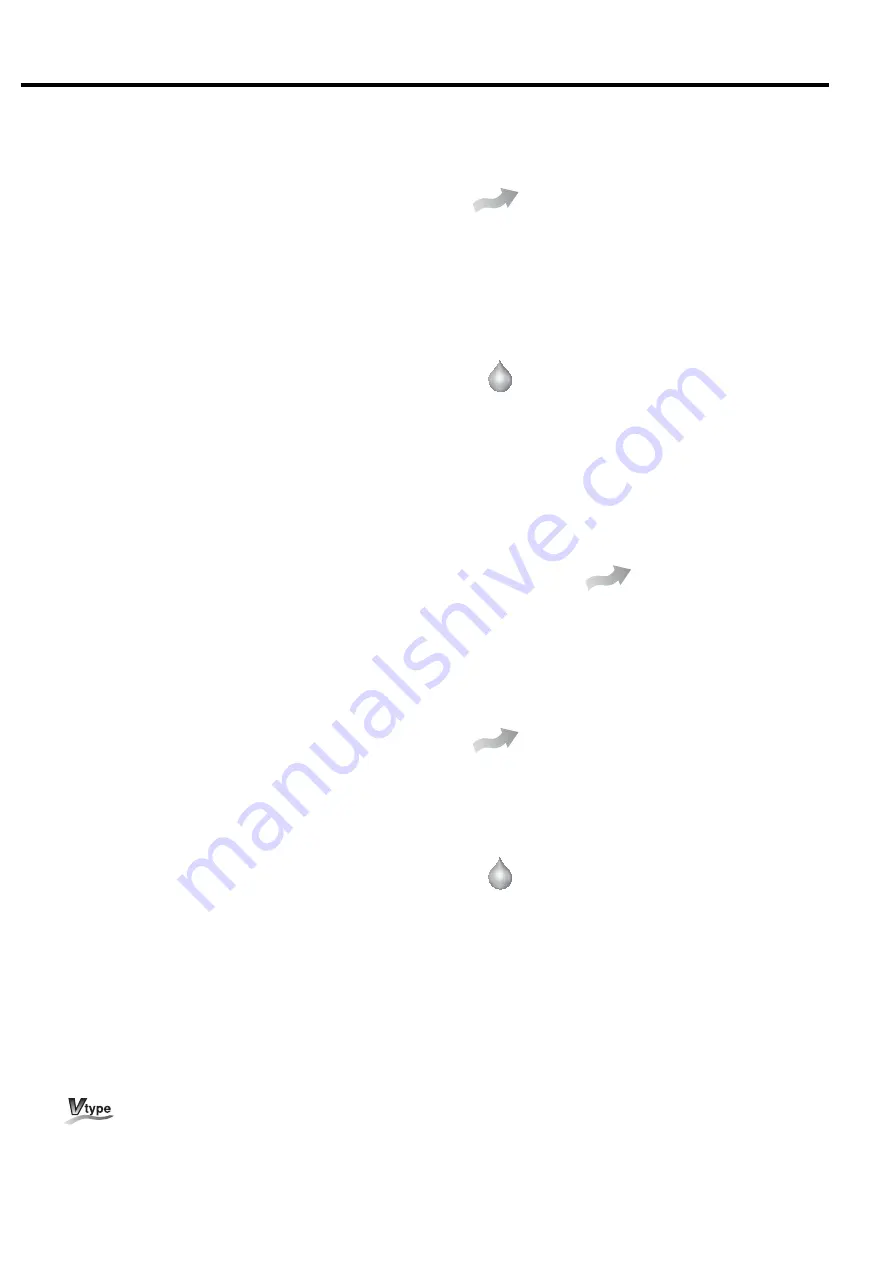
60
8. STANDARD COMPONENTS AND SUBSYSTEMS
⑴
Airend
A rotor assembly rotates while the timing gear keeps
a precise clearance between the male and female
rotors. This non-contacting, high speed rotation of
the rotor assemblies compresses the intake air.
There is no oil injected into the rotor assemblies
during the compression process, allowing the air
compressor to discharge oil free compressed air.
⑴
Roto rs
: The surfaces of the rotors are finished
with a special heat-resistant PTFE-free
coating designed to precisely limit the
clearances between the male and female
rotors and prevent rust.
⑵
Beari ng
: The heavier male rotors are supported
by bearings that are larger in diameter,
thus increasing service life.
⑶
Case
:
The jackets for oil (air-cooled model) or
for cooling water (water-cooled model) are
provided on the case to absorb the heat of
compression.
⑷
Timin g gears
: A pair of precision finished timing
gears is mounted on the ends of the rotor
shafts to keep a precise clearance between the
rotors and prevent contact during rotation.
⑸
Shaft
seal
: The sealing mechanism consists of
both 1.) Air seals and 2.) Visco-type seals.
Air seals prevent the compressed air from
leaking out of the compression chamber.
Visco-type seals prevent the oil in the gear
case from entering the compression chamber.
⑵
Compressor Drive Train
The air compressor employs a high efficient, 2-pole
for fixed speed type or 6-pole for Vtype, totally
enclosed, fan cooled (TEFC) motor. The rotation
speed of both the 1st and 2nd stage airends are
increased to a properly rated level by a set of step-up
gears in the gear case.
⑶
Capacity Control System
[Fixed-speed type]
When the demand of compressed air decreases, the
system closes the suction throttle valve and
exhausts the internal compressed air to atmosphere
at the same time, thus unloading the air compressor.
When demand of the compressed air decreases, the
system reduces the motor speed. And When
demand of the compressed air decreases more,
purges the compressed air to atmosphere.
⑷
Intercooler
Air-Cooled
The air-cooled intercooler is made of aluminum. The
intake air is compressed up to 29 psi (0.20 MPa) (and
consequently heated) by the 1st stage airend. The
intercooler cools the heated air to an atmospheric
tempe approx. 27°F (15
℃
) and separates the
water vapor from the discharge air before the air
enters the 2nd stage airend in the process.
Water-Cooled
The water-cooled intercooler is shell and tube type.
The intake air is compressed up to 29 psi (0.20
MPa) (and consequently heated) by the 1st stage
airend. The intercooler cools the heated air to
cooling water tempe approx. 27
〜
36°F (15
〜
20
℃
) and separates the water vapor from the
discharge air before the air enters the 2nd stage
airend in the process.
⑸
Hi-Precooler
Air-Cooled
The air-cooled Hi-precooler is located between the
2nd stage airend and the intercooler, and has the
following functions:
-Primarily cool the hot compressed air discharged
by the airend.
⑹
Aftercooler
Air-Cooled
The air-cooled aftercooler is made of aluminum. It is
located downstream of the check valve and reduces
the discharge air temperature down to an atmospheric
tempe27
°
F
(15
℃
) or lower and separates the
water vapor from the discharge air in the process.
Water-Cooled
The water-cooled intercooler is shell and tube type. It
is located downstream of the check valve and reduces
the discharge air temperature down to cooling water
tempe 23
°
F
(13
℃
)
and separates the water
vapor from the discharge air in the process.
⑹
Check valve
The check valve is located downstream of the 2nd stage
airend and prevents backflow of the discharge air.
⑺
Lubricating system
The lubricating subsystem consists of the oil pump,
oil strainer, oil filter, oil cooler and oil relief valve.
The oil pump circulates the oil in the gear case oil
sump through the lubrication subsystem, keeping
the bearings, gears, etc. lubricated.
8.1 Standard Components