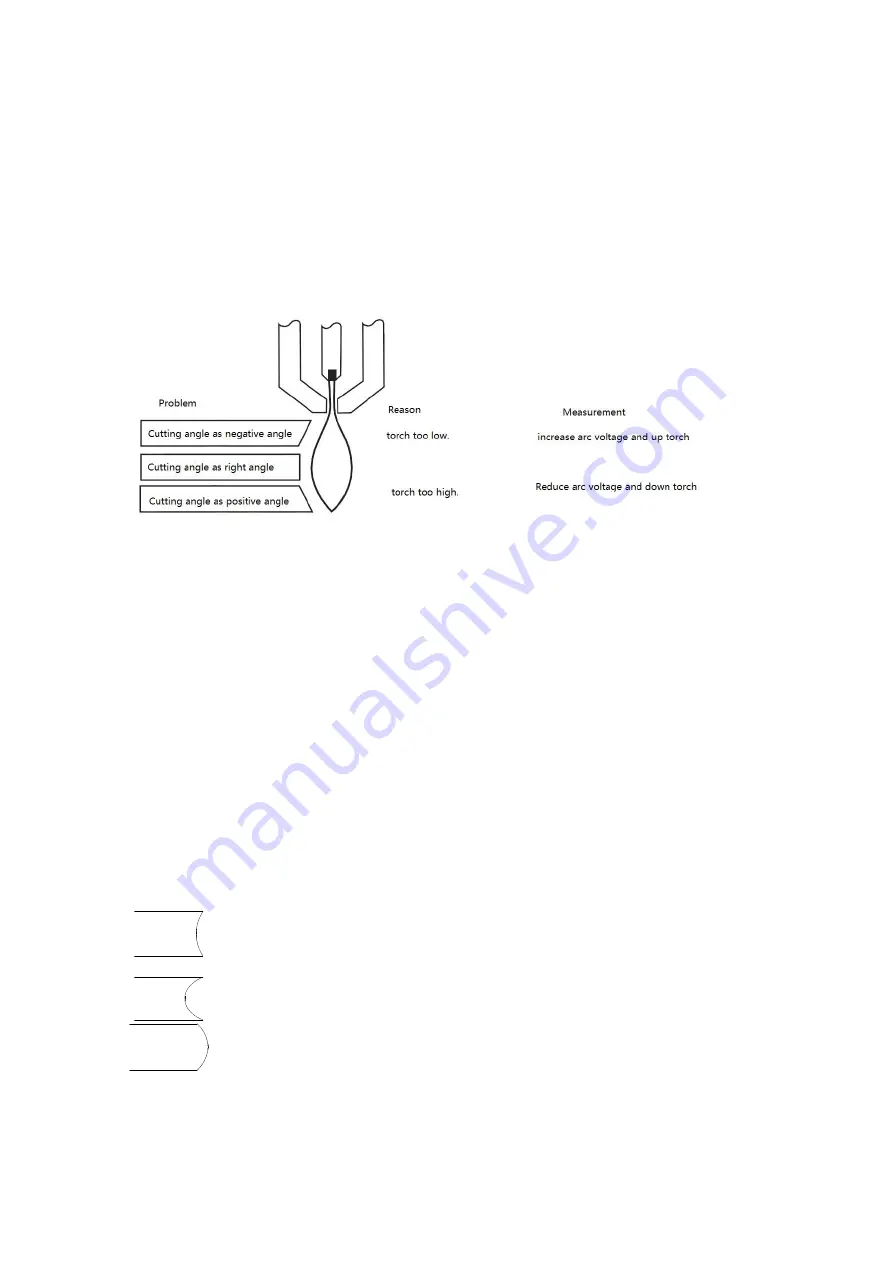
24
If the four side cutting tilt corner less the 4 degree, that is normal
Note: when torch move forward, the cutting corner is at the right side
Note: if need to confirm the cutting corner cause by the cutting machine or CNC system, can try cut and test each side
corner. Then 90degree rotate the torch support, try cut again, if the cutting corner the same for the two cut, then
the problem caused by the CNC system
If the cutting corner problem not solve after the mechanical problem solve, check the distance from torch to workpiece,
especially when the cutting corner both is negative or positive
Note
:⑴
When the cutting seam upper side delete material more than bottom side, the corner is positive
⑵
When the cutting seam upper side delete material less than bottom side, the corner is negative
⑵
slag
When the cutting speed too slow, the slag will arise, which will collect at the bottom of the cutting seam, easy to
remove. Increase the cutting speed can reduce this slag
when cutting speed too fast, slag will arise, which collect on the cutting seam, not easy to remove. Slow the cutting
speed can reduce this slag:
a)
Reduce the cutting speed
b)
Decrease the arc voltage, shorten the distance between torch to workpiece
c)
Increase the O
2
in shield gas(the manual gas console not work with the mix shield gas, but can increase the O
2
,
then connect the gas to the manual gas console input)
Note: compare to cold metal, the hot metal is easy to cause slag. For example, the first cutting, slag is few, but after
first cut, the slag will be more and more, higher the temperature, more slag
Compare with stainless steel or aluminium, low carbon steel is more easy to cause slag
Consumables damage may cause continuous slag
5
、
Cutting surface straightness
Cutting surface dimple or convex require the torch height correct to get cutting surface flat
If the distance from torch to workpiece too short, there will be dimple at the surface, enlarge the arc voltage
need enlarge the distance from torch to workpiece to get better surface.
When the distance from workpiece to torch too far or cutting current too big, there will be convex at the
surface. Then need to lower the arc voltage and cutting current. If can;t change the cutting current, then
need to use smaller consumables
6
、
Other improvement
⑴
piercing
The piercing delay time need be enough so that can penetrate the material, but if delay too long the arc can;t find the
Summary of Contents for SLG-200HF
Page 12: ...5 3 2 SLG 300HF dimension and weight 3 3 SLG 400HF dimension and weight...
Page 22: ...15 5 2 Installation Drawing System components A Plasma power sourceSLG 200HF 300HF 400HF...
Page 47: ...40 3 Circuit diagram 7 1 SLG 200HF...
Page 48: ...41 7 2 SLG 300HF...
Page 49: ...42 7 3 SLG 400HF...
Page 50: ...43 7 4 QFK E1...