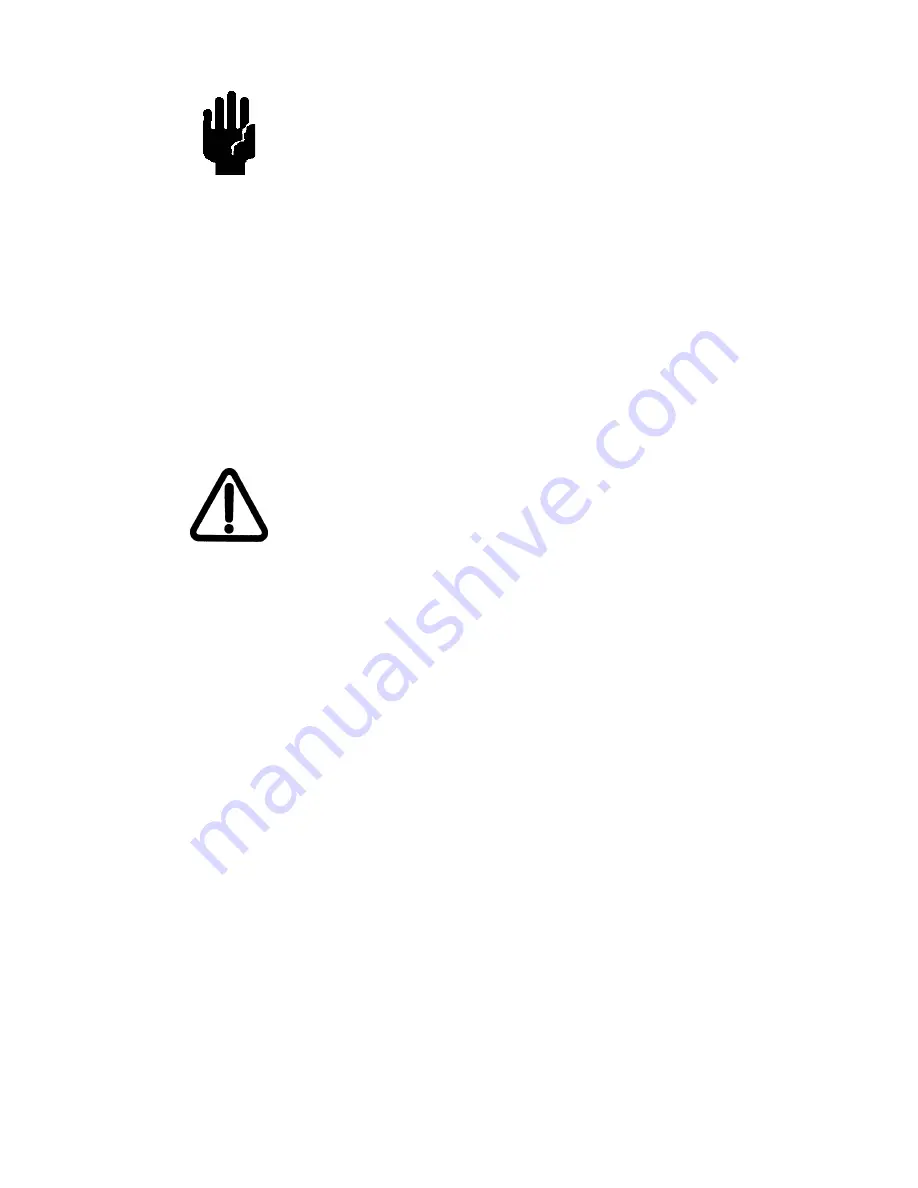
© 2015 General Electric Company. All rights reserved
.
32 |
=
GE Oil & Gas
CAUTION
Do not use an excessive amount, as it will not set and may
migrate into the instrument.
The pneumatic input signal ranges are 3-15 psig (20-100 kPa or
207- 1034 mbar), 6-30 psig (40-200 kPa or 414-2068 mbar), and
3-27 psig (20-180 kPa or 207-1862 mbar). Split ranges are
available.
Positioners with 24 psig signal span (i.e., 6-30 psig and 3-27 psig)
require a different diaphragm assembly as shown in Figure 19 on
page 68.
Maximum allowable air supply pressure to the positioner varies
according to actuator, valve size, and type. See pressure drop
tables in valve catalog to determine correct positioner supply
pressure.
WARNING
Never exceed actuator or positioner maximum supply pressure.
Damage to equipment or injury to personnel may result.
Summary of Contents for Masoneilan 4700E
Page 4: ...This page intentionally left blank ...
Page 8: ...This page intentionally left blank ...
Page 10: ...This page intentionally left blank ...
Page 14: ...This page intentionally left blank ...
Page 18: ...This page intentionally left blank ...
Page 40: ... 2015 General Electric Company All rights reserved 40 GE Oil Gas Figure 13 FM Installation ...
Page 42: ... 2015 General Electric Company All rights reserved 42 GE Oil Gas Figure 15 ATEX Installation ...
Page 46: ...This page intentionally left blank ...
Page 66: ... 2015 General Electric Company All rights reserved 66 GE Oil Gas ...
Page 78: ...This page intentionally left blank ...
Page 79: ......