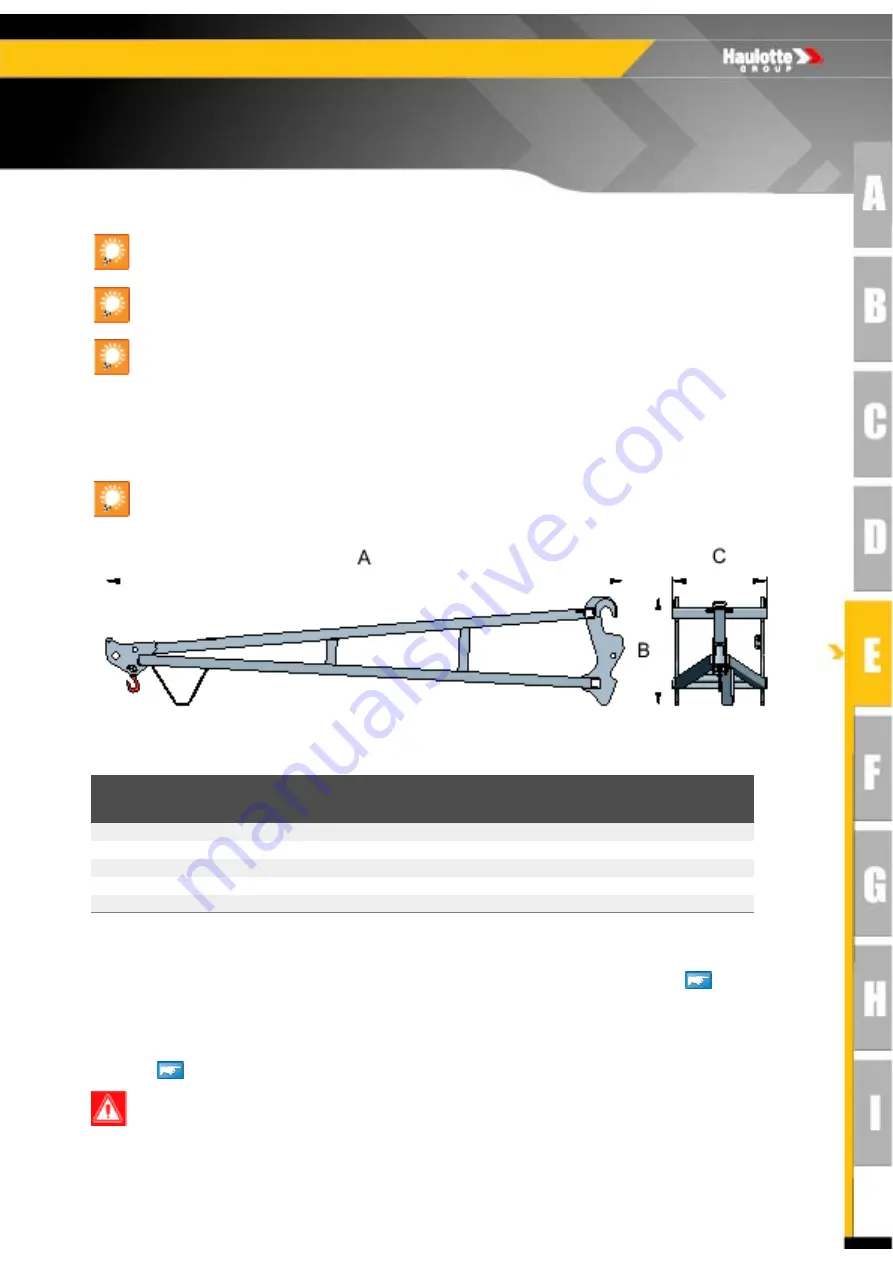
117
2420344510 E
11.11
AUS
Telescopic handlers
E
- Attachments
5.9 -
FLY JIB 4 M(13 FT1 IN), 0,6 T (1323 LB) ON TELESCOPIC ARM
5.9.1 - Characteristics
Fly jib, fitted with swivel hook, mounted on telescopic jib designed to operate under dynamic
and static load.
5.9.2 - Fly jib control
The joystick (P211) controls movements of the boom and attachment tilt (
Section C 2.5.8
-Joystick).
5.9.3 - Attachment installation procedure
Section E 5 - Attachment installation.
Familiarize yourself with the information provided on the attachment identification plate.
Use the capacity table (load chart booklet) corresponding to this attachment located in the cab.
Keep the specific instructions for the forks in the manual holder situated behind the cab seat, with the
telehandler operator manual.
The safety coefficient used is in compliance with the legislation on lifting apparatus or attachment tests.
Fly jib 4 m(13 ft1 in), 0,6 t (1323 lb) on telescopic arm
Marking
Metric
Imperial
A
4,215 m
(13 ft10 in)
B
0,880 m
(2 ft11 in)
C
0,770 m
(2 ft6 in)
Weight
276 kg
(609 lb)
Maximum load, machine halted
600 kg
(1323 lb)
Incorrect installation could result in the attachment or load disengaging, causing death or serious injury.
Summary of Contents for HTL 3210
Page 2: ...2 2420344510 E 11 11 AUS Telescopic handlers...
Page 12: ...12 2420344510 E 11 11 AUS Telescopic handlers...
Page 74: ...74 2420344510 E 11 11 AUS Telescopic handlers D Operation...
Page 80: ...80 2420344510 E 11 11 AUS Telescopic handlers E Attachments HTL4010 load capacity chart...
Page 146: ...146 2420344510 E 11 11 AUS Telescopic handlers F Emergency procedure...
Page 159: ...159 2420344510 E 11 11 AUS Telescopic handlers H Lubrication and maintenance...