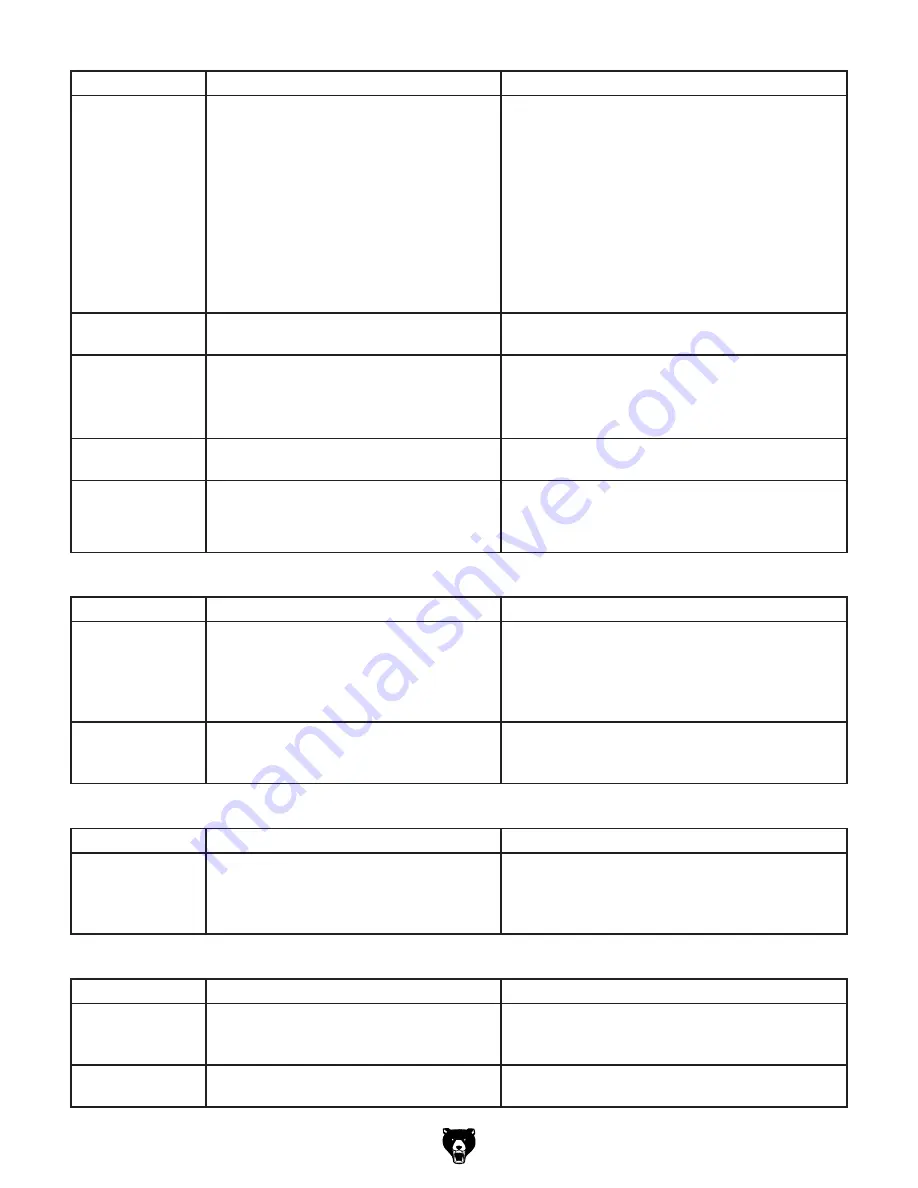
Model G0827 (Mfd. Since 11/17)
-57-
Symptom
Possible Cause
Possible Solution
Bad surface finish.
1. Spindle speed/feed rate too fast for
material type.
2. Depth of cut too deep.
3. Cutting tool is dull or incorrect for
application.
4. Cutting tool rotation is backwards.
5. Workpiece not properly secured.
6. Spindle extended too far down.
7. Non-traveling table axis not locked.
1. Set spindle speed correctly for material type (
Page
36) or use a slower feed rate.
2. Reduce depth of cut.
3. Sharpen cutting tool; select a better cutting tool for
operation.
4. Check for proper cutting tool rotation direction.
5. Properly clamp workpiece to table or in a vise.
6. Fully retract spindle (
Page 38) and raise table
(
Page 30). This increases rigidity.
7. Use Z-axis or other table locks to prevent slight
table movement where axis must be fixed.
Cutting results not
square.
1. Table and spindle not at 90° to each other.
2. Table travel inconsistent.
1. Tram spindle (
Page 58).
2. Adjust gibs (
Page 61).
Lack of power at
spindle.
1. Belt(s) slipping. Oil/grease on belt(s).
2. Incorrect power supply voltage or
frequency.
1. Tension/replace belt(s) (
Page 53);
clean belt(s) of
any oil/grease.
2. Ensure power supply meets correct circuit
requirements (
Page 14).
Spindle does not
fully retract.
1. Worn return spring.
1. Replace return spring.
Control Panel
FORWARD and
REVERSE buttons
do not work.
1. Shorted/disconnected wiring.
2. Button switch at fault.
1. Inspect circuit boards, wiring connections. Replace/
repair as necessary.
Symptom
Possible Cause
Possible Solution
Power feed does
not move table or is
slipping.
1. Table locked.
2. Drive selector not engaged.
3. Sheared pin.
4. Gears not meshing or teeth missing.
5. Motor shaft and gear shaft not engaged.
1. Unlock table locks (
Page 30).
2. Select speed and engage drive selector.
3. Replace pin.
4. Check gears and adjust/replace.
5. Replace clutch.
Operates at high
speed only or is
inconsistent.
1. Rapid micro switch stuck.
2. Wiring harness disconnected.
3. Variable-speed dial (potentiometer) at fault.
1. Lightly tap on it to lower it; replace.
2. Reconnect wiring harness.
3. Replace potentiometer.
Power Feed
Symptom
Possible Cause
Possible Solution
Lamp will not light.
1. Main power not turned ON.
2. Bulb burned out.
3. Short in wiring or wired incorrectly.
1. Press switch/button on lamp or control panel.
2. Replace bulb.
3. Trace/test wiring to ensure proper connections and
verify continuity. Replace or fix as necessary.
Lamp
Symptom
Possible Cause
Possible Solution
DRO doesn't give
reading.
1. DRO not turned ON.
2. DRO not getting power.
1. Switch DRO ON/Power button.
2. Inspect circuit boards, sensors, plugs, and wiring
connections. Replace/repair as necessary.
DRO reading is
incorrect.
1. Initial reading incorrect.
2. Sensor at fault.
1. Zero/Reset DRO at beginning point.
2. Test/replace sensor as necessary.
Digital Readout Unit (DRO)
Summary of Contents for G0827
Page 92: ......