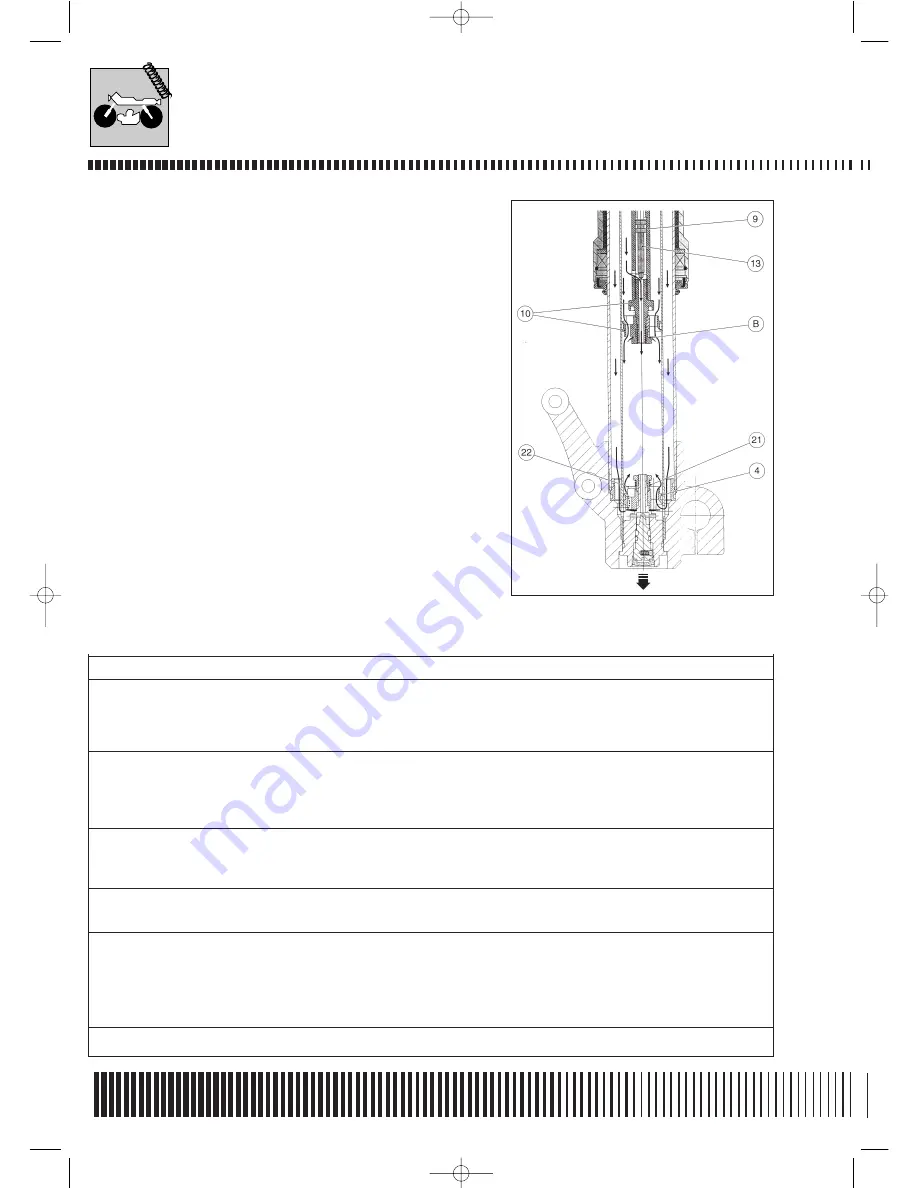
TELAIO, SOSPENSIONI E RUOTE
FRAME, SUSPENSIONS AND WHEELS
CHASSIS, SUSPENSIONS ET ROUES
RAHMEN, AUFHAENGUNG UND RAEDER
BASTIDOR, SUSPENSIONES Y RUEDAS
I.24
N° 8000A3632
(06-04)
Let’s see what happens in each leg during REBOUND.
Spring rebound action pushes the stanchion downwards, thus causing an oil need
into the cartridge (see FIG. 4).
The compression of the oil volume into the chamber over the pumping element
(10) pushes the washers (B) at the pumping element piston bottom to open. To
change the fork damping now, the washer setting (B) can be changed, as
describe for the piston (4).
Apart from flowing through the above passage, the oil is pushed into the rod (9)
and can flow out of the chamber at the pumping element bottom through the area
outlined by the position of the conical pin (13). The size of this area can be
changed by turning the rebound screw adjuster (11). The chamber at the
pumping element bottom is also filled with the oil flowing through the piston slots
(4). The oil flow wins over the action of the return spring (21) and lifts the washer
(22), thus allowing the oil to flow from the outer chamber into the body inner
chamber. (6).
GENERAL RULES FOR A PROPER OVERHAULING
1. After a total disassembly, always use new seals during the reassembly stage.
2. Always follow the sequence 1-2-1 when tightening two screws or nuts close
one to each other, i.e. always tighten the first screw (1) after tightening the second
screw (2).
3. Use non-inflammable and possibly biodegradable solvent when cleaning.
4. Always lubricate all parts in relative contact with fork oil before reassembling.
5. Always grease the oil seal lips before reassembling.
6. Use only metric wrenches and not inch wrenches. Inch wrenches could have
sizes, which are similar to millimeter wrenches but could damage the screws, thus
being impossible to loosen them.
TROUBLESHOOTING GUIDE
This section deals with some troubles, which can occur when using this fork. Possible causes are mentioned as well as recommendations
on how to possibly solve the problem. Always read the following table before performing any fork fixing.
TROUBLE
CAUSE
REMEDIES
Oil leakage from the oil seal
1. Oil seal wear
1. Change oil seal
2. Scored stanchion tube
2. Change the tube and the
oil seal
3. Dirty seal
3. Clean or replace
Foot oil leakage
1. Foot valve OR damaged
1. Change the seal
2. Loose foot valve
2. Tighten the screw
3. OR of the compression screw
3. Change the seal
adjuster damaged
The fork is too soft under
1. Low oil level
1. Top up
any adjustment conditions
2. Broken spring
2. Change the spring
3. Too low oil viscosity
3. Use a different oil viscosity
The fork is too hard
1. Too high oil level
1. Restore the oil level
under any adjustment conditions
2. Too high oil viscosity
2. Use a different oil viscosity
The fork has no reactions when
1. Inner rod pin blocked
1. Clean or change the rod
adjustment changes are made
2. Blocked compression
2. Disassemble and clean
screw adjuster
2. Oil with foreign bodies
2. Clean and change oil
3. Foreign bodies
3. Disassemble and clean
occluding damper valves
Decreased leg stiffness
Sliding bushing wear
Change sliding bushing
FIG.4
Man. 630-2004-IMP. I-2 27-07-2004 11:49 Pagina I.24
Summary of Contents for 2004 SMR 630
Page 6: ...N 8000A3632 06 04 4 Man 630 COP 2004 15 07 2004 15 44 Pagina 4 ...
Page 8: ...6 N 8000A3632 06 04 Man 630 COP 2004 15 07 2004 15 44 Pagina 6 ...
Page 9: ...N 8000A3632 06 04 7 Man 630 COP 2004 15 07 2004 15 44 Pagina 7 ...
Page 10: ...8 N 8000A3632 06 04 Man 630 COP 2004 15 07 2004 15 44 Pagina 8 ...
Page 11: ...N 8000A3632 06 04 9 Man 630 COP 2004 15 07 2004 15 44 Pagina 9 ...
Page 12: ...10 N 8000A3632 06 04 Man 630 COP 2004 15 07 2004 15 44 Pagina 10 ...
Page 13: ...N 8000A3632 06 04 11 Man 630 COP 2004 15 07 2004 15 44 Pagina 11 ...