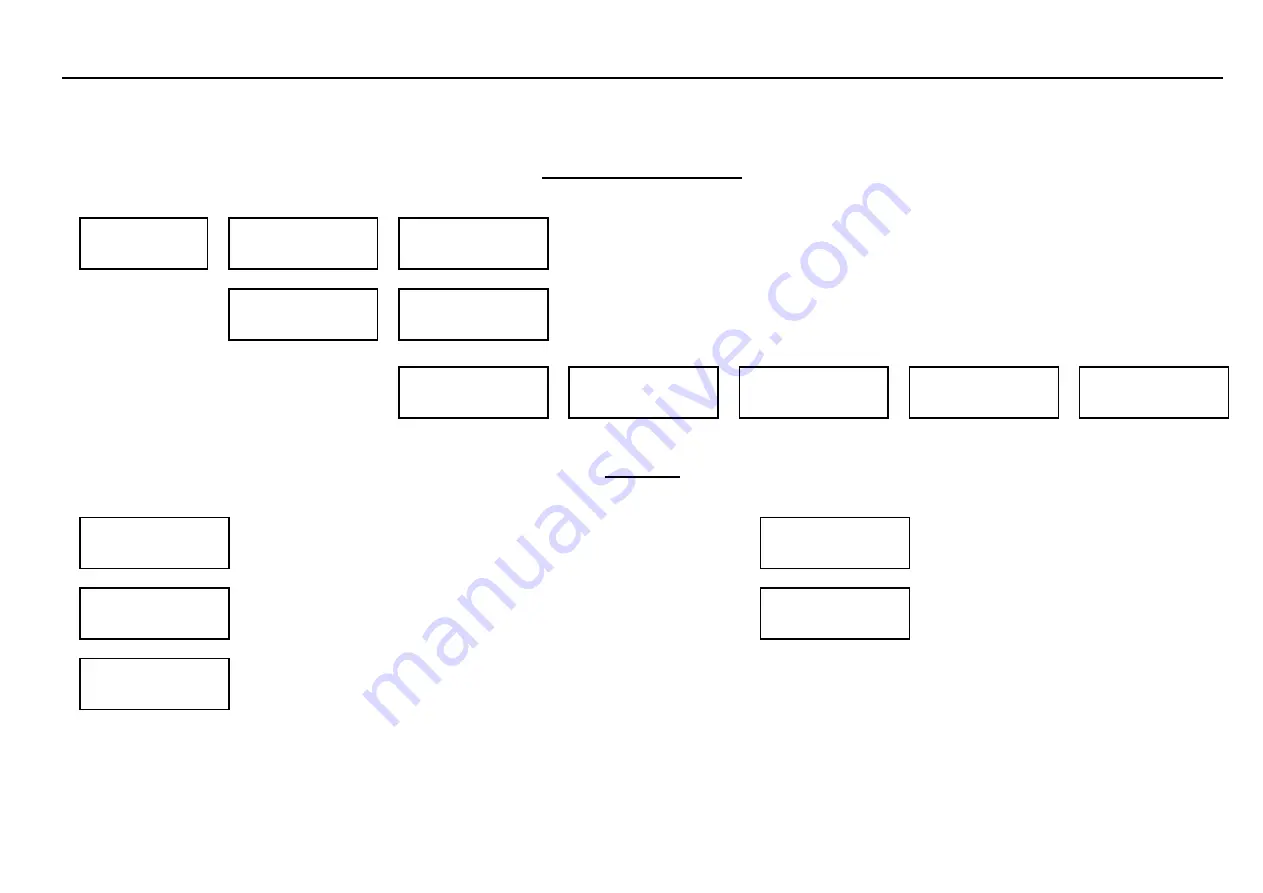
IMM 8001/8002 – Digital Motor Protection Relay
ICE / CEE
__________________________________________________________________________________________________________________________________________
IMU307-1 GB Ind. B
39
LOCAL DISPLAY OF THERMAL IMAGE PROTECTION ANSI code [49]
PARAMETER SETTING
→
←
STATISTICS
→
←
PARAMETERS
TABLE 1
→
←
PARAMETERS
TABLE 2
→
←
↑
↓
TEMPERATURE
RTDs
26
→
←
THERMAL IMAGE
49
→
←
(IMM 8002)
↑
(IMM 8001)
↓
49 – Ith>
1
OFF -- -- -- --
→
←
Heating Time Ct
1
Tau 20 min
→
←
Cooling Time Ct
1
TauC 60 min
→
←
49 – Ith> Al
1
OFF -- -- -- --
→
←
Thermal Alarm
1
Ith>A 1.00
θ
RANGES
49 – Ith>
1
OFF -- -- -- --
RANGE : ON / OFF
-- -- -- -- / T P A B
49 – Ith> Al
1
OFF -- -- -- --
RANGE : ON / OFF
-- -- -- -- / T P A B
Heating Time Ct
1
Tau 20 min
RANGE: 4 to 180 min
STEP : 1 min
Thermal Alarm
1
Ith>A 1.00
θ
RANGE : 0.80 to 1.00
θ
STEP : 0.01
Cooling Time Ct
1
TauC 60 min
RANGE : 4 to 1080 min
STEP : 1 min