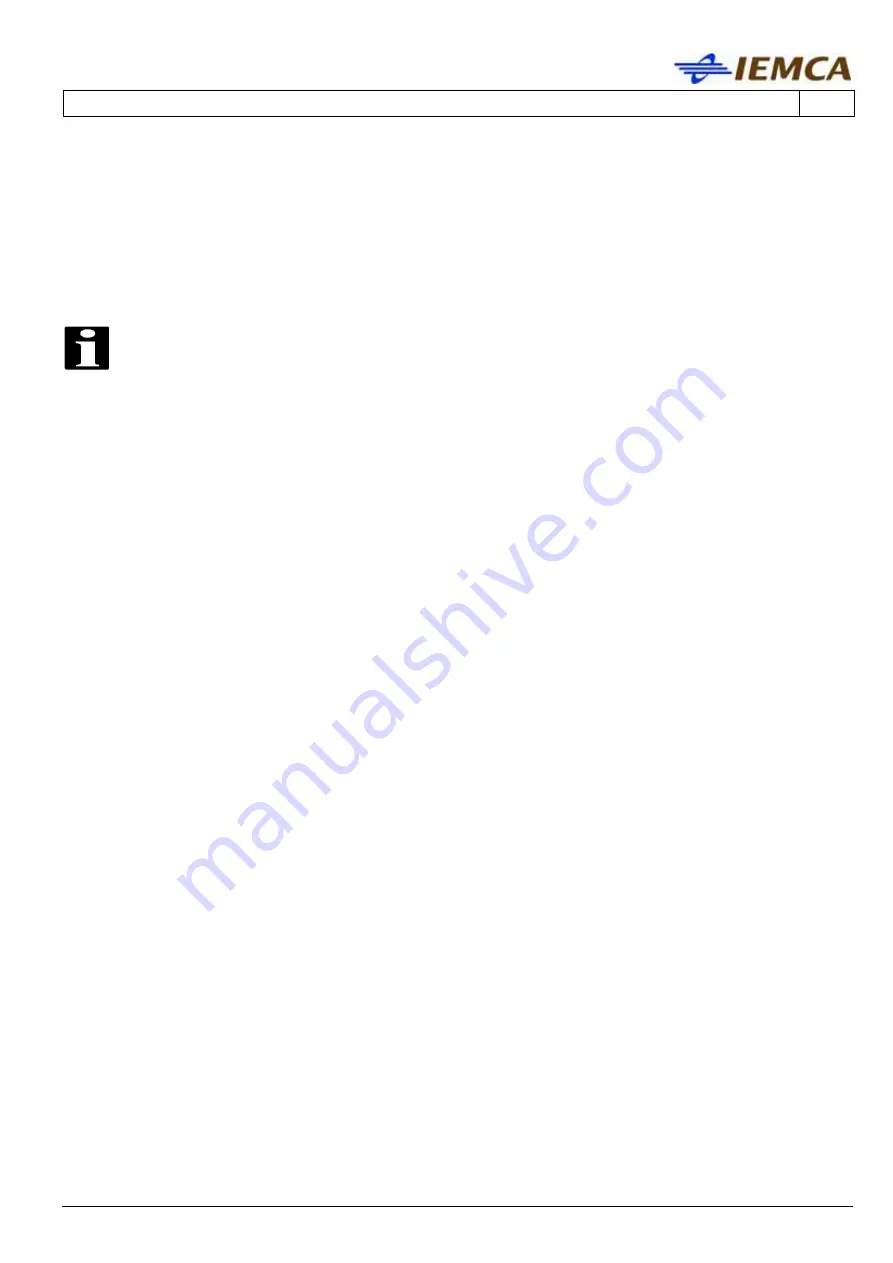
5 - ADJUSTMENTS AND SETUP
VIP80E-II
EN
5 - Pag. 5 / 8
5.4
MAGAZINE ADJUSTMENT (SQUARE BARS)
Parameter setting
- from the operator panel access parameter 16 "Bar Type" and enter value 3, corresponding to
the square bar;
- access parameter 8 "Bar Diameter" and set the diameter of the bar to be machined.
INFORMATION:
For further information on the modification methods of parameters, refer to the
"Instruction manual" which you can find attached.
Summary of Contents for VIP80E-II
Page 2: ......
Page 4: ......
Page 6: ......
Page 8: ......
Page 10: ......
Page 16: ...EN 1 INFORMATIONS GÉNÉRALES VIP80E II 1 Pag 6 6 ...
Page 44: ...EN 2 TECHNICAL INFORMATION VIP80E II 2 Pag 28 28 ...
Page 50: ...EN 3 SAFETY PROCEDURES GENERAL INFORMATION VIP80E II 3 Pag 6 6 ...
Page 80: ...EN 5 ADJUSTMENTS AND SETUP VIP80E II 5 Pag 8 8 ...
Page 100: ...EN 7 BAR FEEDER MAINTENANCE VIP80E II 7 Pag 6 6 ...
Page 104: ...EN 8 TROUBLES CAUSES CURES VIP80E II 8 Pag 4 4 ...