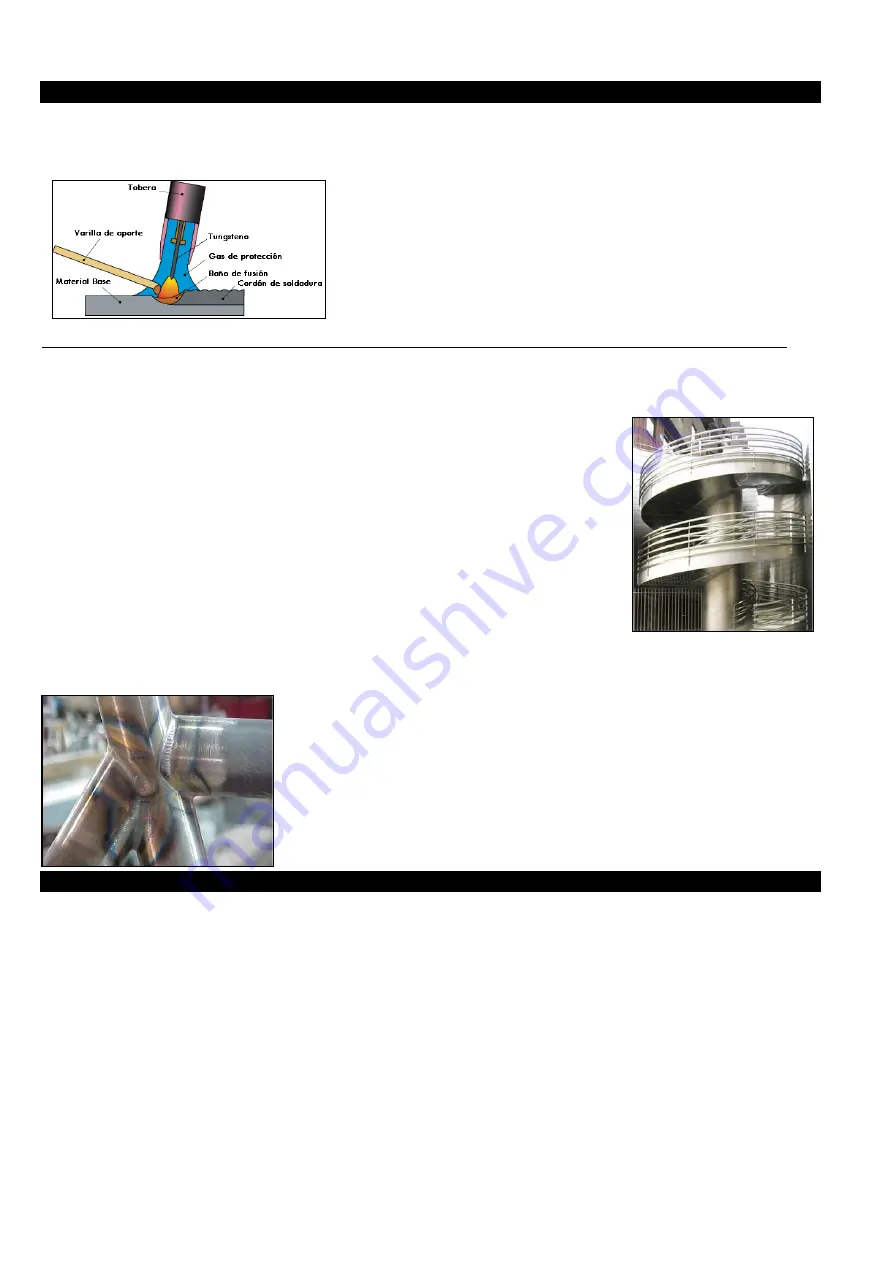
TIG 3200 AC/DC
22
5. WELDING TIG.
Welding with tungsten electrode or wolfram electrode, also known as TIG (Tungsten Inert Gas), GTAW or process 141,
take part of the arc welding processes. Therefore, we must bear in mind the fundamental principles of the process
before beginning the requested welding work.
In the TIG process, the electric arc is established between the part to be
welded and a non-consumable electrode. While, air ionization and pro-
tection against contamination will be performed by atmosphere gaseous
flowing through the torch..
The way of the current will generate the necessary heat for the fusion of
the materials to be welded.
APPLICATIONS
This equipment can be used for welding all kinds of materials. It is not economical to apply to thicker than 10mm. For
higher ranges we must use other combined processes for fill passes.
A great advantage for this welding method is, basically, to obtain more resistant and
ductile cords, while being less sensitive to corrosion than other procedures, since the pro-
tective gas prevents the contact between the atmosphere and the fusion bath.
Reduction of slag deformations or inclusions , besides cleaner and uniform welds due
less fumes and projections are other advantages of this process.
The cord obtained therefore a good surface finish, which it can be improved with simple
finishing operations, which it has a favorable impact over production costs.
As disadvantages; the need to provide a continuous gas flow and the cost involved. Be-
sides, this method of welding requiring a very specialized workforce, which it increases
costs also. Therefore, it is not one of the most used methods, but it is reserved for joints
with special needs of surface finish and precision.
In order to obtain a greater control over the welding, pulsed current can be used.
The result of it is a succession of points that overlap as cord, guaranteeing on each
impulse the penetration and partial solidification of it.
This process is adapted for all those applications in which we must limit the thermal
contribution, either by thickness, deformation or metallurgical transformations.
It is especially recommended for welding pipes because it is less sensitive to varia-
tions in position.
5.1. TIG DC WELDING.
It is the most used form that allows weld most of materials (carbon steels, stainless steels, titanium, bronze, ...), except
aluminum and magnesium.
Connecting the torch to the negative pole allows limited electrode wear, because of most heat is concentrated on the
part being welded. The electrode diameter recommendation changes depending on the selected welding current.