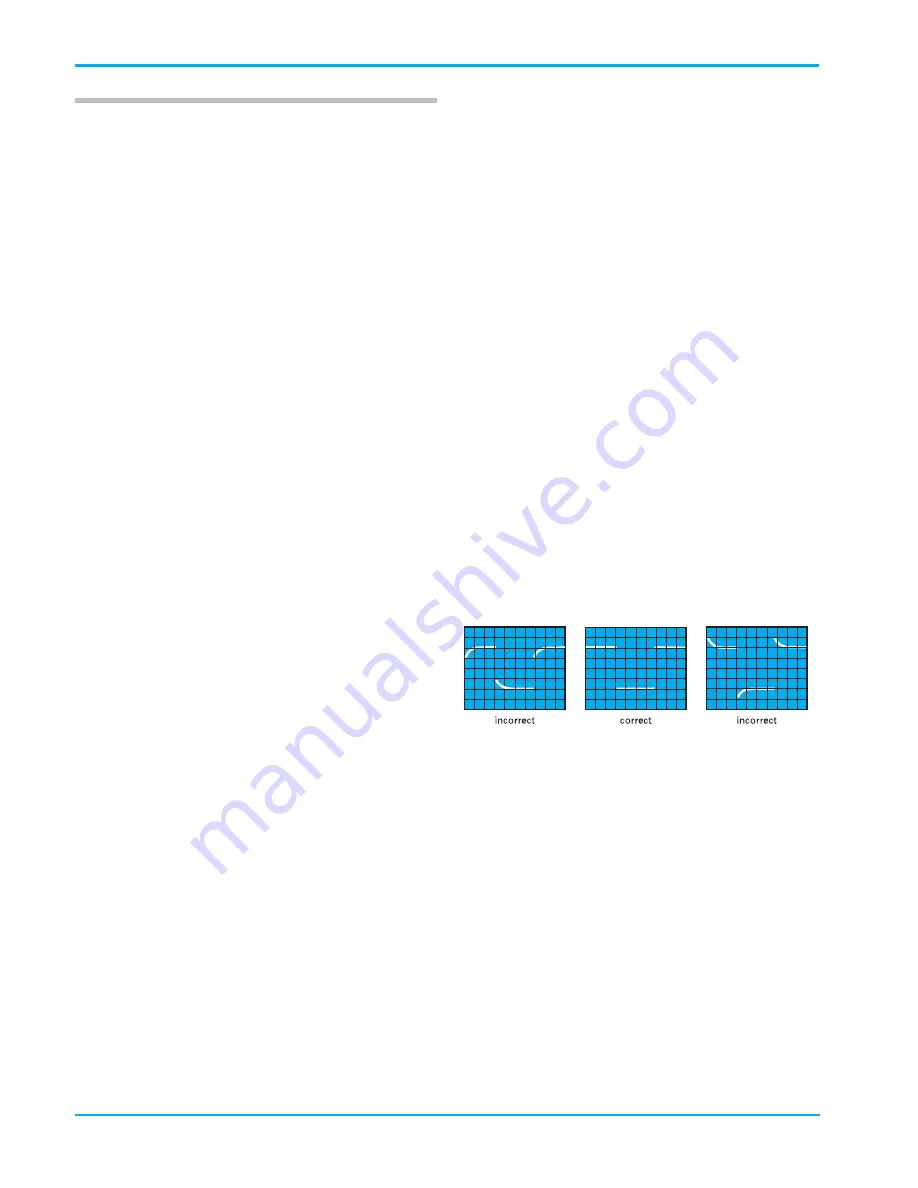
Subject to change without notice
24
First Time Operation
The following text assumes that the
”SAFETY”
section of this
manual has been read carefully and understood.
Each time before the instrument is put into operation check that
the oscilloscope is connected to protective earth. For that reason
the power cable must be connected to the oscilloscope and the
power outlet. Then the test lead(s) must be connected to the
oscilloscope input(s). Check that the device under test is switched
off and connect the test lead(s) to the test point(s). Then switch
on the instrument and afterwards the device under test.
The oscilloscope is switched on by depressing the red
POWER
pushbutton. After a few seconds the
HAMEG
logo and the
instrument software release is displayed on the screen, if this
function is active. As long as the
HAMEG
logo is visible different
internal checks are made. Thereafter the instrument will revert to
its last used operating mode.
If after that no trace is visible, the
AUTO SET
pushbutton should
be pressed briefly. This selects the Yt mode and medium trace
and readout intensity
(
please note ”AUTOSET”)
. Adjust
Y-
POS.I and X-POS
.
controls to centre the baseline. Set
INTENS.
for
suitable
brightness
(intensity) and
FOCUS
for optimum
sharpness (input(s) grounded) of the trace. The oscilloscope is
now ready for use.
If the
AUTOSET
function was not used and only a spot appears
(CAUTION! CRT phosphor can be damaged), reduce the intensity
immediately and check that the XY mode is not selected (XY not
displayed in the readout).
To obtain the maximum life from the cathode ray tube, the
minimum intensity setting necessary for the measurement in
hand and the ambient light conditions should be used.
Particular care is required when a single spot is displayed, as a
very high intensity setting may cause damage to the fluorescent
screen of the CRT. Switching the oscilloscope off and on at short
intervals stresses the cathode of the CRT and should therefore be
avoided.
The instrument is so designed that even incorrect operation will
not cause serious damage.
Trace Rotation TR
In spite of Mumetal shielding of the CRT, effects of the Earth’s
magnetic field on the horizontal trace position cannot be completely
avoided. This is dependent upon the orientation of the oscilloscope
on the place of work. A centred trace may not align exactly with
the horizontal center line of the graticule. A few degrees of
misalignment can be corrected. Please note “Controls and
Readout” section “E: MAIN MENU item 1. TRACE ROT”.
Probe compensation and use
To display an undistorted waveform on an oscilloscope, the probe
must be matched to the individual input impedance of the Y
amplifier.
For this purpose a square wave signal with a very fast rise time
and minimum overshoot should be used, as the sinusoidal
contents cover a wide frequency range.
The built in calibration generator provides a square wave signal
with selectable frequencies and a very fast rise time (<4 ns) from
the output socket below the CRT screen.
As the square wave signals are used for probe compensation
adjustments, neither the frequency accuracy nor the pulse duty
factor are of importance and therefore not specified. The output
provides 0.2 V
pp
±1% (tr <4 ns) for 10:1 probes. When the Y-
deflection coefficient is set to 5 mV/div, the calibration voltage
corresponds to a vertical display of 4 divisions (10:1 probe).
The output socket has an internal diameter of 4.9 mm to
accommodate the internationally accepted shielding tube diameter
of modern probes and F series slimline probes. Only this type of
construction ensures the extremely short ground connections
which are essential for an undistorted waveform reproduction of
non sinusoidal high frequency signals.
Adjustment at 1 kHz
The C-trimmer adjustment (low frequency) compensates the
capacitive loading on the oscilloscope input. By this adjustment,
the capacitive division assumes the same ratio as the ohmic
voltage divider to ensure the same division ratio for high and low
frequencies, as for DC. (For 1:1 probes or switchable probes set
to 1:1, this adjustment is neither required nor possible). A
baseline parallel to the horizontal graticule lines is essential for
accurate probe adjustments.
(See also ”Trace rotation TR”).
Connect the 10:1 probe to the
input of the channel it is to be
adjusted for and don‘t mix up the probes later (always use that
particular probe with the same channel). Set the deflection
coefficient to 5mV/div and the input coupling to DC. The time
deflection coefficient should be set to 0.2ms/div. All deflection
coefficients should be calibrated (Variable controls at CAL position).
Plug the probe tip into the calibrator output socket.
Approximately 2 complete waveform periods are displayed on
the CRT screen. The compensation trimmer should be adjusted.
The location of the low frequency compensation trimmer can be
found in the probe information sheet. Adjust the trimmer with the
insulated screwdriver provided, until the tops of the square wave
signal are exactly parallel to the horizontal graticule lines (see
1kHz diagram). The signal height should then be 4div ± 0.16div (=
4 % (oscilloscope 3% and probe 1%). During this adjustment, the
signal edges will remain invisible.
Adjustment at 1 MHz
Probes
HZ51
,
52
and
54
can also be HF compensated. They
incorporate resonance de-emphasing networks (R-trimmer in
conjunction with capacitor) which permit probe compensation in
the range of the upper frequency limit of the Y amplifier. Only this
compensation adjustment ensures optimum utilization of the full
bandwidth, together with constant group delay at the high
frequency end, thereby reducing characteristic transient distortion
near the leading edge (e.g. overshoot, rounding, ringing, holes or
bumps) to an absolute minimum.
Using the probes
HZ51
,
52
and
54
, the full bandwidth of the
oscilloscope can be utilized without risk of unwanted waveform
distortion.
First Time Operation
Summary of Contents for HM504-2
Page 2: ......
Page 3: ...O s c i l l o s c o p e H M 5 0 4 2 Manual English...
Page 39: ...37 Subject to change without notice Front Panel HM504 2...
Page 40: ......
Page 41: ...LEER...