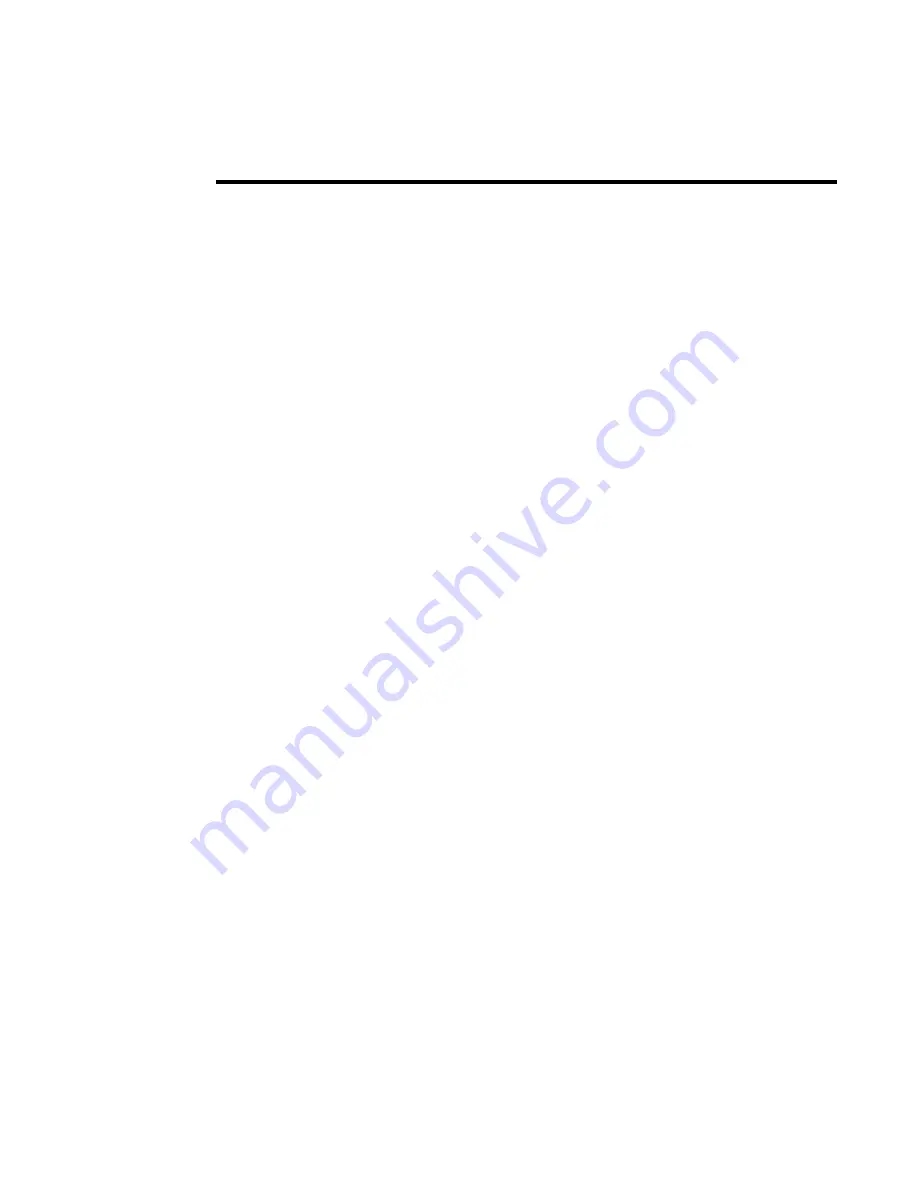
USER MANUAL
DMC-40x0
Manual Rev. 1.0f
By Galil Motion Control, Inc.
Galil Motion Control, Inc.
270 Technology Way
Rocklin, California 95765
Phone: (916) 626-0101
Fax: (916) 626-0102
E-mail Address: [email protected]
URL: www.galilmc.com
Rev 8/09
Summary of Contents for DMC-4040
Page 54: ...Chapter 3 Connecting Hardware 45 DMC 40x0 User Manual...
Page 55: ...DMC 40x0 User Manual Chapter 3 Connecting Hardware 46...
Page 56: ...Chapter 3 Connecting Hardware 47 DMC 40x0 User Manual...
Page 73: ...Figure 4 1 GalilTools DMC 40x0 User Manual Chapter 4 Software Tools and Communication 64...
Page 185: ...THIS PAGE LEFT BLANK INTENTIONALLY DMC 40x0 User Manual Chapter 7 Application Programming 176...
Page 205: ...THIS PAGE LEFT BLANK INTENTIONALLY DMC 40x0 User Manual Chapter 10 Theory of Operation 196...
Page 222: ...Step 2 Remove ICM s Appendices 213 DMC 40x0 User Manual...
Page 232: ...DMC 4080 Steps 4 and 5 Step 4 Replace ICM s Appendices 223 DMC 40x0 User Manual...