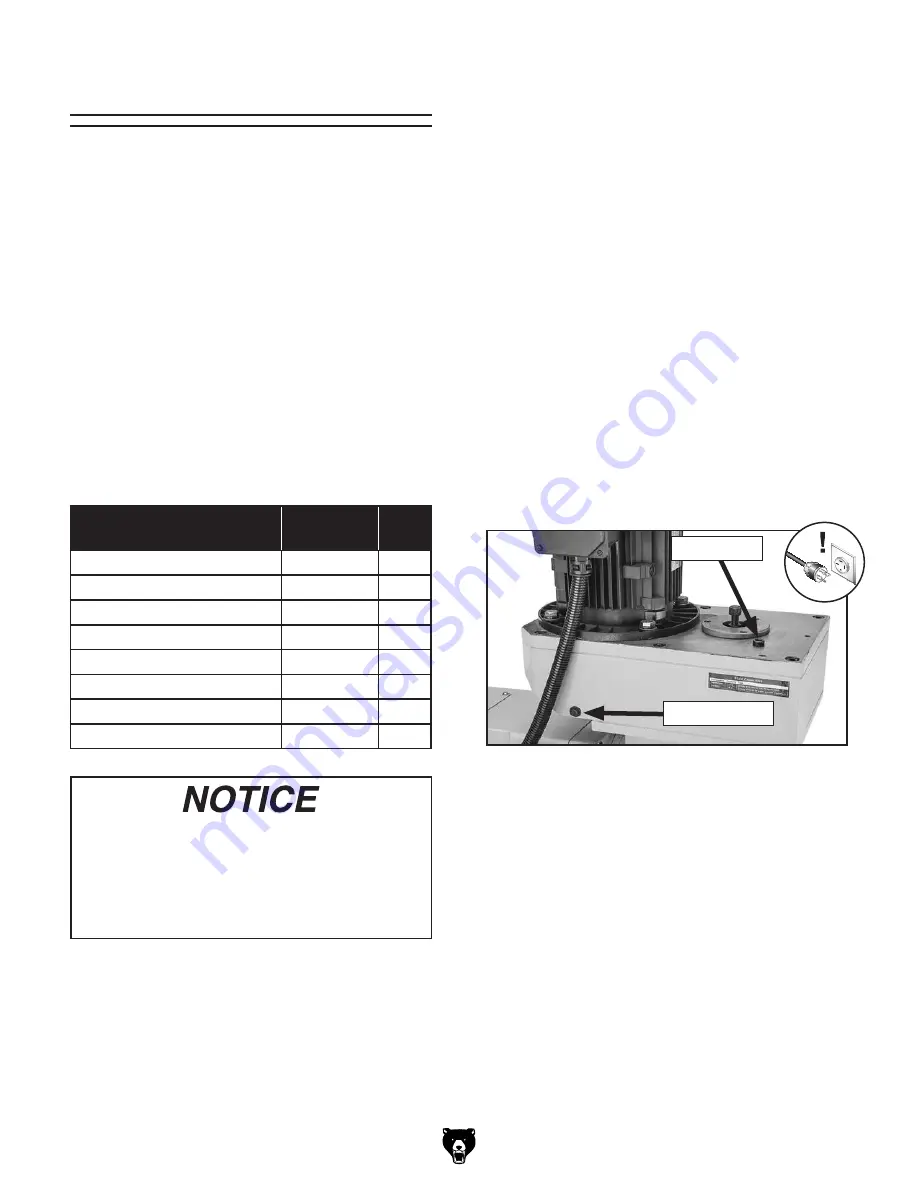
Model G0827 (Mfd. Since 11/17)
-45-
Lubrication
The mill has numerous moving metal-to-metal
contacts that require regular and proper lubrica-
tion to ensure efficient and long-lasting operation.
Use the schedule and information in the chart
below as a daily guide for lubrication tasks.
Other than the lubrication points covered in this
section, all other bearings are internally lubricated
and sealed at the factory. Simply leave them
alone unless they need to be replaced.
DISCONNECT MACHINE FROM POWER before
performing any lubrication task!
Important: Before adding lubricant, clean all
debris and grime from part and nearby area to
prevent contamination of new lubricant.
Lubrication Task
(Hours of
Operation)
Page
Ref.
Ball Oilers
4–8
47
Vertical Spindle Bearings
4–8
48
Quill Exterior
4–8
48
Quill Rack & Pinion
40
49
Table Leadscrews
40
49
Ram Ways
40
49
Z-Axis Bevel Gears
80
49
Power Feed Gears
80
50
The recommended lubrication schedule is
based on light-to-medium usage. Keeping
in mind that lubrication helps to protect
the value and operation of the mill, these
lubrication tasks may need to be performed
more frequently depending on usage.
Tools Needed
Qty
Open-End Wrenches 12, 17, 19mm .............1 Ea.
Hex Wrench 8mm .............................................. 1
Drain Pan (1 Gallon or Larger) .......................... 1
Pump-Type Oil Can with Plastic or Rubber Tip . 1
Mineral Spirits .................................... As Needed
Shop Rags ......................................... As Needed
Brush ................................................................. 1
3. Hold drain pan under drain plug and remove
drain plug. Allow old oil to drain into drain
pan.
4. Replace and tighten drain plug.
To change oil in headstock:
1. DISCONNECT MACHINE FROM POWER!
2. Remove oil fill plug from top of headstock
(see
Figure 72).
Figure 72. Headstock oil fill and drain locations.
Headstock
Oil Type ......Model T23963 or ISO 32 Equivalent
Oil Amount .......................................... 1.9 Quarts
Lubrication Frequency ........................... Annually
The headstock uses ISO 32 machine oil to lubri-
cate the gears, and is equipped with an oil-level
sight glass to gauge when the proper amount of
oil is in the headstock.
The amount of oil in the headstock must be
regularly monitored before each operation to
ensure it doesn't drop below sight glass visibility.
Headstock oil must be changed on an annual
basis to ensure proper lubricity of oil.
Oil Fill Plug
Oil Drain Plug
Summary of Contents for G0827
Page 92: ......