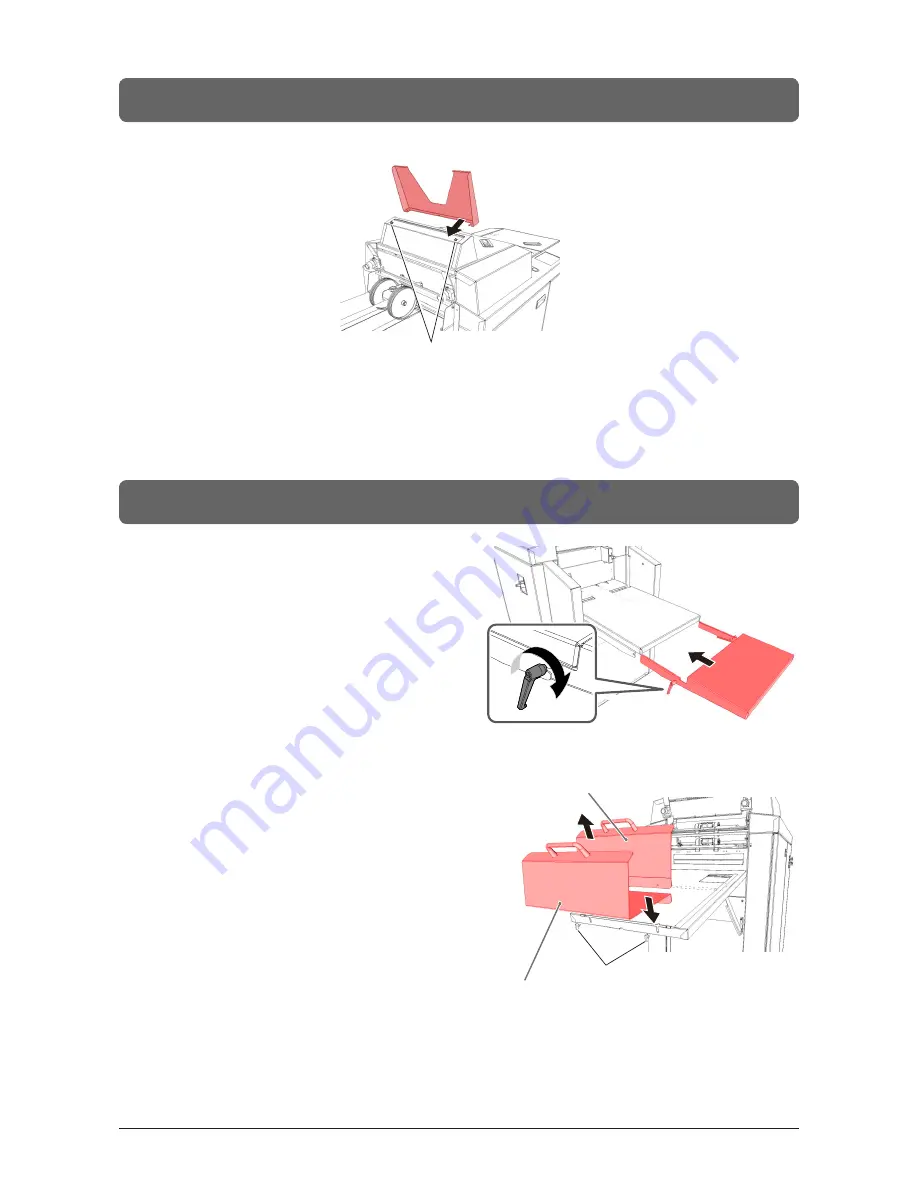
113
CRF-362
6-4
Attaching the Accessory
Sheet Guide for Fold Section
Loosen two locking screws (TT4-8TP×2)
for the fold section cover. Attach the guide,
and lock the cover and the guide together.
6-5
When the Sheet Length Is 650 mm/25.59" or Longer
1
Attach the support table.
2
Remove the standard stopper.
Then attach the stopper for long
sheet.
Lock
Wing Bolt×2
Standard Stopper
Stopper for Long Sheet
Summary of Contents for CRF-362
Page 10: ...This page is intentionally left blank ...
Page 49: ...This chapter explains the procedure for us ing convenient functions 2 2 Advanced Operation ...
Page 64: ...This page is intentionally left blank ...
Page 65: ...3 3 Adjustments This chapter explains how to make some adjustments that may be necessary ...
Page 80: ...This page is intentionally left blank ...
Page 98: ...This page is intentionally left blank ...
Page 99: ...5 This chapter explains how to replace the consumables and clean the machine 5 Maintenance ...
Page 114: ...This page is intentionally left blank ...
Page 115: ...6 7 This chapter lists the specifications for this machine 7 Appendix ...
Page 121: ...This page is intentionally left blank ...
Page 122: ...Manufacturer Phone 81 75 934 6700 Fax 81 75 934 6708 www horizon co jp ...