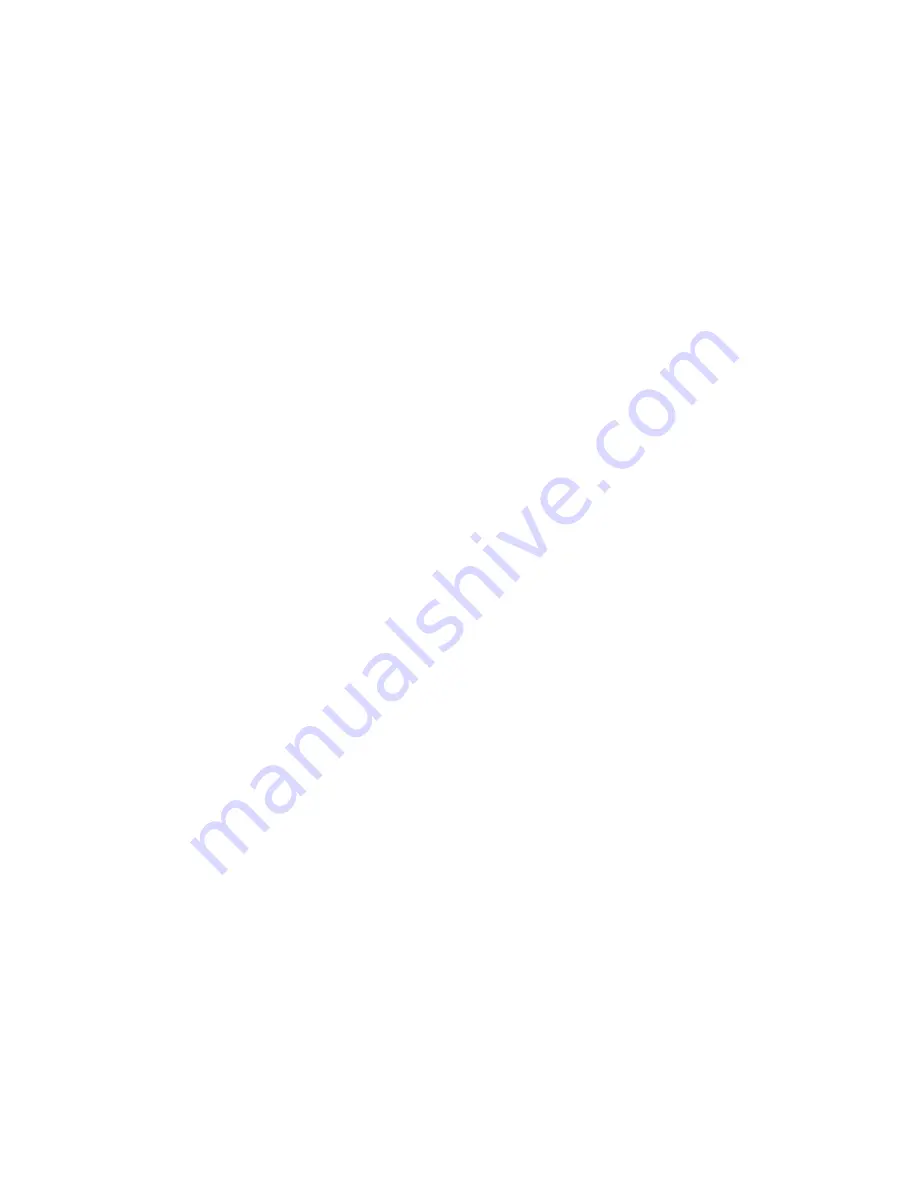
HelmPak Press Control
41
Users Guide
ROBOT FAILED TO CYCLE
This fault occurs when all of the following events occur:
•
The press has completed a stroke in Continuous Mode
•
The robot has not cycled to initiate another stroke
•
The robot wait timer has been satisfied
Clearing fault:
1. Adjust robot wait timer in robot recipe
2. Determine why robots did not cycle
3. Press the fault reset push button
RUN P.B. TIEDOWN
This fault occurs when all of the following events occur:
•
The E-stop safety relay Input (I:4/0) is HIGH.
•
The press is not in motion
•
The Push Button switches are depressed or inputs received to indicate this position
•
The timer has counted for TWO seconds
Clearing fault:
1. Release Push Buttons
2. Press the fault reset push button
SHUTHEIGHT RESOLVER FAULT
This fault occurs when all of the following events occur:
•
The resolver module has determined there is a fault with the resolver or cabling
Clearing fault:
1. Press the fault reset push button
2. If fault persists check resolver cable connection, and cycle power on control
SLIDE ADJUST CONTACTOR FAILED OFF
This fault occurs when all of the following events occur:
•
The slide adjust up or down contactor output is off, but the aux contact is on.
Clearing fault:
1. Function check the contactor
2. Press the fault reset push button
SLIDE ADJUST CONTACTOR FAILED ON
This fault occurs when all of the following events occur:
•
The slide adjust up or down contactor output is on, but the aux contact is off.
Clearing fault:
1. Function check the contactor
2. Press the fault reset push button
SLIDE ADJUST DOWN LIMIT
This fault occurs when all of the following events occur:
•
The slide adjust lower limit is not made, signal A I:2/8 should be high.
Clearing fault:
1. Move slide up, until switch is made and signal is high.
2. Verify switch is working
3. Press the fault reset push button