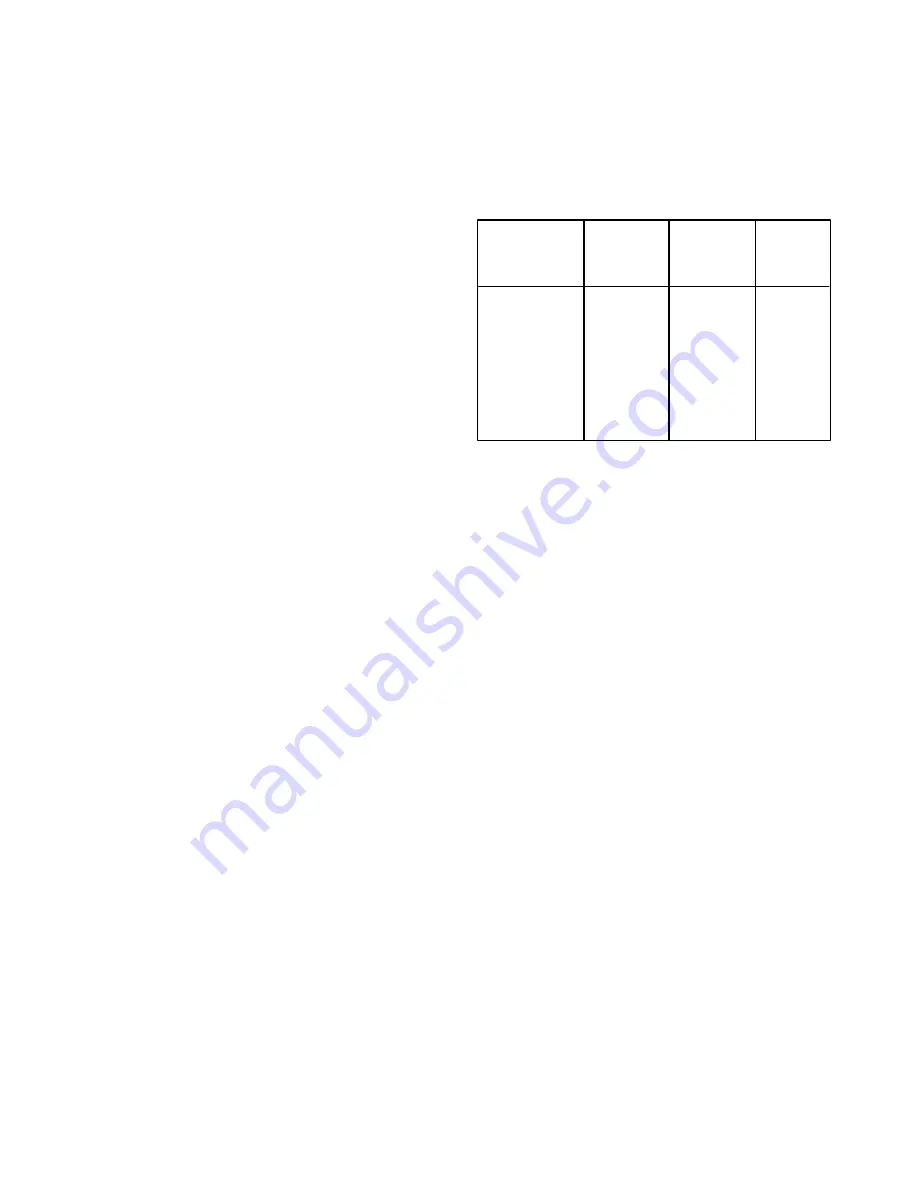
13–10–613 SP Page 35
fer to the transformer label for connection prior to ener-
gizing. Two primary and one secondary fuse are pro-
vided. Refer to adjacent labeling for replacement
information.
Terminal Strip – This provides connections for all
110–120 volt devices not contained within the enclo-
sure.
Fan Starter – The starter is used to provide control
and overload protection for the cooling fan or the ven-
tilation fan of water–cooled units with enclosure. Over-
load heaters should be selected and adjusted based on
the motor nameplate amps and the instructions located
inside the cover of the electrical enclosure. Three
fuses are provided. Refer to adjacent labeling for re-
placement information.
Main Starter – This starter is used to provide control
and overload protection for the main drive motor. Full
voltage starters employ a single contactor, overload
heaters should be selected and adjusted based on the
motor nameplate amps and the instructions located in-
side the cover of the enclosure. Wye–delta starters
employ three contactors which are controlled sequen-
tially to provide low current starting. For wye–delta
starters, the motor nameplate amps must be first multi-
plied by 0.577 before using the heater table.
COMPRESSOR CAPACITY CONTROL – TURN
VALVE UNITS ONLY
The capacity of the compressor is controlled by the ac-
tion of the Turn Valve and the Compressor Inlet Valve.
The turn valve controls compressor delivery to match
demands of 40% to 100% of the compressor’s maxi-
mum capacity. The inlet valve throttles to control com-
pressor delivery to match demands of 0% to 40% of the
compressors maximum capacity.
Example with normal setting of 100 PSIG:
Discharge
Compressor
Manifold
Delivery
Inlet Valve
Turn Valve
Pressure
Full Capacity
Open
Closed
100
70% Capacity
Open
50% Open
100
40% Capacity
Open
Full Open
100
30% Capacity
Closing
Full Open
103
20% Capacity
Closing
Full Open
103
0% Capacity
Closed
Full Open
103
CONTROL SCHEMATICS – FIGURE 4–10 through
FIGURE 4–12, pages 36 through 38, illustrate valve
positions during common operating conditions.
WIRING DIAGRAMS – FIGURE 4–13, page 39, illus-
trates the most common package configuration. If cur-
rent monitoring is not installed, there is no connection
to connector CN–4 on the controller. Refer to the wiring
diagram furnished with the compressor package for
specific connections and wiring.
Summary of Contents for ELECTRA-SAVER EAYQ E
Page 15: ...13 10 613 SP Page 6 DECALS 206EAQ077 212EAQ077 218EAQ077 211EAQ077 207EAQ077 ...
Page 16: ...13 10 613 SP Page 7 DECALS 216EAQ077 217EAQ077 222EAQ077 221EAQ077 208EAQ077 ...
Page 31: ...13 10 613 SP Page 22 FIGURE 4 2 FLOW CHART FOR SET UP PROGRAMMING ...
Page 48: ...13 10 613 SP Page 39 FIGURE 4 13 WIRING DIAGRAM 202EAY546 Ref Drawing ...
Page 75: ......