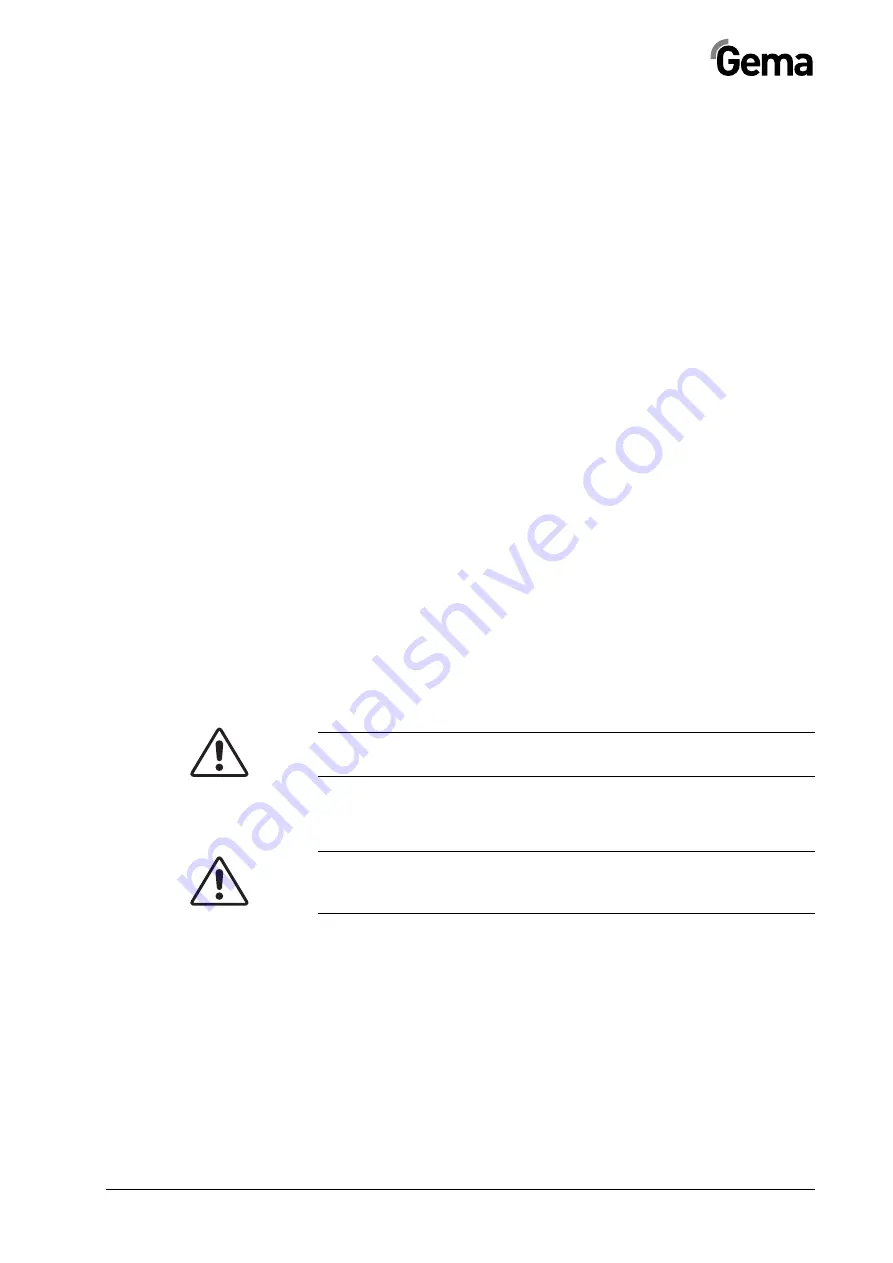
V 10/17
MagicCompact BA04
General safety regulations
•
7
Operating the equipment
In order to be able to operate the equipment safely, it is necessary to be
familiar with the safety regulations, the operational characteristics and
functioning of the various plant components.
For this purpose, read the safety notes, this operating manual and the
operating instructions of the control unit with touch panel, before starting
up the plant.
In addition, all further equipment-specific operating instructions, e.g. the
OptiFlex and all additional components should also be read.
To obtain practice in operating the plant, it is absolutely essential to start
the operation according to the operating instructions. Later on, they also
serve as a useful aid in the event of possible malfunctions or uncertainty
and make many inquiries unnecessary. For this reason, the operating
manual must always be available at the plant.
Should difficulties arise, however, your Gema service center is always
ready to assist.
Inspection
Before switching on the booth, check the following points (where applica-
ble):
–
No foreign material in the central suction unit in the booth and in the
powder suction
–
Pneumatic conduction and powder hose are connected to the dense
phase conveyor
–
Pneumatic conduction to the After Filter is connected, the filter ele-
ment door is closed, the waste container is placed and fitted
Entering the booth
ATTENTION:
Danger of slipping and/or injury!
Repairs
ATTENTION:
Carrying out of repairs is only permitted when the booth is switched
off, and must be done only by trained personnel!