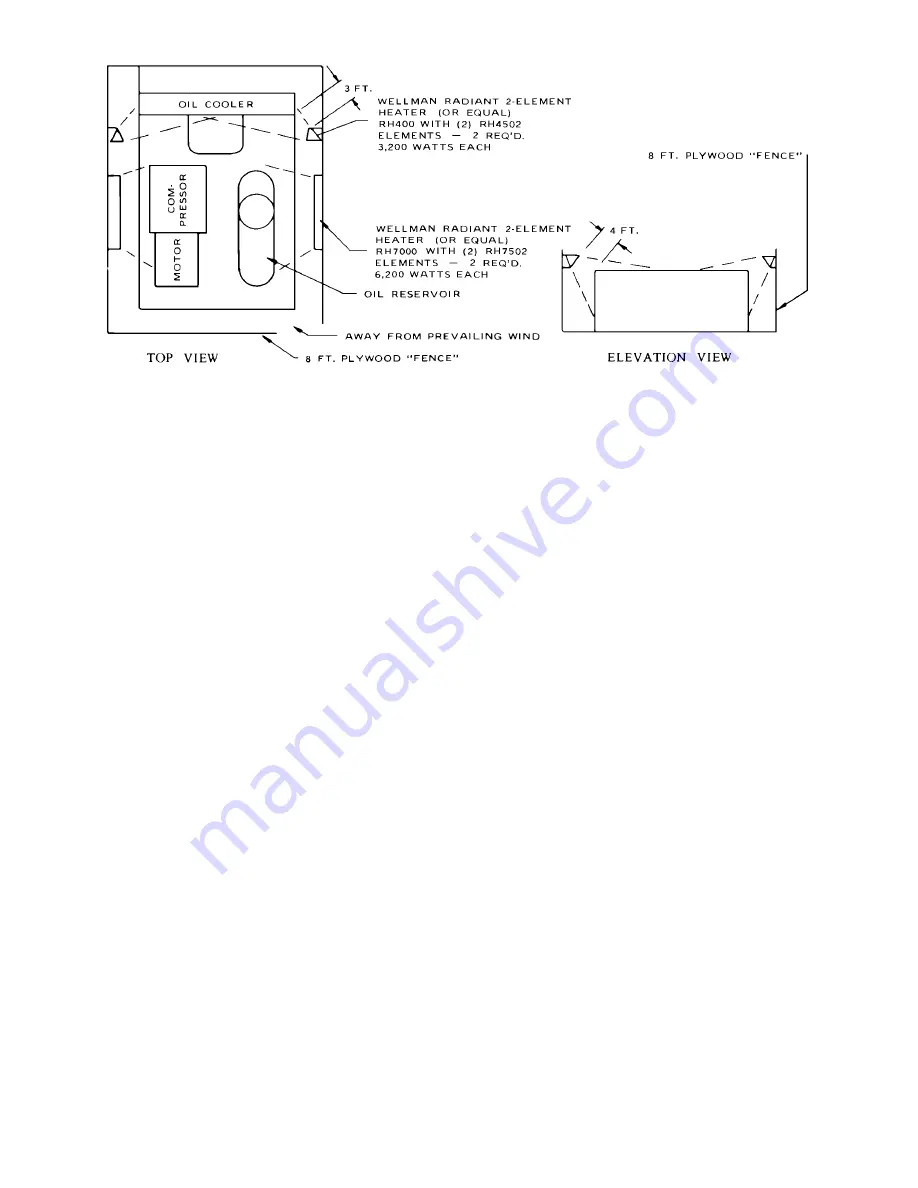
13–10–613 SP Page 11
FIGURE 2–5 – COLD WEATHER INSTALLATION
An oil filler stand pipe and plug must be located in the
piping on the oil cooler module for ease of filling of a re-
mote oil cooler, see FIGURE 5–4, page 45.
Oil Cooler – Installation – Inspect unit upon arrival.
In case of damage, report immediately to transporta-
tion company. Before installation, check rating plate on
motor to verify that power input and motor specification
requirements match available electric power at point of
installation.
1.
Set the unit level on a firm, solid foundation. The
larger oil cooler models have lifting holes to facili-
tate unit hoisting.
2.
Allow for linear expansion and contraction of pip-
ing in the direction away from the oil cooler. Use
flexible connectors or suitable expansion joints on
all oil cooler inlet and outlet piping. See
FIGURE 2–3, page 9, for typical schematics.
3.
Select properly tensioned and aligned piping sup-
port clamps or hangers and position them to re-
lieve any piping stress at the oil cooler inlet and
outlet ports. Do not support from flexible connec-
tors.
4.
Service – For continuous efficiency, oil cooler
cores must be periodically cleaned with either
vacuum or compressed air. If wet cleaning is re-
quired, shield motor and spray on a mild soap
solution and flush with clear water.
AUXILIARY AIR RECEIVER – The unit requires an
auxiliary air receiver unless the piping system is large
and provides sufficient storage capacity to prevent rap-
id cycling. When used, an air receiver should be of ade-
quate size, provided with a relief valve of proper setting,
a pressure gauge, and a means of draining conden-
sate.
AFTERCOOLER (FIGURE 1–2 and FIGURE 1–5,
pages 2 and 3) – An aftercooler will provide control of
moisture entering the shop air lines while reducing the
normal low discharge temperature of about 180
_
F at
100 PSIG discharge pressure to near inlet air tempera-
ture, or cooling water temperature.
Air–Cooled Machines – When an aftercooler is fur-
nished on an air–cooled machine, the aftercooler is
installed on the oil cooler module between the fan and
the oil cooler. The moisture separator is furnished by
Gardner Denver but must be mounted by the customer
between the aftercooler and the auxiliary air receiver
with a condensate drain provided at the bottom. All air
piping from the compressor discharge to aftercooler to
auxiliary air receiver is to be furnished and mounted by
customer. The design of the aftercooler piping
must be approved by the factory before installa-
tion. Design information to be submitted for approval
includes:
1.
Location of aftercooler module – inside or out-
doors.
2.
Range of operating ambient temperatures at the
aftercooler location.
3.
Pipe type and size(s) to be used to connect the af-
tercooler, separator, and compressor unit – mini-
mum pipe size is 5” NPT.
4.
Lengths of the pipe run. If more than one pipe size
is used, list length of each size and total length.
5.
Number and size of elbows, tees, unions, reduc-
ers, and valves to be used in the pipe run.
6.
A dimensional sketch of the proposed piping sys-
tem showing location of the compressor unit, af-
tercooler, separator and auxiliary air receiver, pipe
and fittings illustrating design information included
in numbers 3 through 5 above.
Summary of Contents for ELECTRA-SAVER EAYQ E
Page 15: ...13 10 613 SP Page 6 DECALS 206EAQ077 212EAQ077 218EAQ077 211EAQ077 207EAQ077 ...
Page 16: ...13 10 613 SP Page 7 DECALS 216EAQ077 217EAQ077 222EAQ077 221EAQ077 208EAQ077 ...
Page 31: ...13 10 613 SP Page 22 FIGURE 4 2 FLOW CHART FOR SET UP PROGRAMMING ...
Page 48: ...13 10 613 SP Page 39 FIGURE 4 13 WIRING DIAGRAM 202EAY546 Ref Drawing ...
Page 75: ......