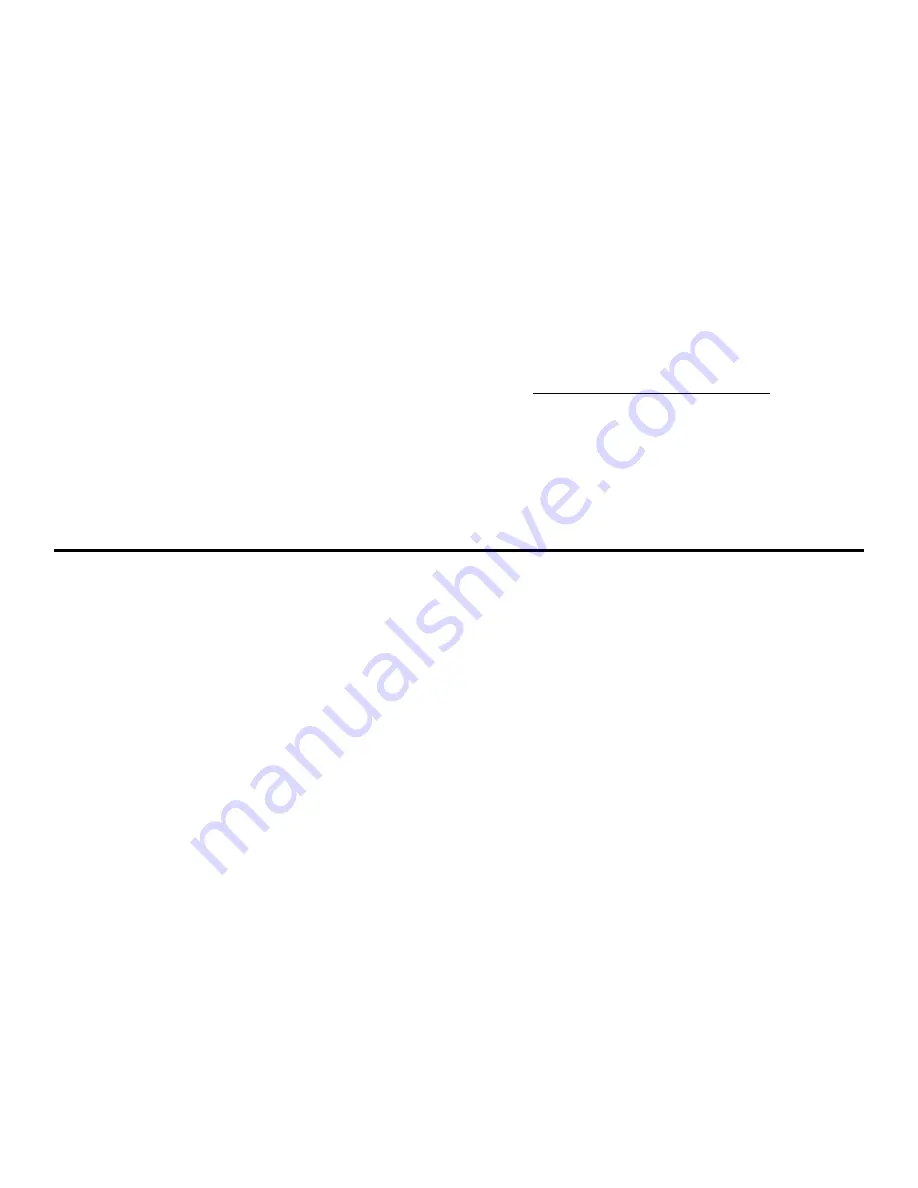
Appendix D. Upgrading the DMS 2/DMS 2E Instrument
Page 204
DMS 2 Operating Manual
The DMS 2 and DMS 2E operating software can be upgraded
using an internet connection and an upgrade utility program.
Each instrument is shipped with a CD containing the DMS 2/
DMS 2E Upgrade Utility Program.
Step 1:
Install the Upgrade Utility Program on your Internet
connected PC.
Step 2:
Run the program by clicking on the program icon,
located on your Program Menu. (Click the START button,
select PROGRAMS, and select DMS 2 Upgrade Utility.)
Step 3:
Select the Download New File button.
The program will connect to the GE Inspection Technologies,
FTP site (you may need to be connected to the Internet prior
to this operation). The program checks the version you have
on your machine against the version that is on the FTP site.
If the version on the FTP site is newer, it will download the
DMS 2 operation code. If they are the same, it will not
download the program, but exit the download routine.
Step 4
: Turn off the DMS 2 and connect it to the PC.
Step 5:
Click on the Upgrade the instrument button.
Step 6:
WHEN PROMPTED, press and hold the CENTER
UP KEY and the ON key for 3 seconds. The DMS 2 will go
into the re-programming mode. When finished, the DMS 2
will automatically shut off.
Step 7:
Perform a software re-set to clean out the instrument
memory (All stored Data Recorder and Parameter Files will be
lost!!!).
Information available on the GE Inspection Technologies,
web site. www.GEInspectionTechnologies.com
•
Up to date information on operating software
•
Latest upgrade utility program
•
Specifications
•
New features
Appendix D: Upgrading the DMS 2/DMS 2E Instrument