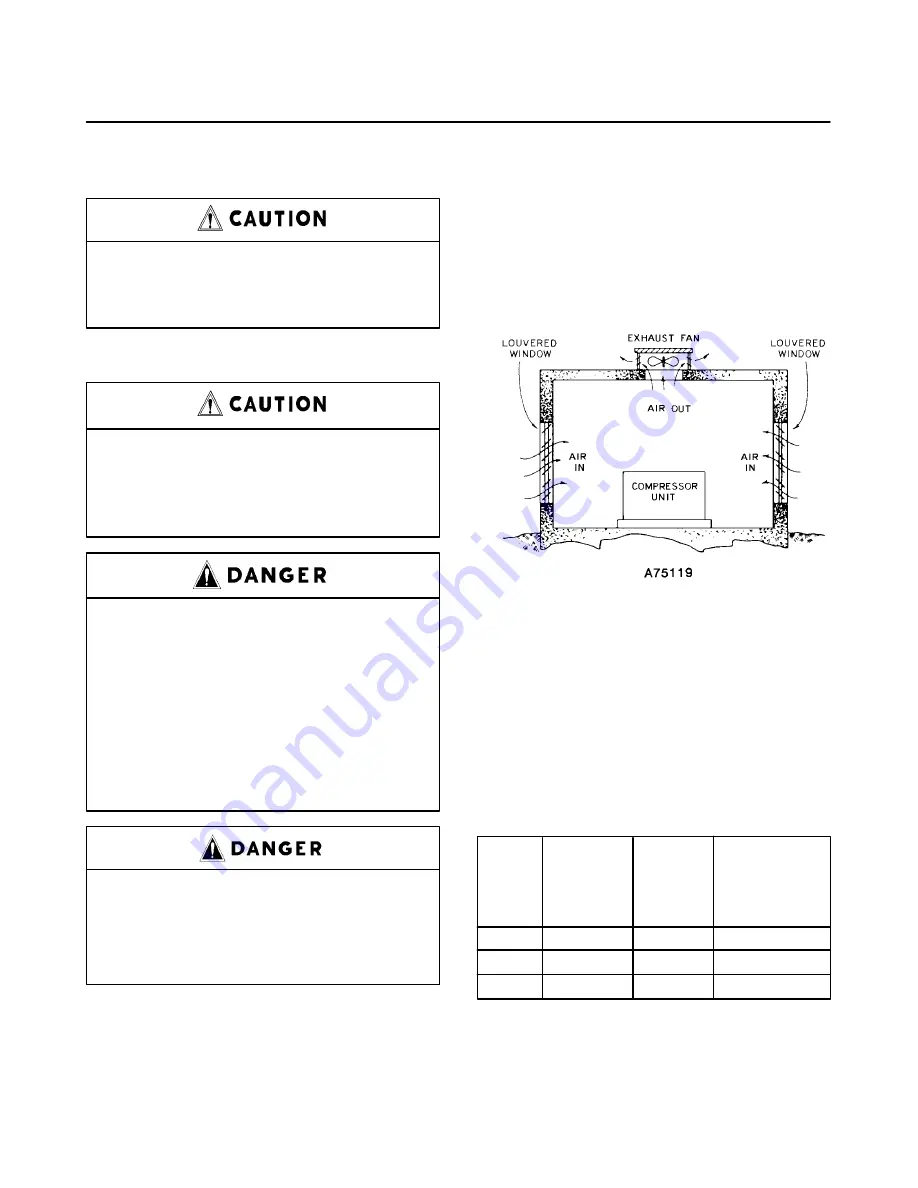
13–10–613 SP Page 8
SECTION 2
INSTALLATION
GENERAL – On receipt of the unit, check for any dam-
age that may have been incurred during transit. Report
any damage or missing parts as soon as possible.
Do not electric weld on the compres-
sor or base; bearings can be damaged
by passage of current.
LIFTING UNIT:
Lift compressor unit by base only. Do
not use other places such as motor,
compressor or discharge manifold
piping as lifting points.
The eyebolts or lugs provided on the
motor are for lifting the motor only
and should not be used to lift any
additional weight. All eyebolts must
be securely tightened. When lifting
the motor the lifting angle must not
exceed 15 degrees. Failure to observe
this warning may result in damage to
equipment or personal injury.
Compressor, air/oil reservoir, separa-
tion chamber and all piping and tub-
ing may be at high temperature during
and after operation.
LOCATION – The compressor should be installed in a
clean, well–lighted, well–ventilated area with ample
space all around for maintenance. Select a location
that provides a cool, clean, dry source of air. In some
cases it may be necessary to install the air filter at some
distance from the compressor to obtain proper air sup-
ply.
The compressor unit require electric motor cooling air
as well as air to the compressor inlet. Proper ventilation
MUST be provided (FIGURE 2–2); hot air must be ex-
hausted from the compressor operating area. A typical
inlet–outlet air flow arrangement is shown in
FIGURE 2–1.
FIGURE 2–1 – TYPICAL COMPRESSOR ROOM
If the air–cooled oil cooler module is to be installed at
a location remote from the compressor unit, be sure
that adequate ventilation is provided, FIGURE 2–2.
Hot air must be exhausted from the oil cooler area.
Do not block the air flow to and from the unit. Allow
3–1/2 feet to the nearest obstruction on the control box
side of the unit and 3 feet on all other sides.
Open Unit With
Aftercooler
Aftercooler & Oil
Open
and
Cooler Module
Compressor
Oil Cooler
Discharge in
Size
Unit
Module
Same Room
350 HP
12,600
43,000
55,600
400 HP
14,400
43,000
57,400
500 HP
18,000
43,000
61,000
* 80
_
F Inlet Air
FIGURE 2–2 – AIR FLOW CHART
Summary of Contents for ELECTRA-SAVER EAYQ E
Page 15: ...13 10 613 SP Page 6 DECALS 206EAQ077 212EAQ077 218EAQ077 211EAQ077 207EAQ077 ...
Page 16: ...13 10 613 SP Page 7 DECALS 216EAQ077 217EAQ077 222EAQ077 221EAQ077 208EAQ077 ...
Page 31: ...13 10 613 SP Page 22 FIGURE 4 2 FLOW CHART FOR SET UP PROGRAMMING ...
Page 48: ...13 10 613 SP Page 39 FIGURE 4 13 WIRING DIAGRAM 202EAY546 Ref Drawing ...
Page 75: ......