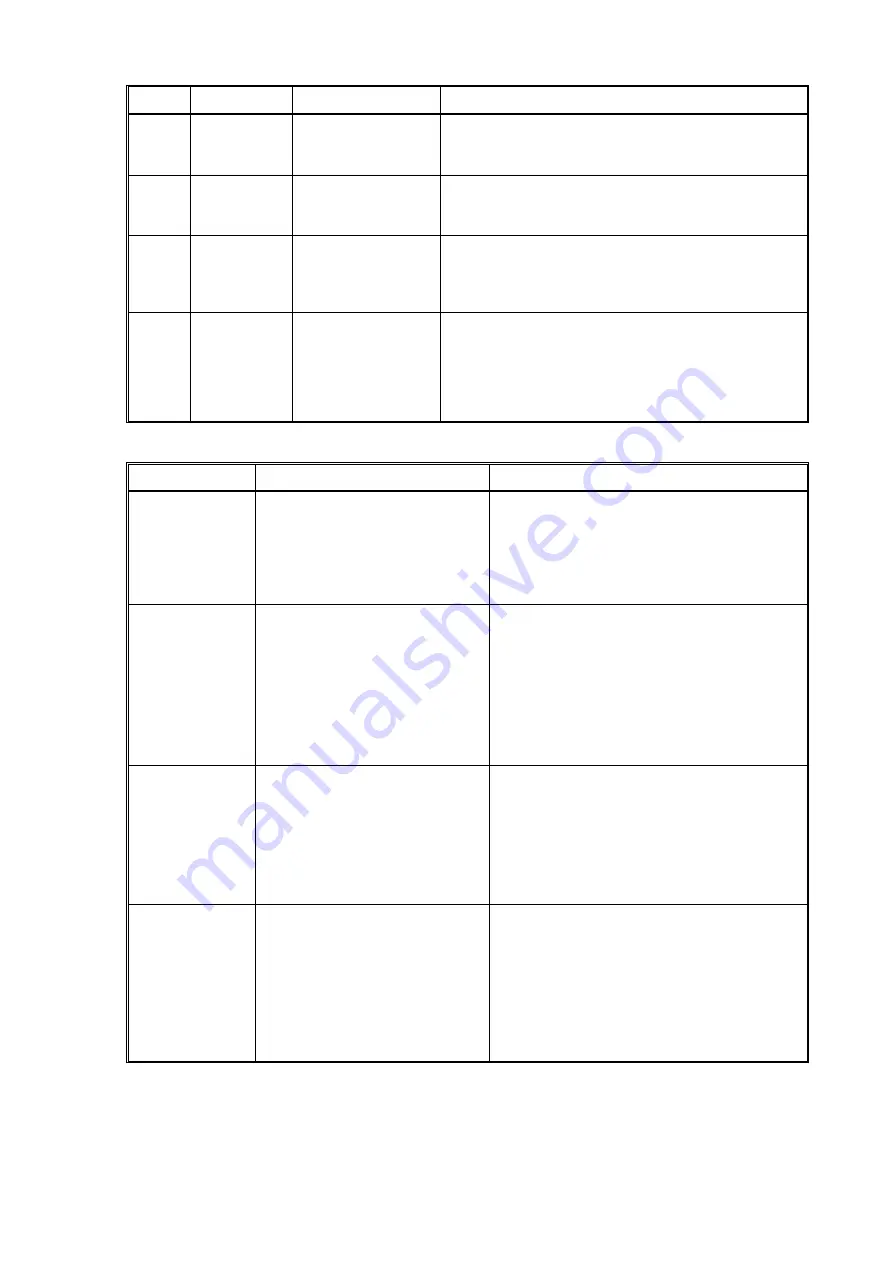
34
Code
Name
Detail
Measurement
110
Coolant
capacity not
enough
Coolant in cool tank not
enough
1
、
Check the coolant capacity, add until the cool tank is full
2
、
Check the flow sensor damage or not
3
、
Check the control cable of the flow sensor damage or not
116
Panel and PCB
communication
error
The communication not
success
1
、
Check the inside of the machine, the panel and PCB
connection well or not
2
、
The communication circuit part of the PL18 or PL19 damage
139
Blow clean
overtime
The gas pressure error
always be there more
than 3min during the
gas blow
Solve same as the error code“044”
、
“053”
156
deputy
machine have
current when
power on
(SLG-200HF no
this function)
there is current output
signal on the sensor of
of the deputy machine
when power on
1
、
Current sensor or PCB PL18 damage
2)
Trouble shooting without error code
Phenomenon
Reason
Measurement
Turn on the plasma
power source,the
all indicator of
power source not
light,no reaction
1
、
Default phase
2
、
Power supply switch damaged.
3. Plasma power source control
transformer power supply not working.
1
、
Check three phase power supply.
2
、
replace power source switch
3
、
replace fuse of rear power source or control
transformer
CNC give start
signal to plasma
power source,but
machine no action.
1
、
gas signal of external power source
problem.
2
、
PCB PL18 of power source is
damaged.
1
、
Check the start indicator on the power source,if
have start signal,the light on, when disconnect the
signal,the light off. Otherwise the outside start signal
circuit damage or PL18 damage.
2
、
When there is start signal, LED17 on the PL18 should
on, when start signal off, then this LED17 should off. If
the signal from CNC to power source OK, but this LED
17 not on, then PL18 is damage.
Not fully
piercing,there are
sparks on the
workpiece surface.
1
、
cutting current setting too low
2
、
cutting speed too fast
3
、
torch part damaged
4
、
metal too thickness
1
、
Check and set current according to cutting table .
2
、
Checking and set cutting speed according to cutting
table .
3
、
Replace the consumables accordingly
4. Select the cutting procedure according to the
cutting table parameter
Bad cutting quality
1
、
Big difference between the actually
gas pressure and theory gas pressure.
2
、
Metal too thickness
3
、
Nozzle and electrode damaged.
4
、
arc and workpiece out of vertical.
5
、
Cutting speed too slow or too fast.
1
、
Check and adjust the air pressure accordingly
2
、
Check the quality cutting thickness according to
table parameter.
3
、
Replace electrode and nozzle.
4
、
Adjust the torch corner.
5
、
Adjust the cutting speed according to cutting
process table.
Summary of Contents for SLG-200HF
Page 12: ...5 3 2 SLG 300HF dimension and weight 3 3 SLG 400HF dimension and weight...
Page 22: ...15 5 2 Installation Drawing System components A Plasma power sourceSLG 200HF 300HF 400HF...
Page 47: ...40 3 Circuit diagram 7 1 SLG 200HF...
Page 48: ...41 7 2 SLG 300HF...
Page 49: ...42 7 3 SLG 400HF...
Page 50: ...43 7 4 QFK E1...