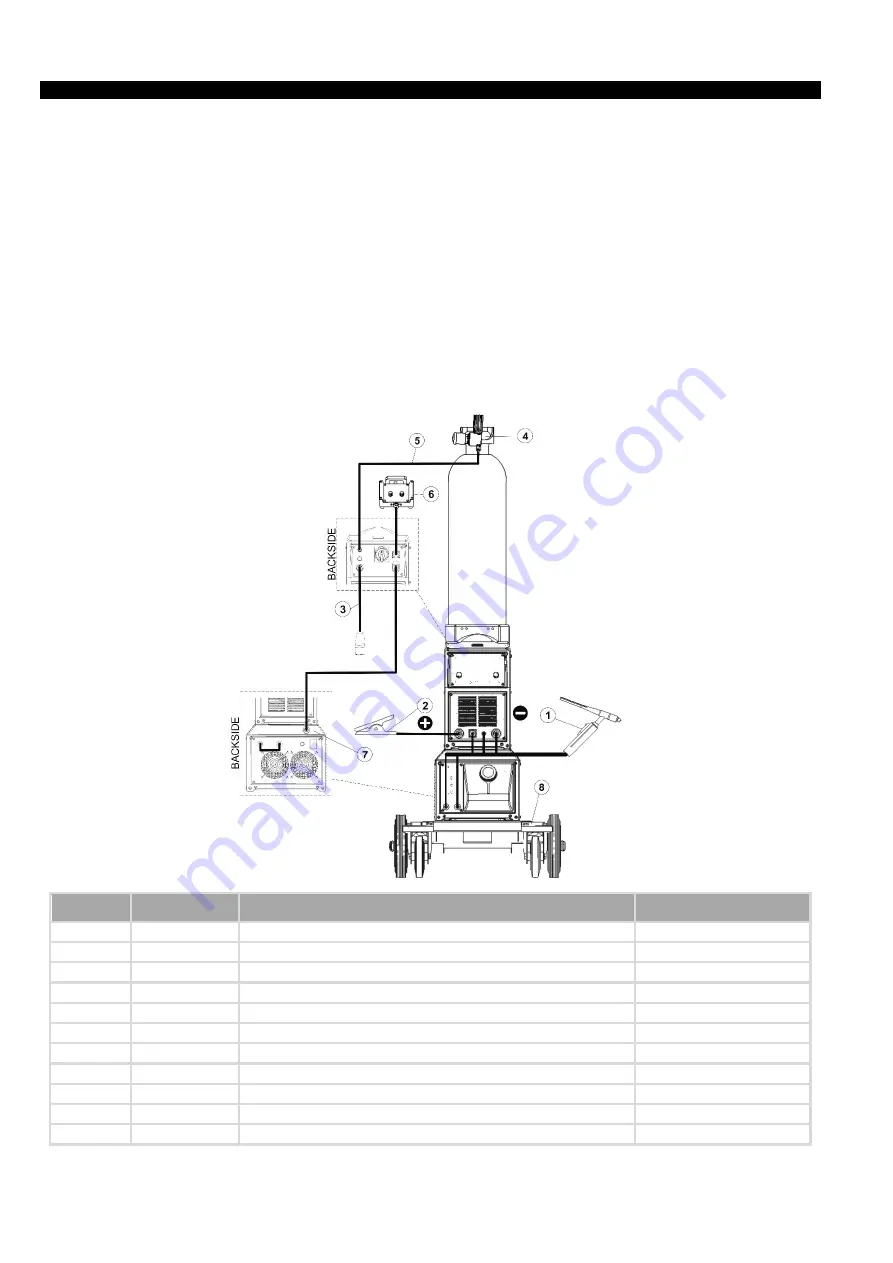
TIG 3200 AC/DC
10
3.2.2. TIG INSTALLATIONS WITH COOLING.
It is recommended to perform this type of configuration for in-process welding applications TIG DC above 200 amps
and TIG AC at any intensity range.
To all welding processes TIG, alternating current welding including, we recommend connecting the torch
to negative
terminal B2 and the grounding
to positive B1. Additionally we will connect the gas fitting of the torch to the gas outlet
of the machine G2 and the torch switching connector to the panel connector CN2
(Torch Control)
. We will connect the
torch cooling, cold inlet and hot outlet (Blue/Red), to the cooling module
.
We will connect the power supply of the cooling module to the connector of the fairing kit
and this one to the connector
J located at the rear of the machine.
We will install the pressure reducer
to the gas bottle and connect the gas pipe
to the pressure reducer and to the
quick plug G1 located at the rear of the machine.
Optionally we can install a remote control
to the connector CN1
(Telenet)
located at the rear of the machine.
We plug the power input cable
(A)
to the electric-net and we will be ready to work.
MARK
REFERENCE
DESCRIPTION
OBSERVATIONS
1
19051814
Torch 5XT-18 4m
Optional
1.1
63716017
Male straight air connector 9v
Included as standard
1.2
47016065
Adapter fitting M-1/4” - Quick Plug (DN5)
Included as standard
2
43812219
Welding mass (35 mm2-4mt)
Included as standard
3
42312022
Input cable
Included as standard
4 (A)
37600000
Pressure reducer EN 2000 Argon
Option A
4 (B)
37900000
Pressure reducer GAS FREE (Saving gas up to 50%)
Option B recomended
5
42312030
Gas Pipe (2m/racor rápido)
Included as standard
6
42312058
Remote control. Universal Control.
Optional
7
47012090
Fairing kit (machine connection cable included)
Required
8
64184000
Transport car
Required