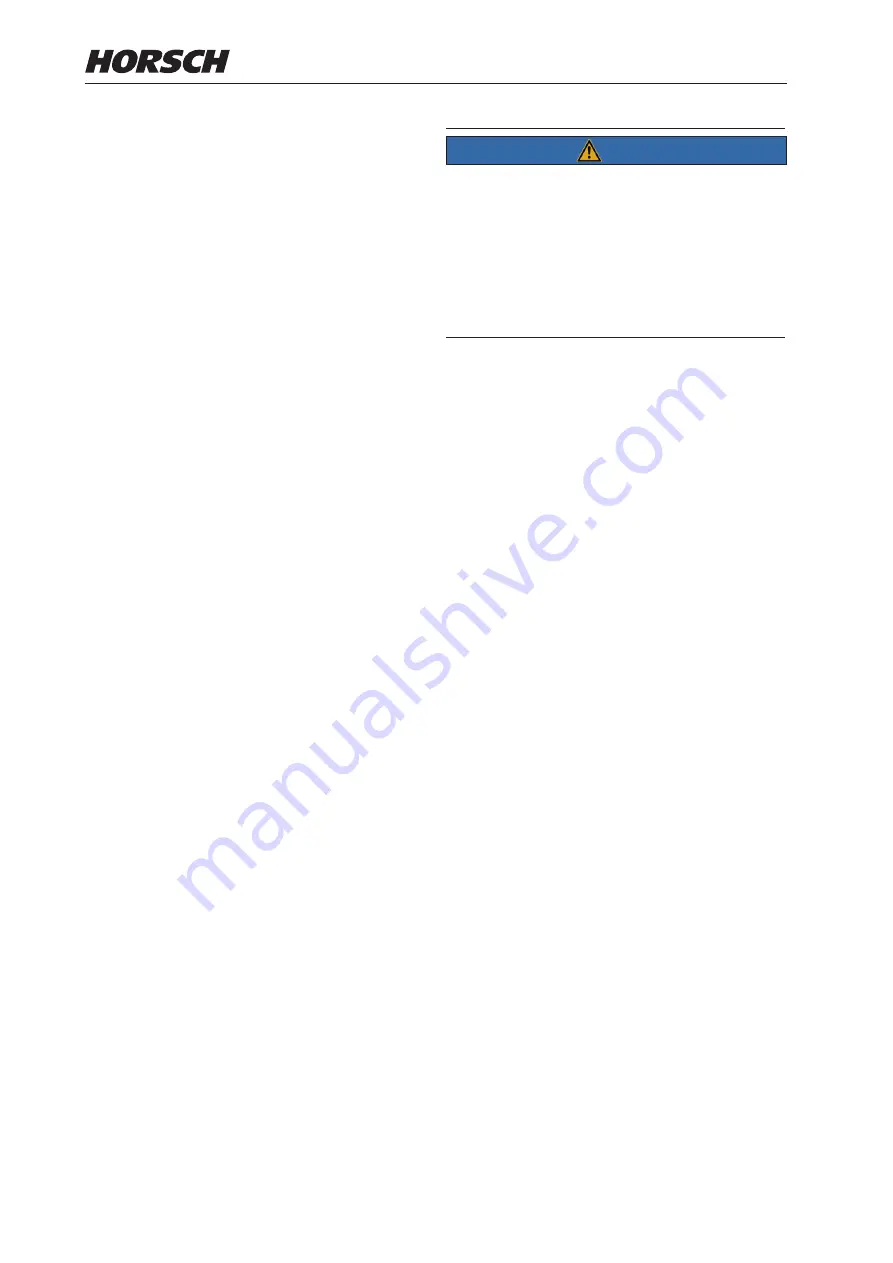
Maintenance intervals
The maintenance intervals are determined by
many different factors.
For example, the different operating conditions,
weather impact, travel and working speeds, dust
accumulation and type of soil, crop protection
agents and carbonyl diamide agents used, etc.
affect the maintenance intervals. The quality of
the lubricants and cleaning agents also affects
the time to the next care activities.
The specified maintenance intervals therefore
only serve as a reference.
In case of deviations from normal operating
conditions the intervals must be adapted ac-
cordingly.
Regular maintenance is the basis for a fully
operable machine. Properly serviced machines
reduce the risk of failing and ensure economical
use and operation of the machines.
¾
Initiate protective measures (e.g. cover or
even disassemble lines at particularly critical
points)
•
when welding, drilling or grinding
•
when working with abrasive cutting wheels
in the vicinity of plastic hoses and electric
lines.
¾
Thoroughly clean the crop protection sprayer
before each repair or maintenance, espe-
cially the parts contaminated by the spraying
mixture.
¾
Carry out repairs only on machines shut down
and secured against restarting.
¾
Switch off the main battery switch with all care
and maintenance work.
This applies in particular to welding work on
the machine. The ground connection must
be as close as possible to the welding point.
¾
Screw connections loosened for the purpose
of care and maintenance work must be retight-
en after work is completed.
Appropriate expert knowledge is the pre-
requisite for the performance of tests and
maintenance work. This expert knowledge
cannot be obtained from these operating
instructions!
The following is generally prohibited:
¾
drilling on the undercarriage
¾
enlarging existing boreholes in the vehicle
frame
¾
welding on load-bearing parts
Conversions affect specifications in the op
-
erating instructions.
NOTE
Before each commissioning
¾
Check hoses, pipes and connecting pieces
for apparent faults or leaking connections.
¾
Remedy chafed sections on hoses and pipes.
¾
Immediately replace worn or damaged hoses
and pipes.
¾
Seal leaking connections immediately.
132
133
Summary of Contents for LEEB 12 TD
Page 2: ......
Page 5: ......
Page 9: ...5...
Page 27: ...Safety stickers with the addition 2x can be found on either side of the machine 2x 23...
Page 121: ...Diagram a with example 117...
Page 146: ...Suspension cylinder Suspension cylinder 142...
Page 148: ...Parallelogram lock Pendulum lock cylinder Parallelogram Parallelogram 144...
Page 180: ......