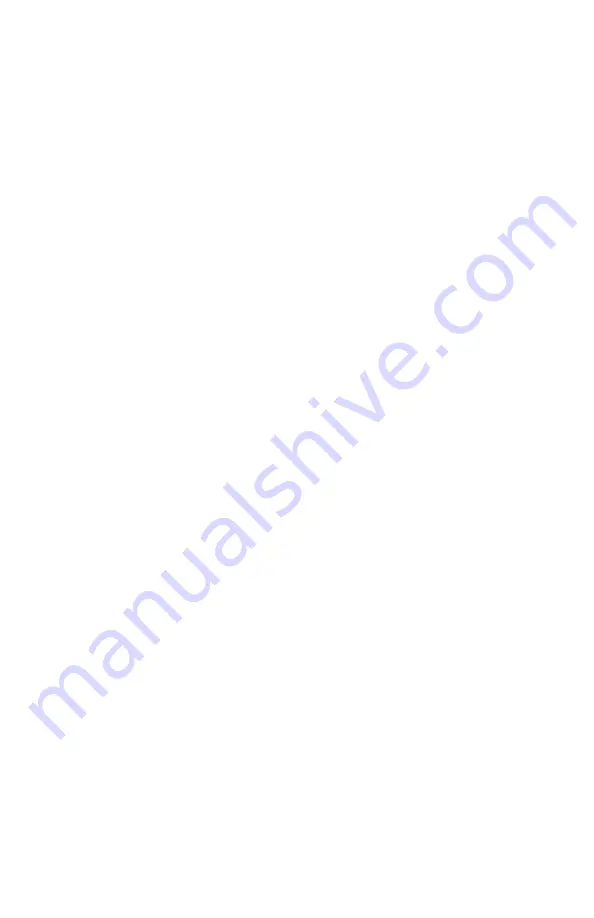
GDS-15-PH 0519
10
PROCESS SAFETY MANAGEMENT [PSM] PROCEDURE:
CHEMICAL DESCALING / SCALEBREAK
®
PRODUCTS
All procedures should be established jointly with all applicable plant personnel
involved in the operation, the following would be included:
1.
Pre-operational safety review with plant operations.
2.
A walk through of all systems to check mechanical integrity of systems being
operated on, valves, associated system components etc.
3.
Establishing complete Isolation of system to be cleaned from any other system.
4.
Hydrostatic testing of condenser system – establishing that the system is
completely isolated from any other system and potential discovery of any pre-
existing leaks – this trial hydrostatic test with water is excellent at discovering
leaks without having product in any unit.
5.
Determination of pump requirements for ScaleBreak
®
injection into units /
logistics on hose connections on inlet and return points.
6.
ScaleBreak
®
general injection process understanding and logistics.
7.
CO2 gas escape / venting requirements in system when calcium carbonate is
being dissolved during descaling.
8.
Leak detection and emergency response If ScaleBreak
®
is injected and a leak is
discovered during ScaleBreak
®
operations.
9.
Understanding of ScaleBreak
®
movement through entire condenser circuit via
supplied drawings during descaling operations.
10.
Monitoring of cleaning process/steps.
11.
Determination of completion of cleaning (hours/contact time,
pH measurements).
12.
ScaleBreak
®
Neutralization and removal procedures. This may involve use of
sodium carbonate, sodium hydroxide, or other alkali material.
13.
Rinsing and flushing of condenser units after cleaning.
14.
Passivation procedures of condenser metallurgy by the plant after cleaning
with corrosion inhibitors.
15.
Inspection of cleaned system by plant personnel - boroscopes.