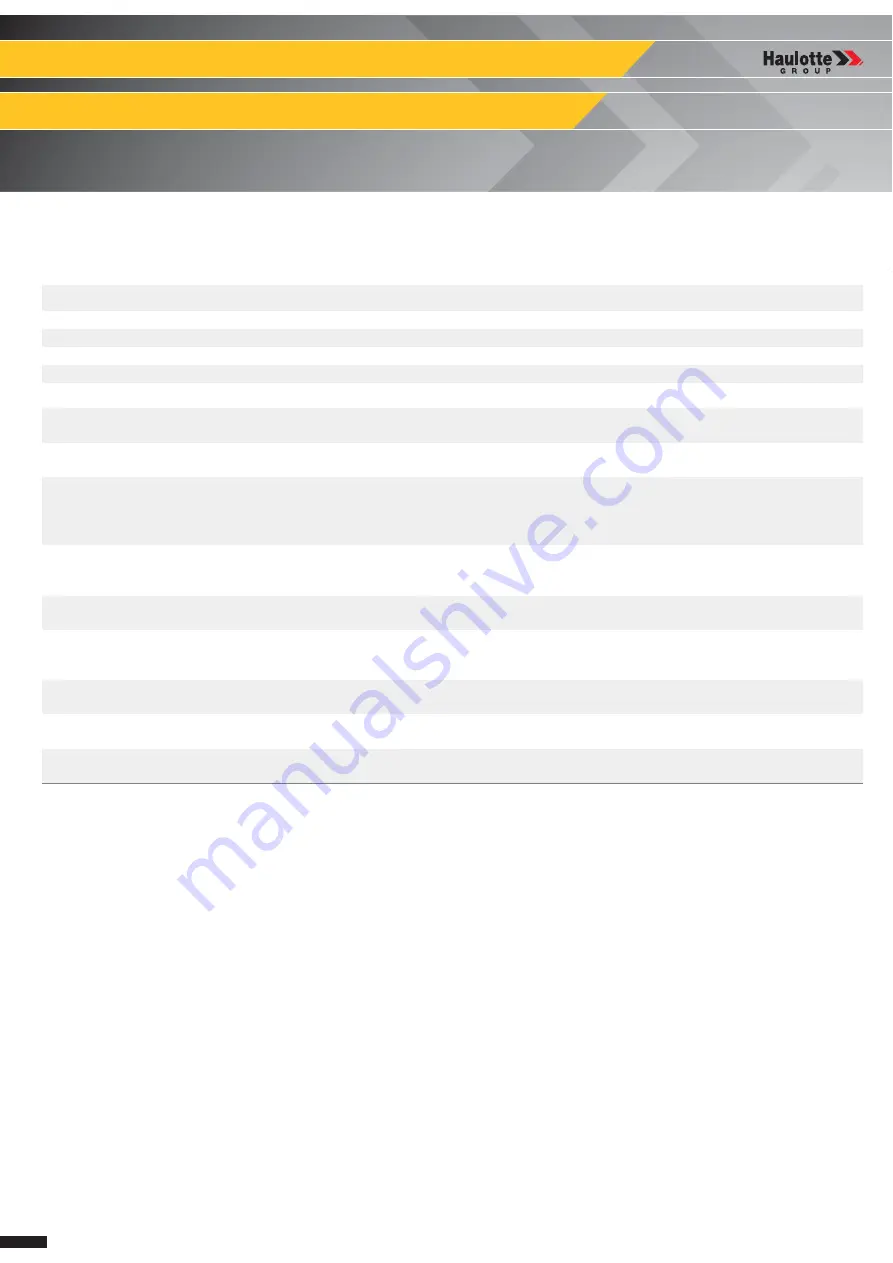
218
4000511390
E03.16 USA
/
GB
Upper boom
Procedure of dismantling / reassembling hydraulic rotary actuators
MS0028
9 - Troubleshooting Guide
Problem
See
Shaft rotates slowly or not at all
1 - 6
Operation is erratic or not responsive
7
Shaft will not fully rotate
8 - 9
Selected position cannot be maintained
3 - 4 - 7
Causes
Solutions
1.
Insufficient torque output
Verify correct operating pressure. Do not exceed OEM's pressure
specifications. Load may be above maximum capacity of the actuator.
2.
Low rate of fluid flow
Inspect ports for obstructions and hydraulic lines for restrictions and
leaks.
3.
Control or Counterbalance valve has internal leak
Disconnect hydraulic lines and bypass valve. Leave valve ports open
and operate the actuator through housing ports (do not exceed OEM's
operating pressure). The valve must be replaced if a steady flow of
fluid is seen coming from the valve ports.
4.
Piston and/or shaft seal leak
Remove the plug and the housing's valve ports. Operate the actuator
through the housing ports. Conduct the internal leakage test as
described in the Testing Section of this manual.
5.
Corrosion build-up on the thrust surfaces
Re-build the actuator. Remove all rust and then polish. Replacement
parts may be needed.
6.
Swollen seals and composite bearings caused by
incompatible hydraulic fluid (Standard actuators
only)
Re-build the actuator. Use fluid that is compatible with seals and
bearings. Contact HAULOTTE Services® for more information.
7.
Air in actuator
Purge air from actuator. See bleeding procedure starting of this
manual.
8.
Twisted or chipped gear teeth overload conditions
Check for binding. Actuator may or may not be able to be rebuilt and
may need to be replaced.
9.
Port fittings are obstructing the piston during stro-
ke
Check thread length of port fittings. Fittings should not reach inside the
housing bore.
Summary of Contents for HT21RT O
Page 86: ...86 4000511390 E03 16 USA GB General data Breaking test procedure MS0004 Notes...
Page 132: ...132 4000511390 E03 16 USA GB Chassis and turntable KUBOTA diesel engine MS0029 Notes...
Page 142: ...142 4000511390 E03 16 USA GB Chassis and turntable Overload system MS0017 Notes...
Page 188: ...188 4000511390 E03 16 USA GB Upper boom Boom adjustment procedure MS0015 Notes...
Page 192: ...192 4000511390 E03 16 USA GB Upper boom Boom angle sensor adjustment MS0018 Notes...
Page 222: ...222 4000511390 E03 16 USA GB Hydraulics Hydraulic oil Level Replacement MS0019 Notes...
Page 231: ...231 4000511390 E03 16 USA GB Hydraulics Hydraulic ways MS0023 F o l i o 2 2...
Page 233: ...233 4000511390 E03 16 USA GB Hydraulics Hydraulic ways MS0023 F o l i o 2 2...
Page 235: ...235 4000511390 E03 16 USA GB Hydraulics Hydraulic ways MS0023 F o l i o 2 2...
Page 237: ...237 4000511390 E03 16 USA GB Hydraulics Hydraulic ways MS0023 F o l i o 2 2...
Page 239: ...239 4000511390 E03 16 USA GB Hydraulics Hydraulic ways MS0023 7 Jib...
Page 240: ...240 4000511390 E03 16 USA GB Hydraulics Hydraulic ways MS0023 Notes...
Page 242: ...242 4000511390 E03 16 USA GB Electric Electrical wiring MS0025 Notes...