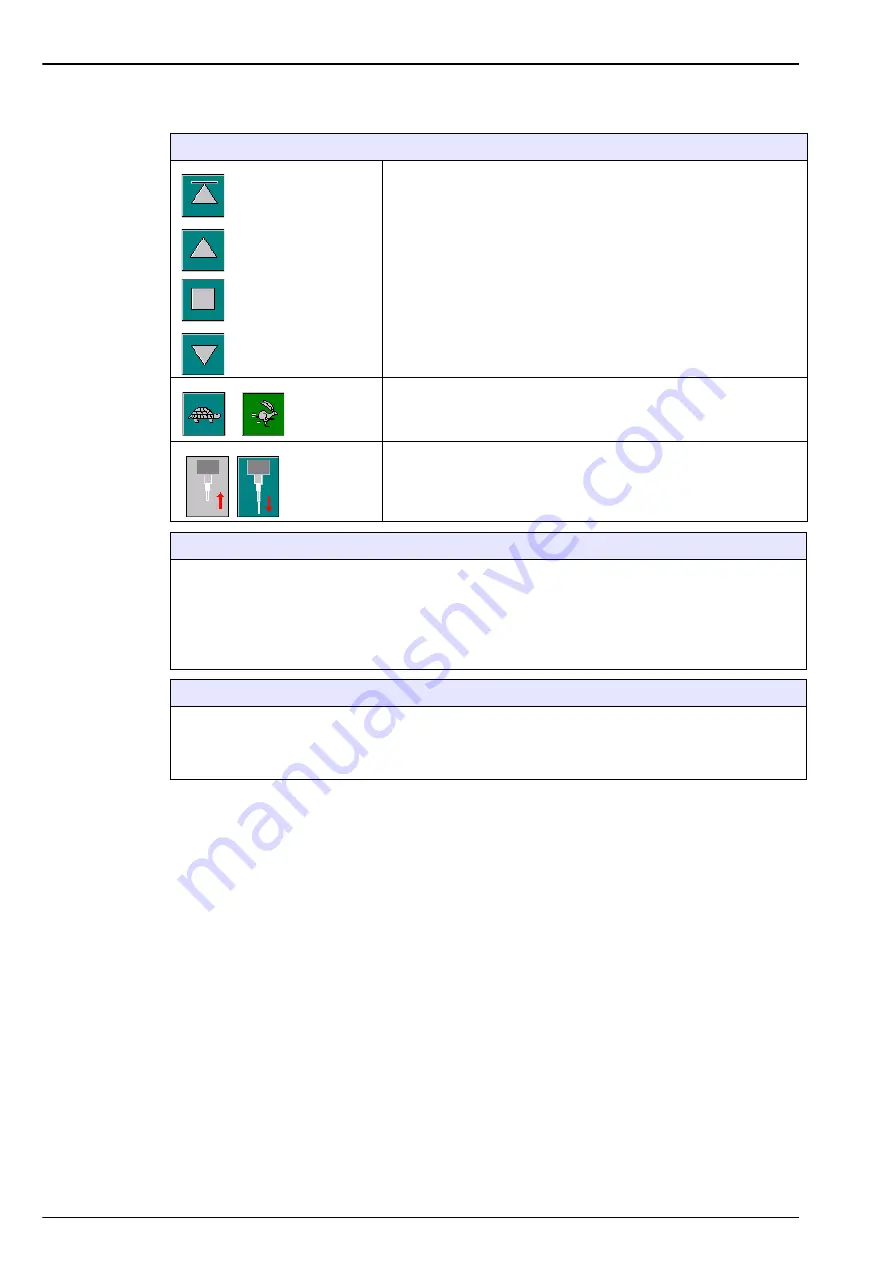
60
Maintenance
9.3.3 Actuator verification
Manual displacement
Move to the home
position (top)
Move up
Stop (only applicable
when moving to the
home position)
Move down
Press on the icons displayed left to perform the required operation on
the piercing assembly.
The current position is displayed on the left side of the screen as the
assembly moves either up or down.
It is advisable to check the displacement process using the two
different speed settings by pressing on these two buttons (tortoise for
slow and hare for fast).
Press on the icon with the down arrow to lower the needle without
moving the piercing assembly.
Press on the icon with the up arrow to raise the needle back into the
home position.
Ultrasound ON/OFF
Switch between having the ultrasound system on or off.
Important Note:
Before turning ON, remove any pierced packages from the package holder to avoid any
liquid spillage.
With some water in the base of the package holder, test the system is working by moving your finger
across the base of the package holder and toggling the switch between ON and OFF. You should sense
a noticeable difference.
Lasers ON/OFF
Switch between having the lasers on or off.
Test the system is working by toggling the switch to ON and you should see the two red laser beams
intersecting on the package holder. Toggle the switch back to OFF and the laser beams should
disappear.
Summary of Contents for ORBISPHERE 6110
Page 1: ...DOC024 52 93009 ORBISPHERE Model 6110 Package Analyzer User Manual 08 2013 Edition 5 ...
Page 2: ......
Page 6: ...4 Table of Contents ...
Page 14: ...12 General Information ...
Page 16: ...14 Specifications 2 2 Instrument dimensions Figure 1 Instrument dimensions ...
Page 28: ...26 Installation ...
Page 34: ...32 User Interface and Startup 4 3 Menu structure overview ...
Page 35: ...33 Section 5 Configuration 5 1 Configuration menu overview ...
Page 46: ...44 Configuration ...
Page 56: ...54 Measurement ...
Page 58: ...56 Analysis ...
Page 70: ...68 Spare Parts and Accessories ...
Page 74: ...72 Material Safety Data Sheets MSDS ...
Page 75: ...73 ...