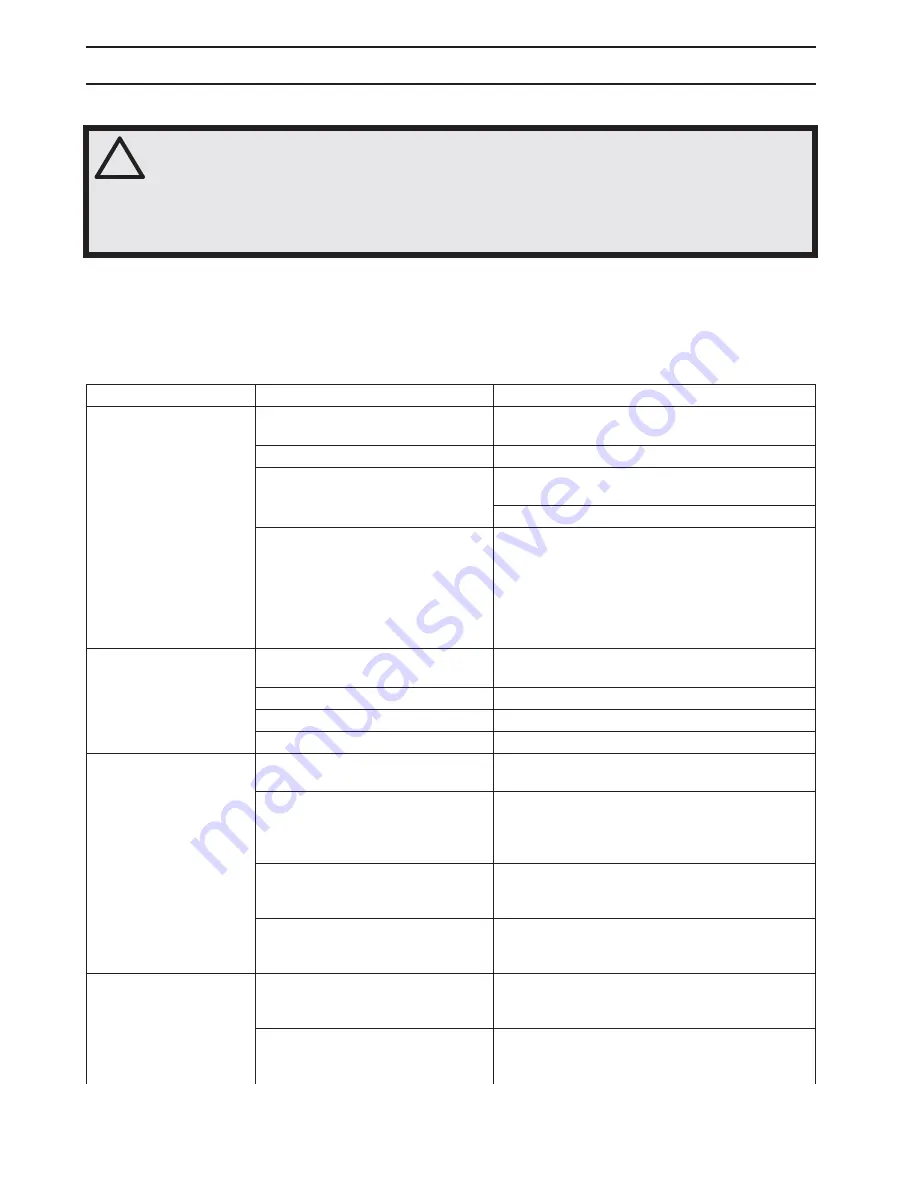
70 – English
TROUBLESHOOTING
Troubleshooting schedule
Following the trouble shooting guide will provide you with tips to facilitate the trouble shooting process. You can also
perform simpler trouble shooting operations. The operator may only carry out the maintenance and service operations
that are described in this Operator’s Manual. More extensive interventions must be carried out by an authorized service
workshop.
Always start by checking any error messages on the remote control. Follow the instructions for the respective message
in accordance with the error messages section.
!
WARNING! Most accidents involving machines occur during trouble shooting, service and
maintenance as staff have to locate themselves within the machine’s risk area. Prevent accidents
by being alert and by planning and preparing the work. You can also refer to 'Preparations for
maintenance and service” in the 'Maintenance and service” section.
If service operations or trouble shooting does not require the machine to be switched on, the
power cable must be removed and positioned so that it cannot be connected by mistake.
Problem
Cause
Possible action
The electric motor does not
start.
Emergency stop/machine stop is
pressed.
Check that the emergency stop or machine stop button
are not pressed by turning them clockwise.
Too low mains voltage to the machine.
Check power supply and ensure correct voltage.
A fuse has blown.
Check that the mains voltage is compatible with the
machine and that the correct fuses are used.
Check the power cable.
No radio communication between
remote control and machine.
Green symbol in the display indicates contact. If the
symbol is red, check that the battery for the remote
control is charged and correctly inserted. Ensure that
the correct remote control is being used. Check that
the communication cable and aerial cable on the
machine are properly secured. Test run the machine
using cable control.
Fuses for the mains
connection blow when
starting.
The machine’s fuses have too low a
rating.
Check that the mains voltage is compatible with the
machine and that the correct fuses are used.
Electric motor blown.
Contact your service agent.
Defective power cable.
Change the power cable.
The hydraulic pump has cut out.
Contact your service agent.
The motor runs but the
hydraulic functions have no
power or do not work at all.
Too little hydraulic fluid in the tank.
(Noise emanating from the pump.)
Stop the motor at once. Investigate and rectify any
leaks there might be. Replenish hydraulic fluid.
Circulation valve open.
Check the diode on the valve cap at the bottom of
valve block 1. If the circulation valve is open the diode
does not light up. Check the cable to the control
module.
Fault in the pump regulator.
Extend an unloaded cylinder to its end position and
check the pump pressure in the display. If you get
maximum pressure the pump regulator is OK.
Standby pressure set too low.
Activate the remote control without operating any
functions and check the settings for stand-by pressure
on the display. The pressure should be 20
±
1 bar.
Arm movements and tool
function run slowly.
The potentiometer that controls
mechanical movements/tools is
screwed down.
Unscrew the knob(s).
Standby pressure set too low.
Activate the remote control without operating any
functions and check the settings for stand-by pressure
on the display. The pressure should be 20
±
1 bar.
Summary of Contents for DXR-310
Page 75: ...English 75 TECHNICAL DATA Range and transport diagram DXR250 4483 176 5 2020 79 5 4815 189 5 ...
Page 77: ...English 77 TECHNICAL DATA DXR270 4483 176 1986 78 4849 191 1435 56 ...
Page 79: ...English 79 TECHNICAL DATA DXR300 4868 192 2368 93 5231 206 1818 72 ...
Page 81: ...English 81 TECHNICAL DATA DXR310 5182 204 2129 84 2678 105 5549 218 ...
Page 84: ...1158619 27 z Z 78 z Z 78 2016 12 19 US Original instructions ...