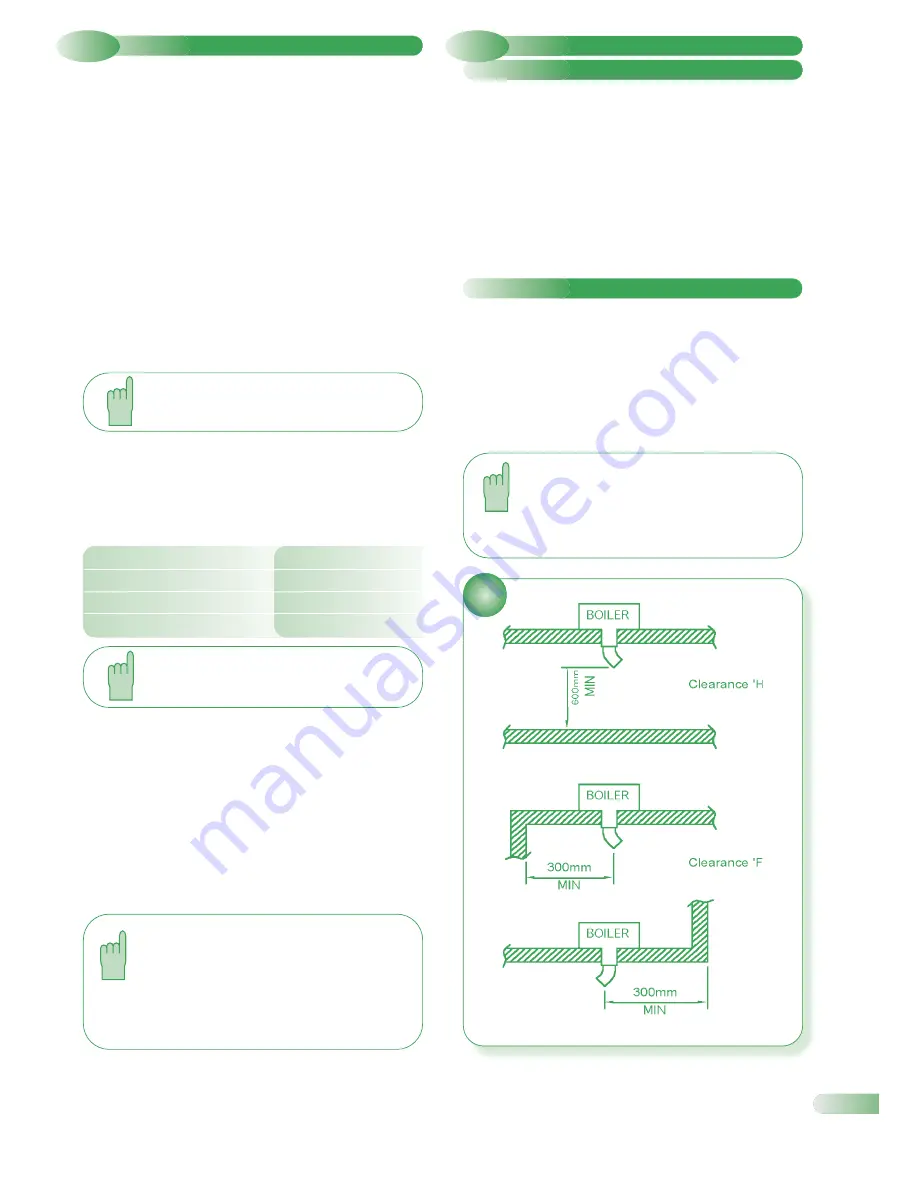
9
The following additional concentric kits are available as optional
extras.
Flue Extension Ducts
- 1000 mm and 500 mm long, (each
duct extends the flue length by up to 950 mm and 450 mm
respectively).
93° Extension Elbow
- Allows an additional bend in the flue,
and has an 'equivalent length' of 1550 mm. This elbow is
mechanically different from the flanged elbow supplied as
standard with the appliance, but has the same equivalent length.
45° Extension Elbow
- Allows an additional bend in the flue
and has an 'equivalent length' of 775 mm.
Vertical Turret Socket
- For use with elevated horizontal flues
and vertical terminals.
Vertical Roof Terminal
- For use where an external wall is not
available, or where it is desirable to route the ducts vertically.
For installation details refer to the instructions
provided with the individual flue kits.
These optional kits may be used with the standard flue kits to
produce an extensive range of flue options, providing that the
following rules are strictly obeyed.
a)
The maximum/minimum permissible length of the room sealed
flue system are:
2.8
ADDITIONAL CONCENTRIC FLUE KITS
The 'equivalent' flue length must not exceed the
maximum values stated.
Horizontal flue terminal (all orientations) maximum 10000 mm (394 in)
Horizontal flue terminal (rear exit)
minimum 250 mm (10 in)
Vertical flue terminal
maximum 12000 mm (472 in)
Vertical flue terminal
minimum 600 mm (23
1
/
2
in)
Refer to Figures 2 and 3 to determine which option
kits are required before commencing the installation.
Instructions for installing the appliance with a
horizontal flue and straight extension ducts are
included in the main text of these instructions
(section 4.8).
b)
The standard terminal must always be fitted horizontally;
horizontal ducts must have a continuous fall towards the appliance
of 2.5°. This ensures condensate runs back into the appliance from
the flue system. The vertical terminal must always be used if a
vertical outlet is required.
c)
The concentric flue system must use either a flanged elbow or
a vertical flue turret socket at the entry/exit to the appliance.
d)
All joints must be correctly made and secured in accordance
with the installation instructions. When cutting ducts, avoid swarf,
uneven and sharp edges to maintain duct integrity.
The resistance of the diverter is equivalent to 0.5
metre of flue length. Ensure this is used when
calculating the maximum allowable flue length.
(maximum horizontal flue length restricted to 4.5
metres when using the plume diverter).
Plume Diverter Kit Part No: 956103
(For use with Standard horizontal telescopic flue kit - Part no
956120 - only)
This kit is provided to assist in fitting a condensing boiler with
reduced clearances when fitted in good practice according to the
Guide to Condensing Boiler Installation published by
DEFRA/HMSO.
This kit allows the boiler flue outlet to be directed to the left or to
the right only.
Under certain operating conditions condensing appliances have a
tendency to form a plume of water vapour at the terminal.
Therefore consideration should be given when fitting the Plume
Diverter in terms of plume dispersal onto adjacent surfaces and
neighbouring properties.
a)
Refer to section 2.5 for instructions on fitting the flue system.
Also see Figure 5 for all other clearances.
INSTALLATION
PLUME DIVERTER TERMINAL
INSTALLATION INSTRUCTIONS
2.8.1
3h
Summary of Contents for Eden CBX
Page 13: ...4b Domestic Hot Water Mode CBX 4c Central Heating Mode SBX 11...
Page 28: ...26 24 CBX SBX...
Page 31: ...INTERNAL WIRING DIAGRAMS 7 7 1 FUNCTIONAL FLOW WIRING DIAGRAM 29 29...
Page 44: ...42 54 1 2 3 4 5 6 7 8 9 10 11 12 13 14 15 16 17 18 19 20 21 22 23 24...
Page 45: ......
Page 46: ......