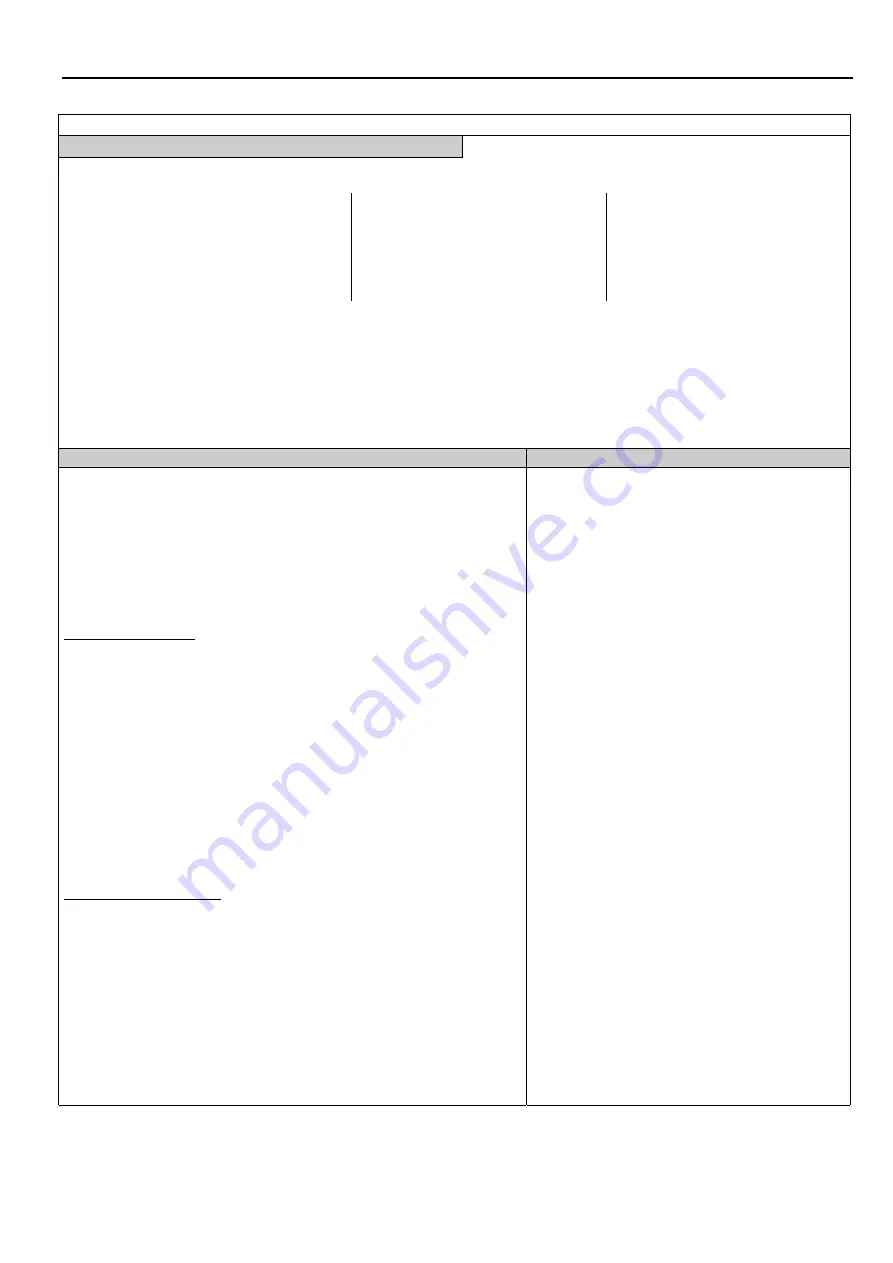
IMM 8001/8002 – Digital Motor Protection Relay
ICE / CEE
____________________________________________________________________________________________
IMU307-1 GB Ind. B
77
TESTS : Verification of the protection AGAINST MINIMUM LOAD (PUMP UNPRIMING) [37P]
CONNECTION, COEFFICIENT OF CORRECTION
Protection verification
Current injection
Coefficient
M
to be applied
Terminals
In =
1A
In =
5A
- single-phase
1.732
2-4 or 10-12
3-5 or 11-13
- balanced three-phase
1
2-4 phase 1
3-5 phase 1
10-12 phase 3
11-13 phase 3
Caution – the adjustment of coefficient K must be taken into account in the current to be injected :
K = In machine/IN
CT
Voltage injection
Voltage generator connected to terminals 19 – 21
- single-phase, voltage in phase with current :
V (hot spot voltage terminal 19), I (hot spot current terminals
4 or 5
)
or V (hot spot voltage terminal 21), I (hot spot current terminals
12 or 13
)
- three-phase like the connection diagram
With single-phase, the power measured by the relay is divided by
√
3
Sequence of operations to be performed
Results to be obtained
Simulate motor operation with the instantaneous application of an Ipos current equal to at least
1.5 In (start), then by lowering the Ipos current to a value close to In (normal
operation).
Or simulate the motor operation by ap24V to the
EL1
input (wire between terminals A3
and B18)
On starting, enabling time-delay
tP< on
is started. When it is ended, function [37P] is
put into serviced.
Check of underpower unit
Check of operating level P<
Put into service the protection, and route it to a chosen unit.
Note the value of operating level
P<
Note the value of the tripping time-delay
tP<
Note the value of the enabling time-delay
tP<on
With the current generator connected according to the desired connection, deduce
M
Pre-set the current to be injected to 1.5In by taking
M
into account.
Adjust the voltage to be injected to Un
Cut off the current, then inject it to simulate start.
Decrease the current to a value close to
In
by taking
M
into account.
Wait for the end of time-delay
tP<on
, then lower the current* down to operating level.
P<
by taking
M
into account
* the current shall not be less than 12 %In; otherwise, the relay considers that the motor
is stopped, and that the function is inhibited. For operating levels < 20 %Sn, divide the
voltage by 2 : the current operating level will be multiplied by 2.
Check of tripping time-delay tP<
Preset the power to at least 1.5 times programmed operating level
P<
Do again the same operations as above to simulate start and, at the end of
tP<on
, cut off
the voltage** to start trip time-delay tP<
** If the current is cut off, the relay considers that the motor is stopped, and that the
function is inhibited.
The Start Function indicator LED illuminates on
reaching the displayed operating level expressed
in %In x M
At the end of the time-delay :
the selected relay must be energised,
the Internal Trip indicator LED must illuminate,
the fault message and related informations must
be displayed.