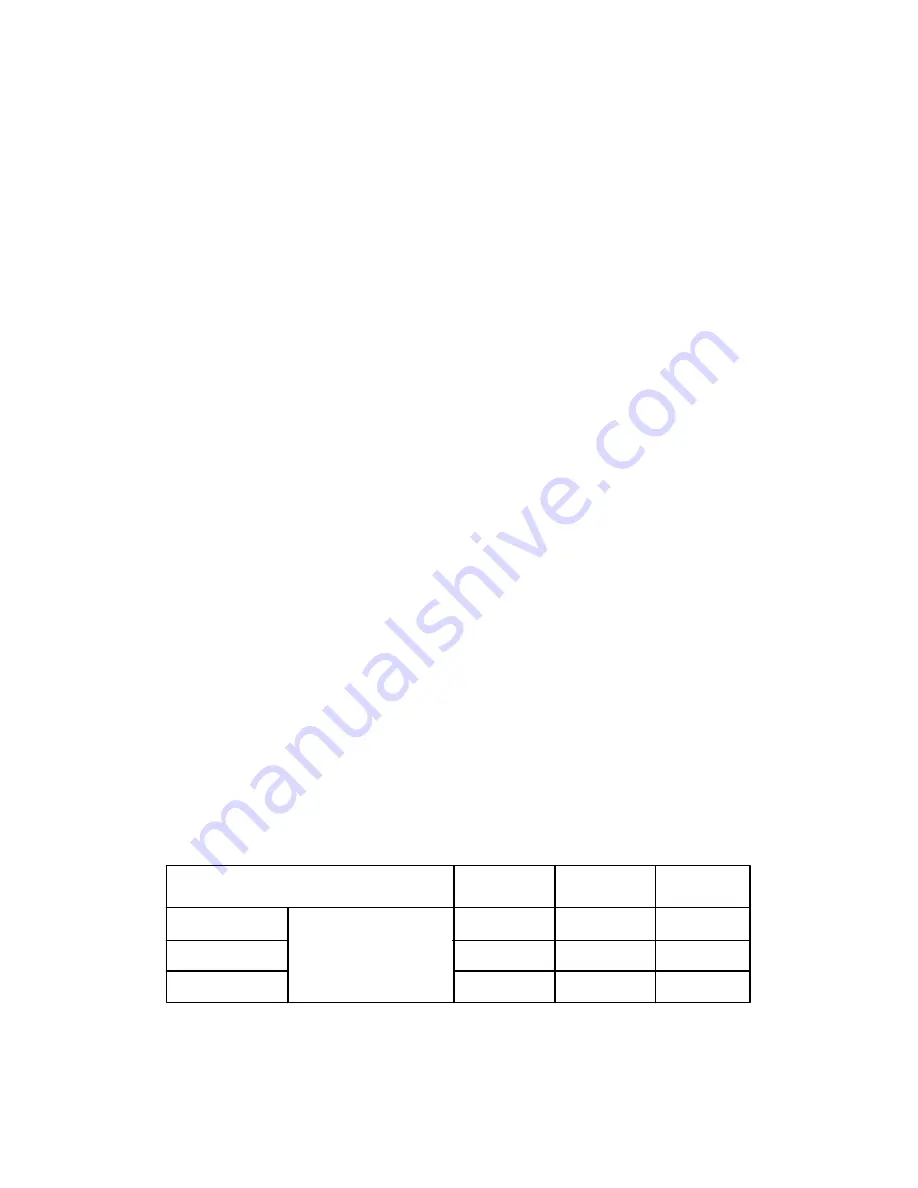
13–10–613 SP Page 50
13. Install original oil return by slipping tube through
the fitting at the discharge manifold flange until
ferrule bottoms in the fitting. If a new fitting and
return tube are used, slip the tube through the
fitting until it touches the bottom of the separator,
then raise the tube about 1/4 inch off the bottom
and tighten the fitting nut securely. Connect the
other end of the tube to the compressor oil return
tube elbow. Do not bend tube or raise tube further
than 1/4”–1/2” from the bottom of the separator.
14. Reconnect compressor oil return tube to tube
elbow.
COMPRESSOR OIL SYSTEM CHECK – The com-
pressor should be at operating temperature at the time
of the checks. On–half hour of loaded operation is usu-
ally sufficient to reach level–out operating tempera-
tures. The data shown below is for an oil–system in
good condition.
If the unit will operate at discharge temperatures over
200
_
F for more than 4 consecutive hours, refer to the
“High Temperature Operation” paragraph and select a
lubricant for this service. Regardless of level of
sustained discharge temperature, the high discharge
air temperature switch must never be set higher than
225
_
F shutdown temperature.
Air and Oil Discharge Temperature – Check with a
thermometer in the tapped opening on top of the com-
pressor discharge pipe to the oil reservoir.
For Air Cooled Oil Systems, FIGURE 5–10 shows
the normal upper limit of discharge temperatures for
varying ambient temperatures beginning at the system
design point of 80
_
F. At ambient temperatures below
80
_
F, the mixing valve will hold the discharge tempera-
ture at the 80
_
F ambient temperature point. Above
80
_
F, the oil cooler is fully used and the discharge tem-
perature varies degree for degree with the ambient
temperature.
For Water Cooled Oil Systems, the water flows at var-
ious temperatures outlined in Section 2 will hold the dis-
charge temperature below the 80
_
F ambient tempera-
ture level of FIGURE 5–10. Small variations in specific
water flows or temperatures will not be noted in the dis-
charge temperature since the water control valve will
tend to hold a constant oil temperature. A significant
change in the discharge temperature is cause to check
for a change in water flow or temperature.
Oil Inlet Pressure – Check at the fitting in the line near
the compressor oil inlet. With air receiver pressure at
100 psi, oil inlet pressure should be 75–85 psig.
Oil Cooler Oil Pressure Differential (Air–Cooled
Radiator) – 2 to 25 psi (65 to 150 PSIG Receiver Pres-
sure) – Check at the fitting in the inlet and outlet lines
of the oil cooler.
Oil Cooler Oil Pressure Differential (Water–Cooled
Heat Exchanger) – 2 to 25 PSI (65 to 150 PSIG Re-
ceiver Pressure) – Check at the heat exchanger oil inlet
and outlet fittings.
Oil Cooler Temperature Differential (Air–Cooled
Radiator) – The oil temperature differential depends
on the temperature of the air at the oil cooler fan and
cleanliness of core faces. As ambient temperatures
and core restrictions increase, the oil cooler outlet tem-
perature will increase. The inlet oil temperature may be
checked at the fittings in the oil inlet line on the oil cooler
module. The outlet oil temperature may be checked at
the fitting in the oil outlet line.
Oil Cooler Temperature Differential (Water–Cooled
Heat Exchanger) – The oil temperature differential de-
pends on the inlet water temperature and the water flow
rate permitted by the water flow control valve setting.
The oil inlet temperature is approximately the same as
the air discharge temperature – see the gauge on the
instrument panel. The oil outlet temperature may be
checked at the compressor oil inlet line fitting.
Oil Cooler Water Pressure Differential (Water–
Cooled Heat Exchanger) – The water pressure differ-
ential through the heat exchanger will depend on the
supply pressure, flow rate, cooler tube cleanliness and
outlet pressure. The inlet and outlet water pressure
may be checked at the pipe fittings supplied by the
customer.
FIGURE 5–10 – AMBIENT TEMPERATURES
Ambient Temperature (
_
F.)
80
90
100
350 HP
Discharge
171
181
191
400 HP
Temperature
175
185
195
500 HP
_
F
184
194
204*
* For temperatures above 200 F see “High Temperature Operation”.
Summary of Contents for ELECTRA-SAVER EAYQ E
Page 15: ...13 10 613 SP Page 6 DECALS 206EAQ077 212EAQ077 218EAQ077 211EAQ077 207EAQ077 ...
Page 16: ...13 10 613 SP Page 7 DECALS 216EAQ077 217EAQ077 222EAQ077 221EAQ077 208EAQ077 ...
Page 31: ...13 10 613 SP Page 22 FIGURE 4 2 FLOW CHART FOR SET UP PROGRAMMING ...
Page 48: ...13 10 613 SP Page 39 FIGURE 4 13 WIRING DIAGRAM 202EAY546 Ref Drawing ...
Page 75: ......