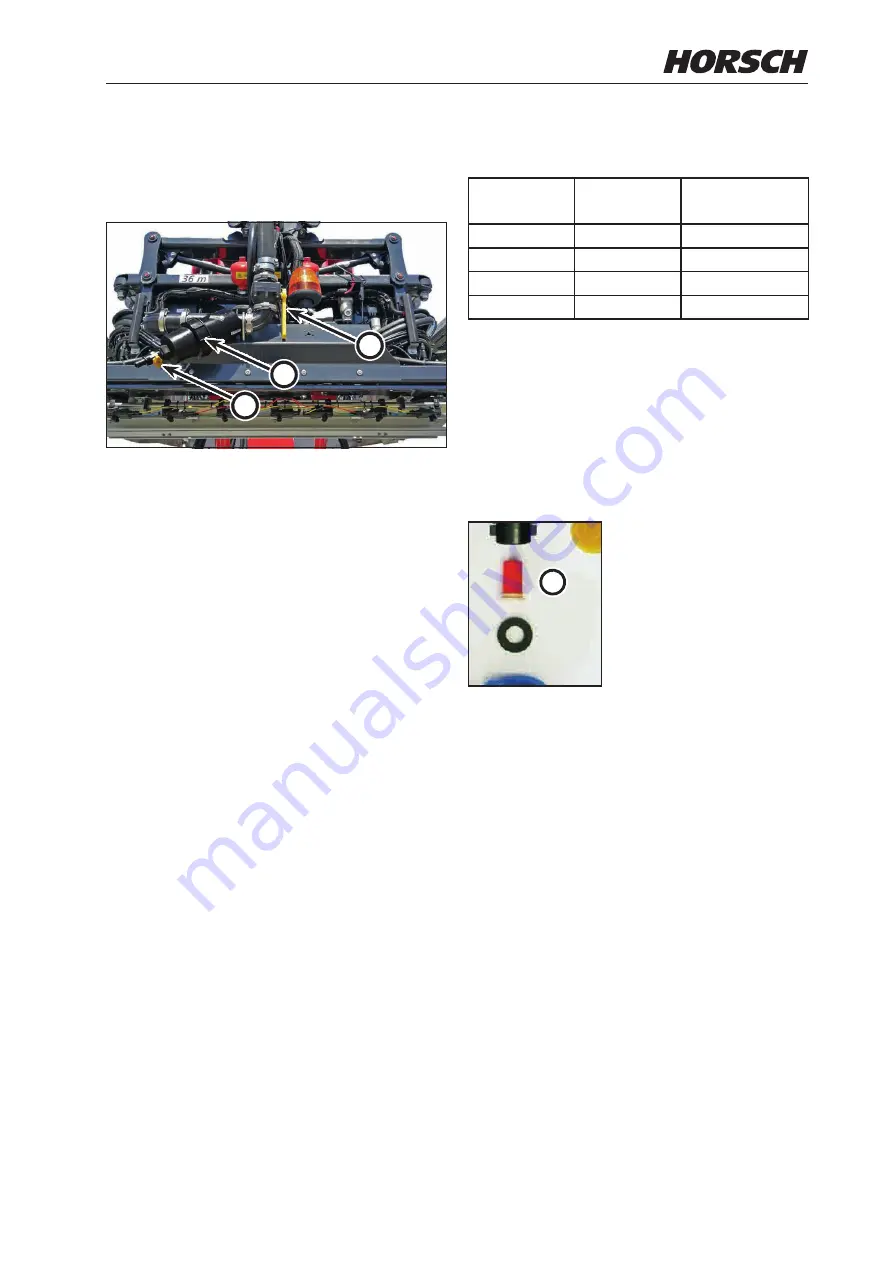
The pressure filter is equipped with 80 meshes/
inch² insert as standard. Depending on the use,
additional filter inserts with 50 or 100 meshes/
inch² insert are available.
1
3
2
1
Auxiliary pressure filter
2
Shut-off lever
3 Valve
Clean the auxiliary pressure filter as needed.
Lower the parallelogram for this purpose. Turn
the yellow lever to the right (2) by 90° to thus
block the flow to the pressure filter. Open the
small yellow valve at the lift (3) and collect any
draining agent. Dispose of the agent if necessary
or return it to the spraying mixture container.
Open the filter housing with the pressure filter
wrench. Clean the auxiliary pressure filter.
Repeat all steps in the opposite order after
cleaning.
Dome screen
The dome screen prevents contaminants from
entering into the spraying mixture container
during filling through the dome. The screen has
a standard mesh size of 1 mm.
Drain filter in the tank
The drain filter in the tank prevents settled
agents from being deposited in the suction fitting.
Suction filter
The suction filter filters the water / chemical
before it enters into the centrifugal pump (mesh
size 0.9 mm).
Overview of pressure filter elements
Meshes/
square inch
Nozzle
size
Mesh size
[mm]
32
50
from ‘03’
0.35
80
‘02’
0.20
100
up to ‘015’
0.15
Filter cleaning, see chapter Cleaning,
maintenance and repair.
Nozzle filter (optional)
The nozzle filter (a) prevents clogging of the
spraying nozzles.
a
Overview of nozzle filters
24
meshes/square inch
from nozzle size:
06’ and bigger
Filter area:
5.00 mm²
Mesh size:
0.50 mm
50 meshes/square inch
for nozzle size:
'02' to '05'
Filter area:
5.07 mm²
Mesh size:
0.35 mm
100 meshes/square inch
for nozzle size:
015’ and smaller
Filter area:
5.07 mm²
Mesh size:
0.15 mm
62
63
Summary of Contents for LEEB 12 TD
Page 2: ......
Page 5: ......
Page 9: ...5...
Page 27: ...Safety stickers with the addition 2x can be found on either side of the machine 2x 23...
Page 121: ...Diagram a with example 117...
Page 146: ...Suspension cylinder Suspension cylinder 142...
Page 148: ...Parallelogram lock Pendulum lock cylinder Parallelogram Parallelogram 144...
Page 180: ......