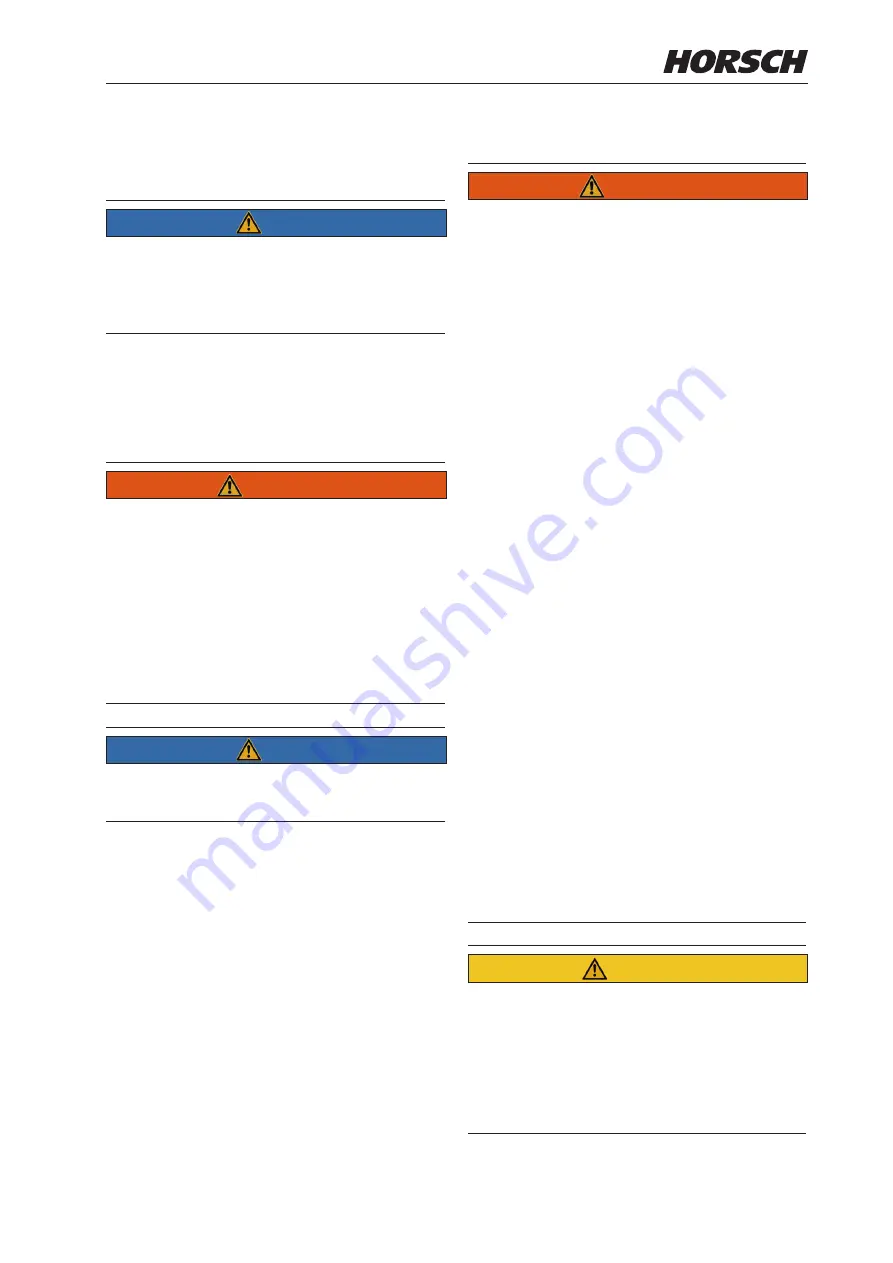
Maintenance of brake
system
NOTE
In order to achieve optimal braking characteristic
and minimal wear of brake linings we recommend
the performance of a drawing adaptation
between tractor and crop protection sprayer.
¾
Have the drawing adaptation carried out in
a specialist workshop after a reasonable
running-in time of the service brake system.
WARNING
¾
Repair and adjustment work on the service
brake system must only be performed by
specially trained specialists.
¾
Use extreme caution when performing
welding, torch cutting and drilling work near
brake lines.
¾
After completing setting and maintenance
work on the brake system you should
generally perform a brake test.
NOTE
Continuously check the brakes for wear and
function!
General visual inspection
WARNING
A general visual inspection of the brake
system must be performed!
The following criteria must be checked
and observed at this:
¾
Pipe, hose lines and coupling heads must
not show any external damage or corrosion.
¾
Joints, e.g. on fork heads must be properly
secured, light moving and should not be worn.
Ropes and actuating cables
¾
must be properly guided.
¾
must not show any noticeable damage.
¾
must not be knotted.
¾
Check the piston stroke on brake cylinders,
adjust if necessary.
The
air vessel must
¾
not be damaged.
¾
not show any external corrosion damage.
Check the brake drum for contamination
(workshop work)
¾
Dismantle the brake drum.
¾
Remove any dirt and crop residues that may
have entered.
¾
Check the condition of the brake drum and
lining thickness.
¾
The drum must be measured when the wear
edge is approached. Once the max. degree
of utilisation has been reached, it must be
replaced immediately.
¾
Reassemble the brake drum.
CAUTION
Risk of accident from dirt that has entered the
brake linings! It may settle there and significantly
affect the braking power.
If there is dirt inside the brake drum, the
brake linings should be inspected in an expert
workshop. Wheel and brake drum must be
disassembled for this purpose.
148
149
Summary of Contents for LEEB 12 TD
Page 2: ......
Page 5: ......
Page 9: ...5...
Page 27: ...Safety stickers with the addition 2x can be found on either side of the machine 2x 23...
Page 121: ...Diagram a with example 117...
Page 146: ...Suspension cylinder Suspension cylinder 142...
Page 148: ...Parallelogram lock Pendulum lock cylinder Parallelogram Parallelogram 144...
Page 180: ......