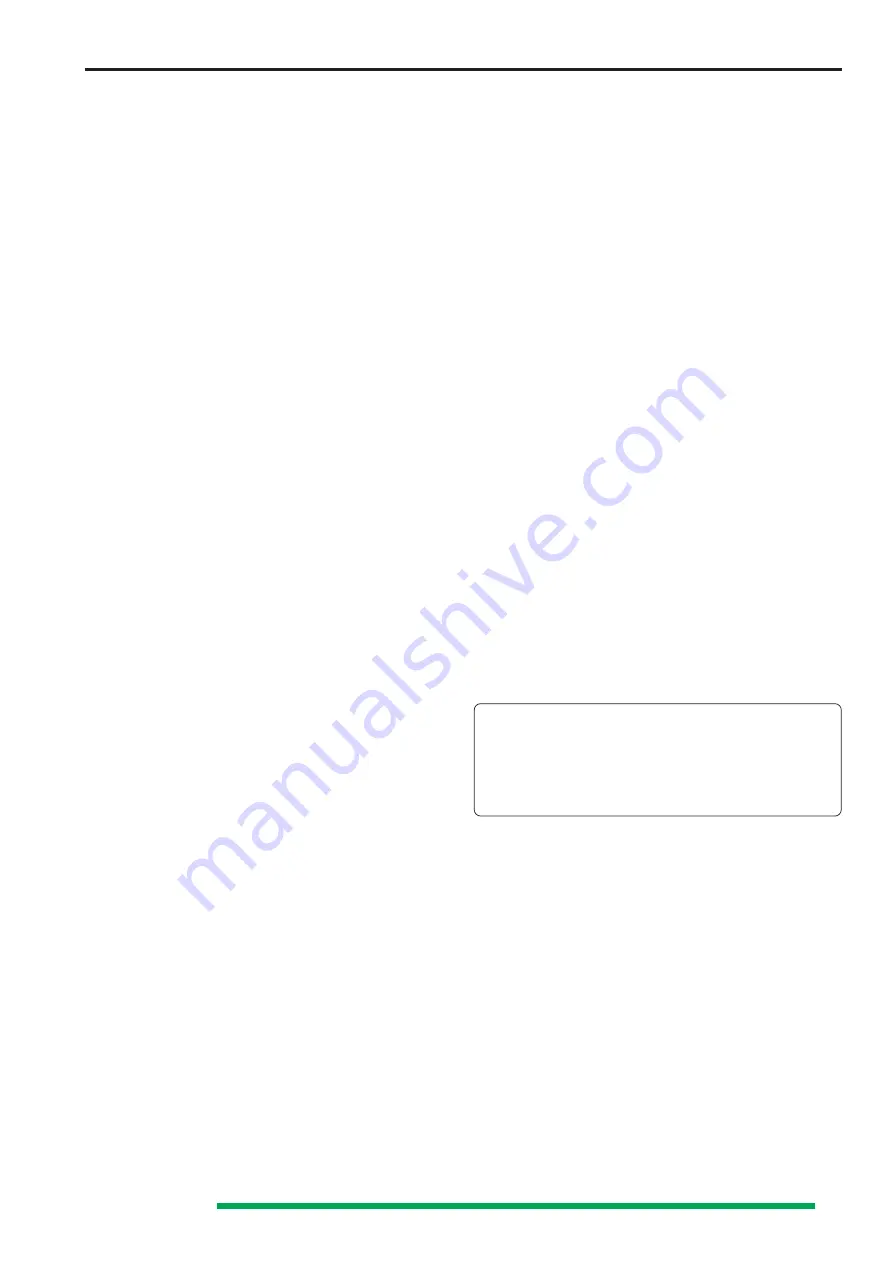
25
Subject to change without notice
mid position (i.e. 20µs/div.). Prior to the commencement of
any check set the time variable control to CAL. The X-MAG.
x10 LED should not light. This condition should be maintained
until the variation ranges of these controls are checked.
Check that the sweep runs from the left to the right side of
the screen (TIME/DIV. setting to 0.1s/div.; X-POS. control in
mid-range). This check is only necessary after changing the
cathode-ray tube.
If a precise marker signal is not available for checking the
Timebase time coefficients, then an accurate sine-wave
generator may be used. Its frequency tolerance should not
be greater than ±1%. The timebase accuracy of the HM304
is given as ±3%, but it is considerably better than this. For
the simultaneous checking of timebase linearity and accuracy
at least 10 oscillations, i.e. 1 cycle every div., should always
be displayed. For precise determination, set the peak of the
first marker or cycle peak exactly behind the first vertical
graticule line using the X-POS. control. Deviation tendencies
can be noted after some of the marker or cycle peaks.
If a precise Time Mark Generator is used for checking, Nor-
mal Triggering (NM LED lights) and TRIG. LEVEL control
adjustment is recommended.
The following table shows which frequencies are required
for the particular ranges.
0.5s/div.
-
2Hz
0.1ms/div. -
10kHz
0.2s/div.
-
5Hz
50µs/div.
-
20kHz
0.1s/div.
-
10Hz
20µs/div.
-
50kHz
50ms/div. -
20Hz
10µs/div.
- 100kHz
20ms/div. -
50Hz
5µs/div.
- 200kHz
10ms/div. -
100Hz
2µs/div.
- 500kHz
5ms/div.
-
200Hz
1µs/div.
-
1MHz
2ms/div.
-
500Hz
0.5µs/div.
-
2MHz
1ms/div.
-
1kHz
0.2µs/div.
-
5MHz
0.5ms/div. -
2kHz
0.1µs/div.
-
10MHz
0.2ms/div. -
5kHz
0.05µs/div. -
20MHz
When the X-MAG. x10 function is active, a marker or cycle
peak will be displayed every 10div. ±5% (with variable control
in CAL. position; measurement in the 5
µ
s/div. range). The
tolerance is better measurable in the 50
µ
s/div. range (one
cycle every 1div.).
Holdoff time
The variation of the holdoff time while turning the HOLD OFF
knob can not be tested without opening the instrument.
However, a visual check can be made if the instrument is not
operated in DELAY mode.
Without an input signal, set TIME/DIV. to 0.05µs/div and time
variable control cw, use automatic peak (value) triggering. At
the left hand stop of the HOLDOFF knob, the trace should
be bright. It should noticeably darken at the right hand stop
of the HOLDOFF knob.
Component Tester
After selecting component tester mode by pressing the
COMP. TESTER button, a horizontal straight line should
appear immediately, when the COMP. TESTER socket is open.
The length of this trace should be approx. 8div if the X MAG.
x10 LED is dark. With connection of the COMP. TESTER
socket to the ground jack in the Y-Section, a vertical straight
line with approx. 6div. height should be displayed. The above
stated measurements have some tolerances.
Trace Alignment
The CRT has an admissible angular deviation ±5° between
the X deflection plane D1-D2 and the horizontal center line of
the internal graticule. This deviation, due to tube production
tolerances (and only important after changing the CRT), and
also the influence of the earths magnetic field, which is
dependent on the instruments North orientation, are
corrected by means of the TR potentiometer. In general, the
trace rotation range is asymmetric. It should be checked,
whether the baseline can be adjusted somewhat sloping to
both sides round about the horizontal center line of the
graticule. With the HM304 in its closed case, an angle of
rotation ±0.57° (0.1div. difference in elevation per 10div.
graticule length) is sufficient for the compensation of the
earths magnetic field.
Service Instructions
General
The following instructions are intended as an aid for the
electronic technician, who is carrying out readjustments on
the HM304, if the nominal values do not meet the
specifications. These instructions primarily refer to those
faults, which were found after using the Test Instructions.
However, this work should only be carried out by properly
qualified personnel. For any further technical information call
or write to HAMEG. Addresses are provided at the back of
the manual. It is recommended to use only the original packing
material, should the instrument be shipped to for service or
repair (see also Warranty).
Instrument Case Removal
The rear cover can be taken off after unplugging the power
cords triple-contact connector and after two nuts the washers
have been removed. If a cross recessed pan head screw is
present on the bottom of the instrument, it must be removed
too. While the instrument case is firmly held, the entire
chassis with its front panel can withdrawn forward. When
the chassis is inserted into the case later on, it should be
noticed that the case has to fit under the flange of the front
panel. The same applies for the rear of the case, on which
the rear cover is put.
Caution!
During opening or closing of the case, the instrument
must be disconnected from all power sources for
maintenance work or a change of parts or components.
If a measurement, trouble-shooting, or an adjustment
is unavoidable, this work must be done by a specialist,
who is familiar with the risk involved.
When the instrument is set into operation after the case has
been removed, attention must be paid to the acceleration
voltage for the CRT -2025V and to the operating voltages for
both final amplifier stages 175V and 144V. Potentials of these
voltages are on the PS-Board, the CRT-PCB, on the upper
and lower PCBs. Such potentials are moreover on the
checkpoint strips on the upper and lower horizontal PCBs.
They are highly dangerous and therefore precautions must
be taken. It should be noted furthermore that shorts occuring
on different points of the CRT high voltage and unblanking
circuitry will definitely damage some semiconductors and the
opto-coupler. For the same reason it is very risky to connect
capacitors to these points while the instrument is on.
Capacitors in the instrument may still be charged, even when
the instrument is disconnected from all voltage sources.
Normally, the capacitors are discharged approx. 6 seconds
after switching off. However, with a defective instrument an
interruption of the load is not impossible. Therefore, after
switching off, it is recommended to connect one by one all
terminals of the check strips on the upper PCB across 1k
Ω
to ground (chassis) for a period of 1 second.