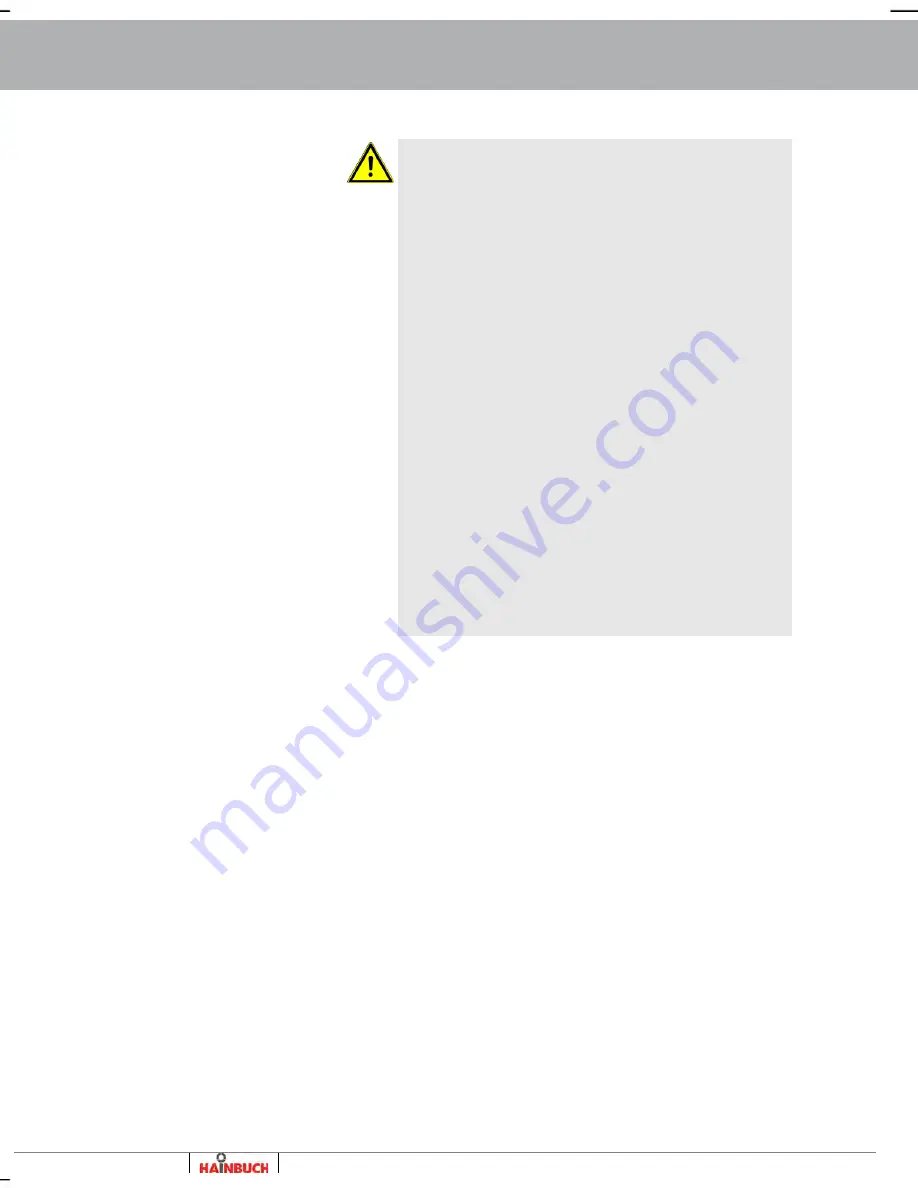
Segmented mandrel T213 – Safety
2.8 Screws
Moving parts
WARNING!
Danger of injury due to screws and stud
screws being accelerated out of the device!!
Screws and stud screws radially attached to
the product can be accelerated out of the de-
vice and cause severe injuries.
At the product radially mounted screws and
stud screws which were loosened for assem-
bly and maintenance must be re-tightened
with the correct tightening torque!
The tightening torque is given at the product
itself, near the screw or threaded pin, and/or
given in chapter »Bolt torque«.
All screws or stud screws that are not
marked with a tightening torque specification
are tightened with the prescribed tightening
torque and locked [medium-strength bonding]
in the factory and should only be unscrewed
after consultation with the manufacturer. If in
doubt you must contact the manufacturer im-
mediately do determine the subsequent pro-
cedure.
18
Order h49 7144.907-333