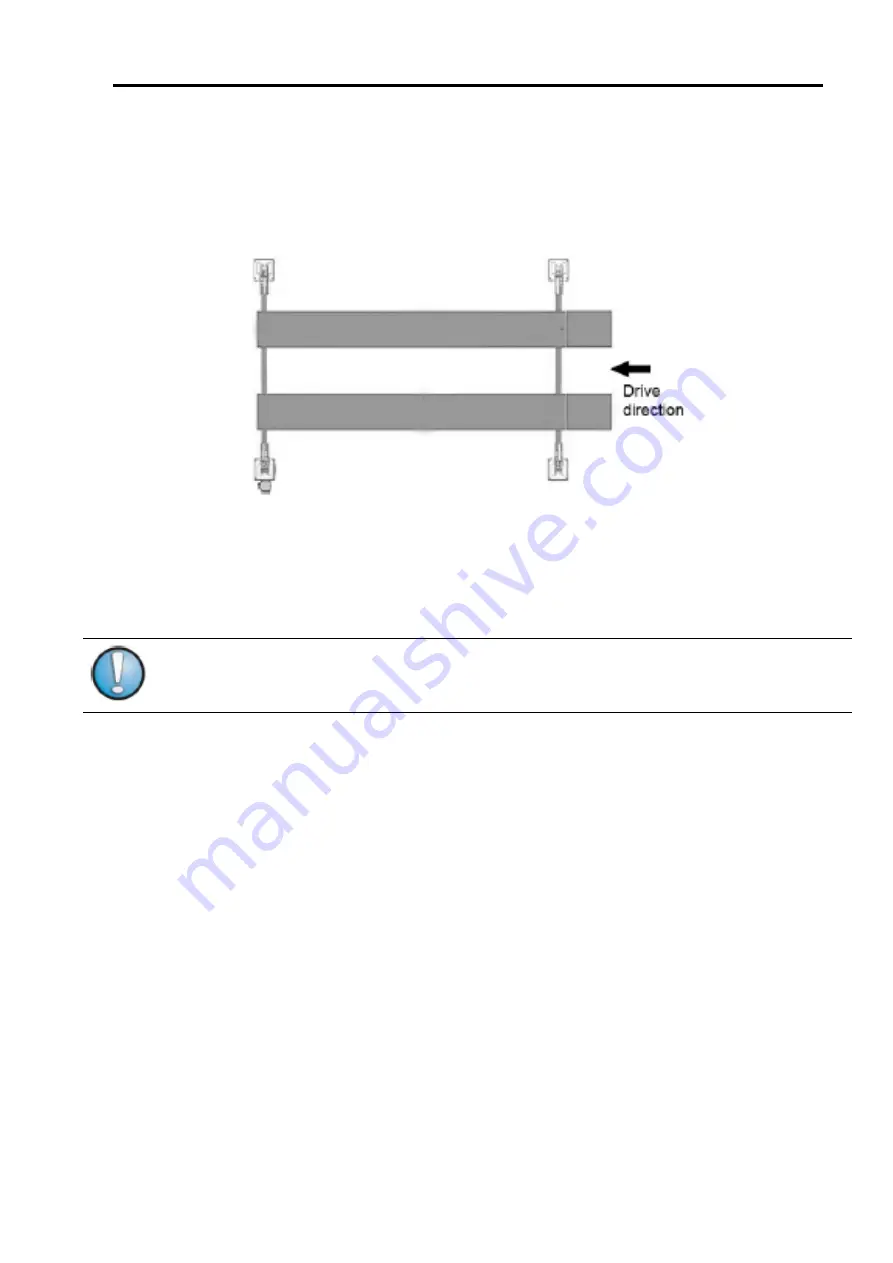
Four post workshop lift HAPP27
Version 5
WWW.HAPP.COM.AU
42
Operation
Loading vehicle onto lift
1 Fully lower the platform.
2 Slowly position vehicle midway between platforms. Apply the parking brake
3. leave vehicle and remain clear of lift
Always lift the vehicle using all four wheels.
Raising
l
Position the vehicle at the centre of the platform.
l
Check to make sure that the vehicle is secured.
l
Ensure all people and objects are clear from hoist
l
Place the pads in the positions
l
Connect the power.
l
Press green button on power unit to raise the vehicle
l
The safety latches should make a slight clicking noise on each hoist as the hoist raises, if
they are not clicking it is likely the safety release lever is not disengaged fully.
l
To rest the lift in standing position at the desired height by releasing the green button.
l
Press lowering handle on pump assembly to lower hoist onto safety latches. Ensure all four
safety latches are engaged.
Note:
Always ensure that the lift rests steadily and safely latches are engaged before any
attempt is made to work on or near the vehicle.