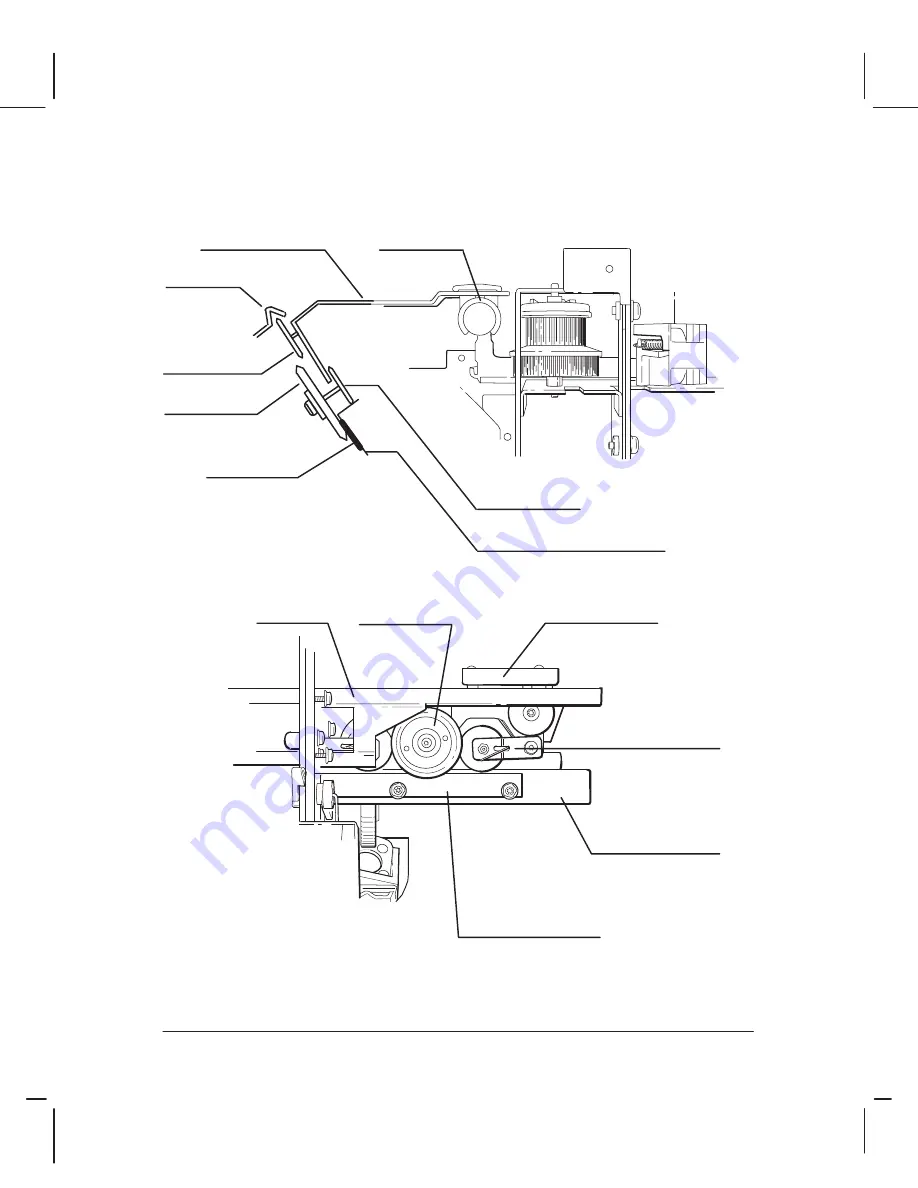
6-33
Removal and Replacement
Figure 6-23.
Cutter Assembly
Starguard
Right Pre-load Arm
Cutter Blade
Linear Cutter Blade
Overdrive Support
Assembly
Bottom Finger of
Cutter Assembly
Slider Rod
Bushing
Cutter Blade
Linear Blade
Starguard
Upper Wheels
Lower Wheels
Overdrive Support Assembly
Side View
Front View
(C)C2858-55
(C)C2858-66
Summary of Contents for C2858A
Page 125: ...7 10 Adjustments Calibrations Notes ...
Page 155: ...9 4 Product History Notes ...
Page 164: ...10 9 Parts and Diagrams Illustrated Parts Breakdown C2859A Electronics Enclosure C C2858 3 1 ...
Page 166: ...10 11 Parts and Diagrams Illustrated Parts Breakdown C2858A Electronics Enclosure C C2858 4 1 ...
Page 182: ...10 27 Parts and Diagrams Illustrated Parts Breakdown Paper Drive Assemblies C C2858 12 1 ...
Page 198: ... ...