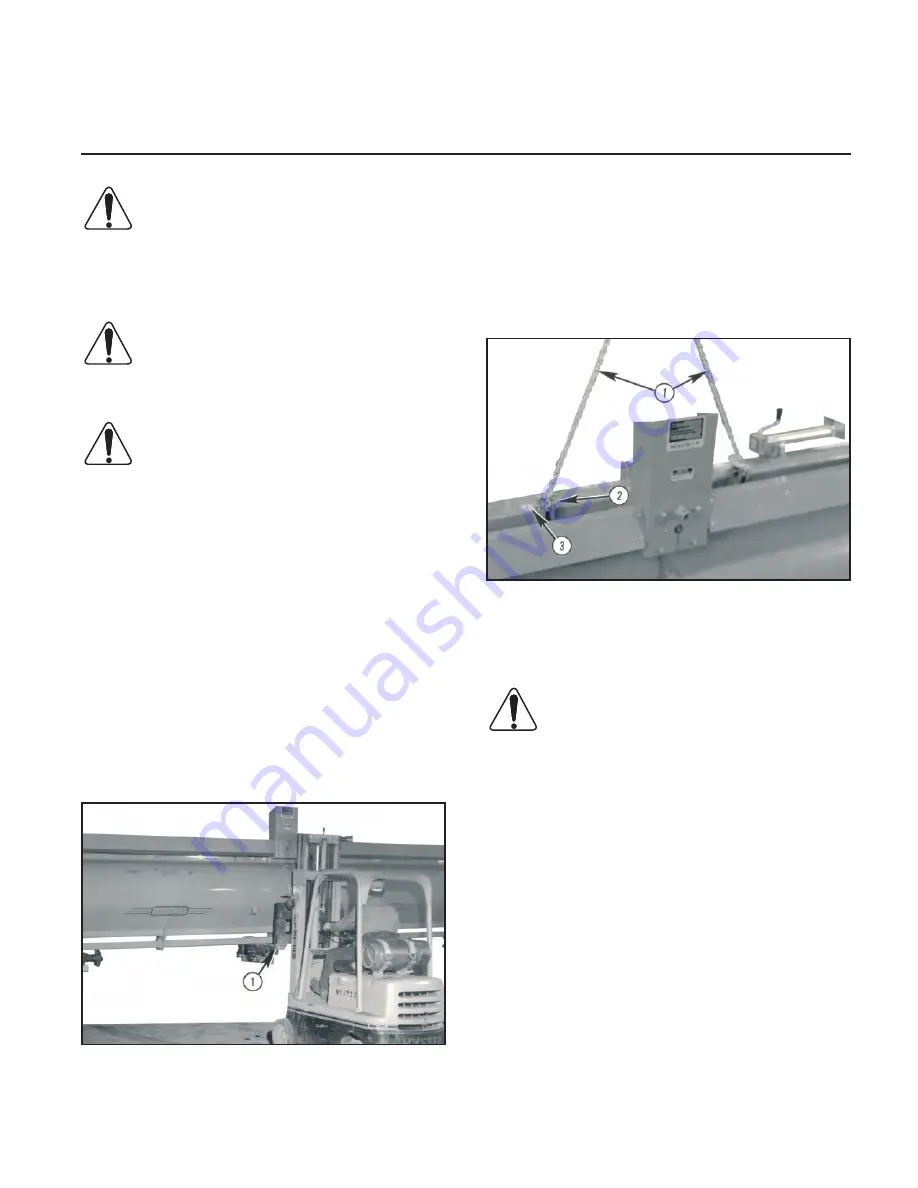
TITLE
Section 43
Assembly 43
ASSEMBLY
WARNING: DEATH OR SERIOUS IN-
JURY CAN RESULT. BEFORE ASSEM-
BLING, READ SAFETY-GENERAL AT
FRONT OF THIS MANUAL.
OFFLOADING
Warning: Death Or Serious Injury Can
Result. Use Equipment Capable Of
Safely Handling No Less Than: 3 Ton
(6000#).
WARNING: DEATH OR SERIOUS IN-
JURY CAN RESULT. CLEAR PEOPLE
FROM CARRIER AND OFF-LOADING
AREA. DO NOT OFF-LOAD ON SOFT, OR UN-
EVEN GROUND. AVOID HIGH WORK SPEEDS
AND ‘JACKRABBIT’ MANEUVERING.
HINIKER shredders are shipped vertical with self
contained storage and handling dunnage. They
may be off-loaded with a forklift or an overhead
chain sling.
For forklift off-loading, 2 fork pockets (Item 1),
spaced 32” apart, are provided. The forklift may
approach the shredder from either the knives, or
hood, face. Set forks centerlines 32” apart and po-
sition forklift as close as possible to shipping pack-
age. Lift off carrier and deposit on a firm, clear and
level work area. See Photo 2980.
PHOTO NO. 2980
For overhead chain sling off-loading, use a chain
sling (Item 1) approximately 5’ long on each run.
Fix EACH sling chain hook SECURELY around
both 1” diameter hitch pins (Item 2) where shown
by decal (Item 3). Lift off carrier and deposit on
a firm, clear and level work area. See Photo
2981.
PHOTO NO. 2981
Shredder hitches (whether trailing or 3 point) are
shipped separate from the basic package.
CAUTION: DEATH OR SERIOUS INJU-
RY CAN RESULT. DO NOT ATTEMPT
TO “MANHANDLE” THE HITCHES
WITHOUT PROPER EQUIPMENT. THE 3 POINT
HITCH WEIGHS 220# (100 KG.).
Remove and discard all shipping dunnage as-
sociated with PTO (Item 1). See Photo 3136A.
Do not forget to remove and discard 2 metal dun-
nage brackets (Item 2). Pull out and temporarily
set aside wheels and PTO. Cut bottom skids dun-
nage bands and remove 3/8” lag screws, along
with, dunnage “U” retainers at (Item 3).