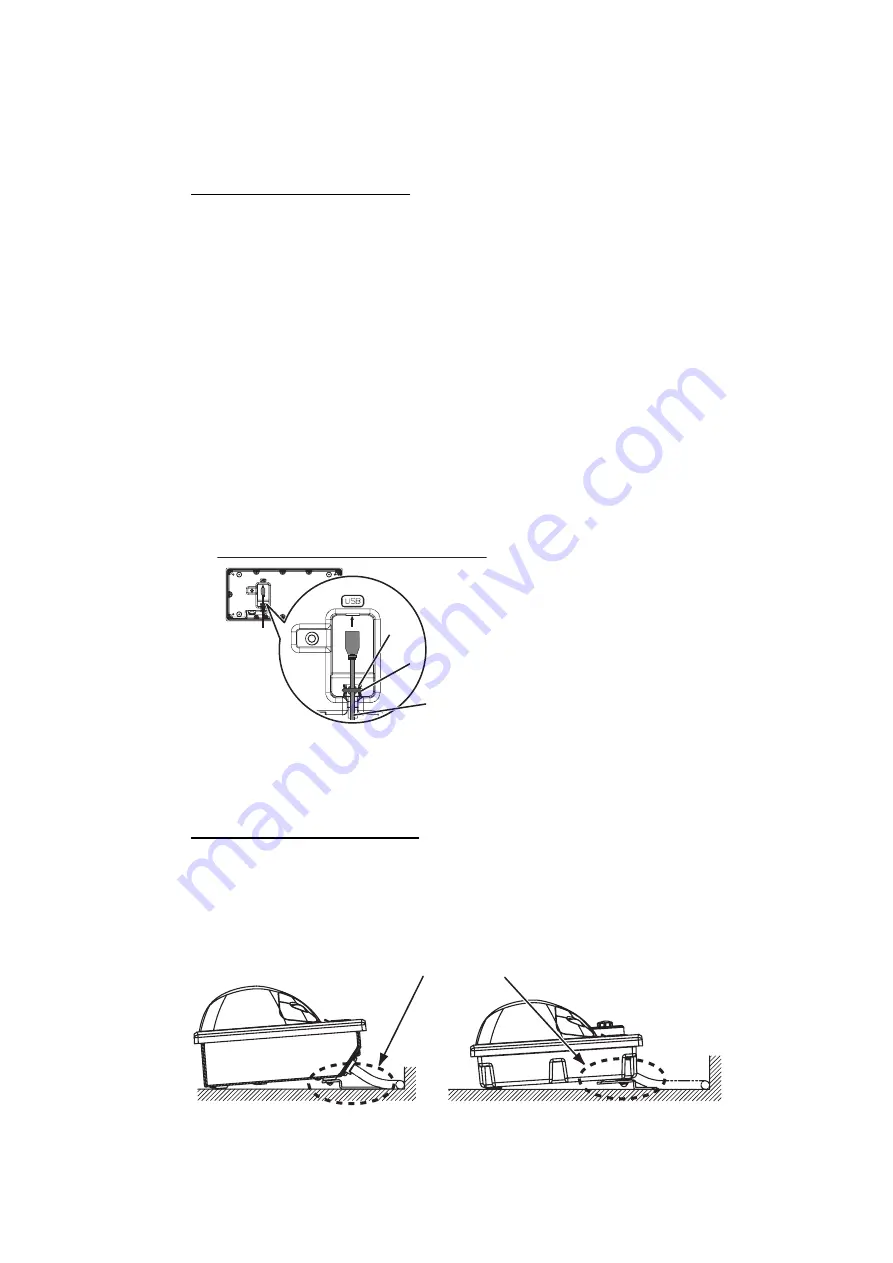
1. INSTALLATION
1-13
1.4
Radar Control Unit, Trackball Control Unit
The control units can be installed on a desktop or flush mounted in a console. For the
desktop installation the unit can laid flat or tilted.
Installation considerations
Keep in mind the following points when selecting a location.
• Select a location where the control unit can be operated easily.
• Locate the unit away from heat sources because of heat that can build up inside the
cabinet.
• Locate the equipment away from places subject to water splash and rain.
• Leave sufficient space at the sides and rear of the unit to facilitate maintenance.
• Determine the location considering the length of the signal cable between the con-
trol unit and the processor unit.
• A magnetic compass will be affected if the control unit is placed too close to the
magnetic compass. Observe the compass safe distances in the SAFETY IN-
STRUCTIONS to prevent interference to the compass.
• Be sure to connect the ground wire (between the earth terminal on the chassis and
the ship’s earth).
• Fasten the USB cable with the cable tie.
1.4.1
Desktop installation
How to mount the unit tilted
Use the desk fixing plate to mount the unit tilted.
1. Fix the desk fixing plate to the bottom of the control unit.
2. Fix the control unit with self-tapping screws (local supply).
Side view of control units
Ex. Radar control unit, bottom view RCU-025
USB cable
USB cable
Cable tie
Cable tie
Cable routing peg
Cable routing peg
Desk fixing plate
RCU-026
RCU-025
Summary of Contents for FAR-3230SW-BB
Page 14: ...EQUIPMENT LIST xii This page is intentionally left blank ...
Page 36: ...1 INSTALLATION 1 22 This page is intentionally left blank ...
Page 112: ...3 SETTINGS AND ADJUSTMENTS 3 12 This page is intentionally left blank ...
Page 142: ...D 1 12 Sep 2014 H MAKI ...
Page 143: ...D 2 12 Sep 2014 H MAKI ...
Page 144: ...20 Jan 2014 H MAKI D 3 ...
Page 145: ...4 Jul 2014 H MAKI D 4 ...
Page 146: ...2 Nov 2012 Y NISHIYAMA D 5 ...
Page 147: ...13 Feb 2014 H MAKI D 6 ...
Page 148: ...24 Mar 2014 H MAKI D 7 ...
Page 149: ...24 Mar 2014 H MAKI D 8 ...
Page 150: ...18 Jan 2014 H MAKI D 9 ...
Page 151: ...18 Jan 2014 H MAKI D 10 ...
Page 152: ...18 Jan 2014 H MAKI D 11 ...
Page 153: ...7 Nov 2012 Y NISHIYAMA D 12 ...
Page 154: ...7 Nov 2012 Y NISHIYAMA D 13 ...
Page 155: ...7 Nov 2012 Y NISHIYAMA D 14 ...
Page 156: ...D 15 24 May 2012 Y NISHIYAMA ...
Page 157: ...D 16 24 May 2012 Y NISHIYAMA ...
Page 158: ...D 17 24 May 2012 Y NISHIYAMA ...
Page 159: ...7 Nov 2012 Y NISHIYAMA D 18 ...
Page 160: ...7 Nov 2012 Y NISHIYAMA D 19 ...
Page 161: ...7 Nov 2012 Y NISHIYAMA D 20 ...
Page 162: ...Apr 05 04 D 21 ...
Page 163: ...7 Nov 2012 Y NISHIYAMA D 22 ...
Page 164: ...D 23 13 Jan 2012 Y NISHIYAMA ...
Page 165: ...D 24 13 Jan 2012 Y NISHIYAMA ...
Page 166: ...D 25 13 Jan 2012 Y NISHIYAMA ...
Page 167: ...D 26 13 Jan 2012 Y NISHIYAMA ...