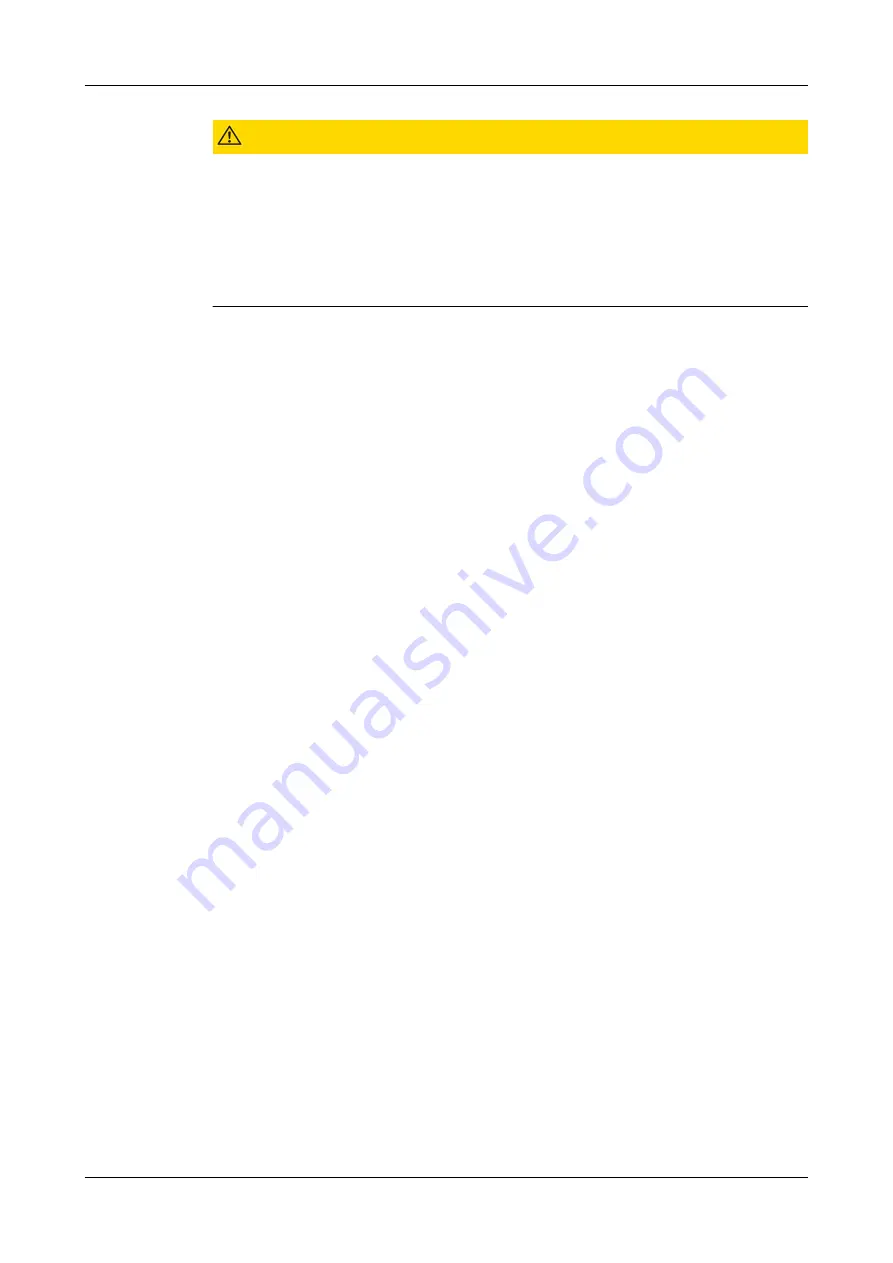
Caution!
If pipes contain liquids, these can spurt out when the pipes are
opened.
Danger of injury as a result of hot or aggressive liquids.
► Drain all pipe system elements that lead to the valve location and, if
necessary, clean or rinse them.
► Separate the pipe section in which the valve is to be fitted from the rest
of the piping system to prevent medium from entering again.
Carry out the following steps:
1.
Saw the pipe ends flat and square, deburr and degrease them.
2.
Prepare the component housing so that the component housing can be
welded into position free from stress and distortion.
3.
Prepare the welding procedure: use the 141 TIG (tungsten inert gas) welding
method with butt weld. I-joint according to DIN8532; hand or orbital weld.
4.
Connect the forming gas.
5.
Tack the component housing at several points distributed around the
circumference under forming gas (ensure forming gas supply).
!
Adjoining welding ends must not be separated by a gap. Otherwise the
corrosion resistance of the welded joint and the pipe will be reduced when
forming gas flows out.
6.
Weld the housing into the pipe system.
®
The valve has been welded in and installed.
6.3.2
Welding post-treatment
Interior
As long as forming and welding were carried out professionally, post-treatment of
the interior surfaces is not necessary.
Exterior area
Depending on the requirements, post-treatment in the exterior area consists of:
•
pickling,
•
grinding,
•
brushing,
•
polishing.
6.4
Pneumatic connections
6.4.1
Air Requirement
The air requirement depends on the type of actuator fitted. The following tables
show guideline values at an air pressure supply of 6 bar per valve size and the
corresponding actuator size used as a standard.
Assembly and installation
Pneumatic connections
430BAL012727EN_1
03.01.2018
25
Summary of Contents for Aseptomag GD
Page 65: ...Appendix 430BAL012727EN_1 03 01 2018 65...
Page 66: ......