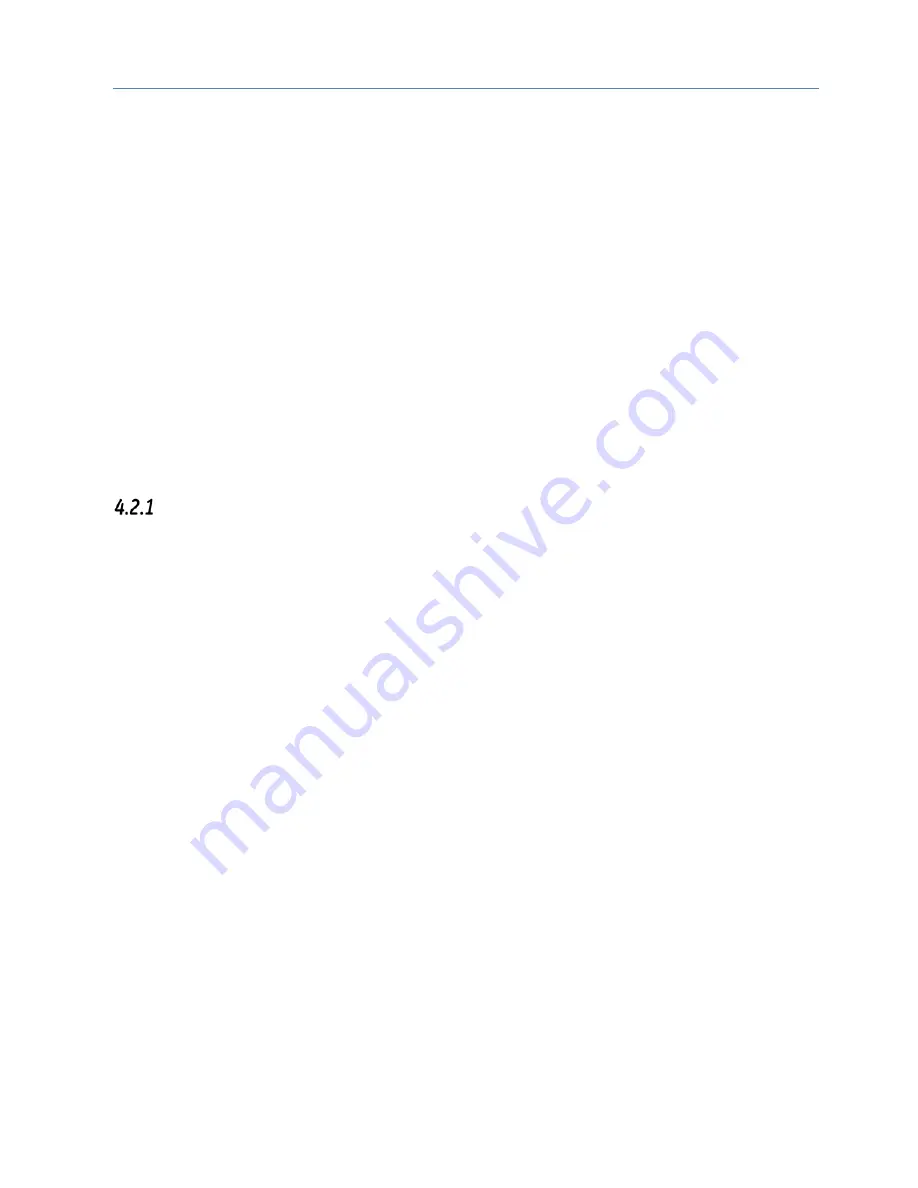
Chapter 4. Configuration
GFK-2224Q
January 2017
47
4.2
Rack-based and RX7i Embedded Interfaces
The configuration process for the rack-based and RX7i embedded Ethernet interfaces includes:
▪
Assigning a temporary IP address for initial network operation, such as connecting the programmer to
download the hardware configuration.
▪
Configuring the characteristics of the Ethernet interface.
▪
Configuring Ethernet Global Data (if used).
▪
(Optional, not required for most systems). Setting up the RS-232 port for Local Station Manager operation.
This is part of the basic Ethernet Interface configuration.
▪
(Optional, not required for most systems). Configuring advanced parameters. This requires creating a
separate ASCII parameter file that is stored to the PLC with the hardware configuration. The Ethernet
Interface has a set of default Advanced User Parameter values that should only be changed in exceptional
circumstances by experienced users. The Advanced User Parameters definitions and configuration are
described in Appendix A.
▪
(Optional) Setting up the PLC for Modbus/TCP Server operation. See Chapter 8 for information about
configuring Modbus/TCP Server operation.
This chapter discusses only the configuration of the PACSystems Ethernet Interface. Information about overall
system configuration is available in other PACSystems documentation and in the Logic Developer online help.
Ethernet Configuration Data
The PACSystems PLC is configured exclusively by the Machine Edition PLC Logic Developer-PLC programmer.
The Programmer can be connected over the Ethernet network. For initial programmer connection, an initial IP
address must be manually assigned to the Ethernet interface as described next in this chapter. The
PACSystems PLC does not support auto-configuration.
Generating / Storing / Loading the Configuration
The PACSystems Ethernet interfaces use several types of configuration data: Ethernet Configuration, optional
Ethernet Global Data Configuration, and optional Advanced User Parameter (AUP) Configuration. These
configuration parameters are generated at the programmer, stored from the programmer to the PLC CPU as
part of the hardware configuration Store sequence and may be loaded from the PLC CPU into the programmer
as part of the Configuration Load sequence. The optional AUP file must be manually generated with a text
editor and then imported into the programmer. The programmer then stores any AUP files to the PLC within the
Configuration Store operation. Once stored to the PLC, the PACSystems main CPU maintains the configuration
data over power cycles.
Backup Configuration Data
The PACSystems Ethernet interface saves a backup copy of the most recent Ethernet Configuration and AUP
Configuration in non-volatile memory for use when the PLC is cleared. (Ethernet Global Data configuration is
maintained only in the PLC CPU.) The PACSystems Ethernet interfaces maintain the backup configuration data
in nonvolatile memory without battery power. (A PLC Configuration Clear does not affect the backup
configuration data in the Ethernet interface.)
When the PLC configuration was not stored from the programmer, the Ethernet interface uses its backup
configuration data if valid. If that data is invalid or has never been configured, factory default configuration
values are used.
Locally Edited Configuration Data
If the PLC configuration was not stored from the programmer, the CHSOSW and CHPARM Station Manager
commands can be used to locally edit Ethernet configuration or AUP configuration data. These Station
Manager commands are not active if the PLC configuration has been stored from the programmer.
Summary of Contents for PACSystems RX7i
Page 45: ......
Page 80: ...Chapter 4 Configuration GFK 2224Q January 2017 67 ...
Page 81: ......
Page 122: ...Chapter 6 Programming EGD Commands GFK 2224Q January 2017 109 ...
Page 147: ......
Page 211: ......
Page 262: ...Chapter 13 Network Administration GFK 2224Q January 2017 249 ...
Page 263: ......